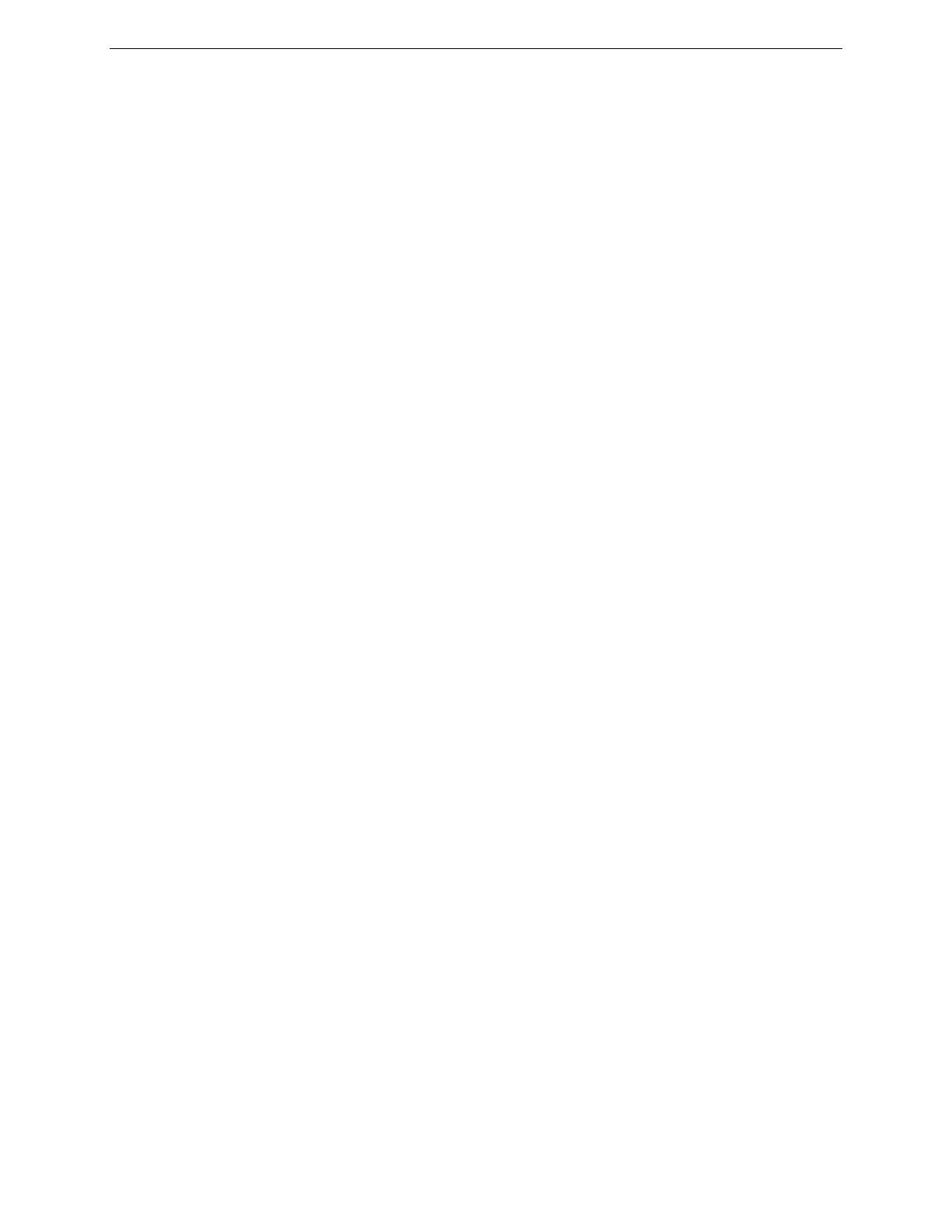
EPRI Proprietary Licensed Material
Introduction
1-2
turbines in combustion technology with dry low NO
x
and CO levels that are several orders of
magnitude lower and meet land based pollution requirements in many geographic areas.
The enabling technology of today’s advanced frame machines lies with the computer codes and
manufacturing processes developed by the aviation combustion turbine industry. The application
of these processes is inevitable under the pressure of the power generation industry to produce
power at low cost with maximum efficiency, reliability, and availability.
The power generation combustion turbines have different operating demands than the aviation
combustion turbines and the designers and developers have programs in place to advance the
technology beyond the aviation programs. Manufacturers have extended the technology to more
advanced industrial thermal barrier coatings (TBCs), oxidation resistant coatings, bond coat
technologies, large size single crystal blade and vane manufacturing processes, single digit dry
low NOx combustion systems, and integrated electronic digital control systems handling more
than 4800 I/Os.
The trends by all the major manufacturers are similar with the adoption of the aviation
technology into the flow paths, with corresponding advances in materials, cooling schemes,
coatings, and clearance control. The basic approach, inherent in each manufacturer’s design
philosophy, is evident in their general combustion turbine designs (rotors, combustion systems,
and proprietary technology) but the general trend to higher firing temperatures, pressure ratios,
efficiency, low emissions, reliability (99%), and availability (96%) goals is similar. The overall
approach to compete worldwide is based on cost per MW. Supporting the supplied equipment
with long term maintenance contracts is the internal corporate incentive to provide reliable
equipment and designs. With the merging of companies and aviation and industrial technologies
to maintain competitiveness, the large frame combustion turbines are ‘hybrids’ absorbing
technology that previously lagged by a decade before incorporation into industrial turbines. The
industrial aero-derivative and some advanced frame combustion turbines are to the point of being
the leading edge of technology in the overall combustion turbine environment in terms of
efficiency, emissions, and advanced technology.
This strategy by the manufacturers is propelled in large part by advanced combustion turbines
becoming the “only game in town” due to the current worldwide disfavor with nuclear and fossil
boiler plants. The requirement to provide sited power quickly and cost effectively, with
guarantees, is pushing these technologies forward at a rapid pace.
In order to understand the risk associated with new product introductions, the changes in the new
products must first be understood. The design evolution of these machines have been reviewed
and incorporated in a Pedigree Matrix. The pedigree matrix consolidates information for
selected combustion turbine models into a format that allows the design evolution of the
advanced machines to be reviewed and major design changes or areas of potential risk to be
evaluated.