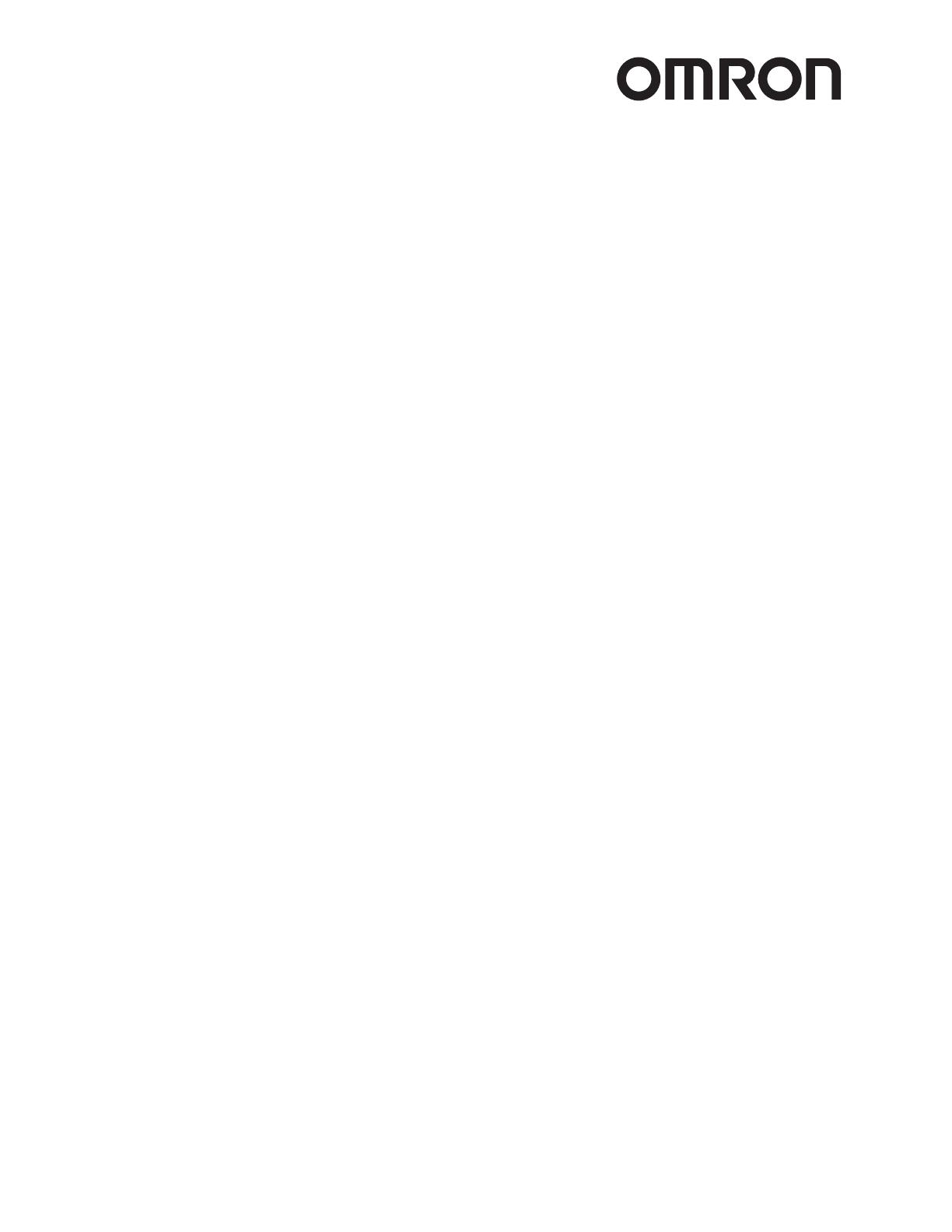
Section 1: Introduction
This document will allow the user to setup an Explicit Messaging Connection using Ethernet
socket between a Mitsubishi Q series PLC and an Omron NX-SL5700 safety CPU, through an
NX-CSG320 communications gateway.
In this configuration, the NX-SL5700 is performing the machine safety functions, incorporating
devices such as door switches, safety area scanners, ESTOP buttons, force guided relays,
remote safety IO blocks, robots with CIP Safety capabilities, and other safety components.
The PLC is performing only non-safety functions such as the monitoring of the safety devices for
annunciation on an HMI.
In order to establish the Explicit Messaging Connection, Tags in NX-SL5700 CPU need to be
exposed to EtherNet/IP, then the Q series PLC send EtherNet/IP Explicit Messages using the
Ethernet Socket Interface to read and write the data of Tags that are exposed.
This Explicit Messaging Connection will share:
• 2 boolean data points from the Q series PLC through the NX-CSG320 to the NX-SL5700
• 6 boolean data points from the NX-SL5700 through the NX-CSG320 to the Q series PLC
• IO Module status from local NX Safety IO from the NX-CSG320 to the Q series PLC.
Note: the names of the NX-SL5700 and NX-CSG320 as shown in Sysmac Studio have been
changed from the default for clarity.