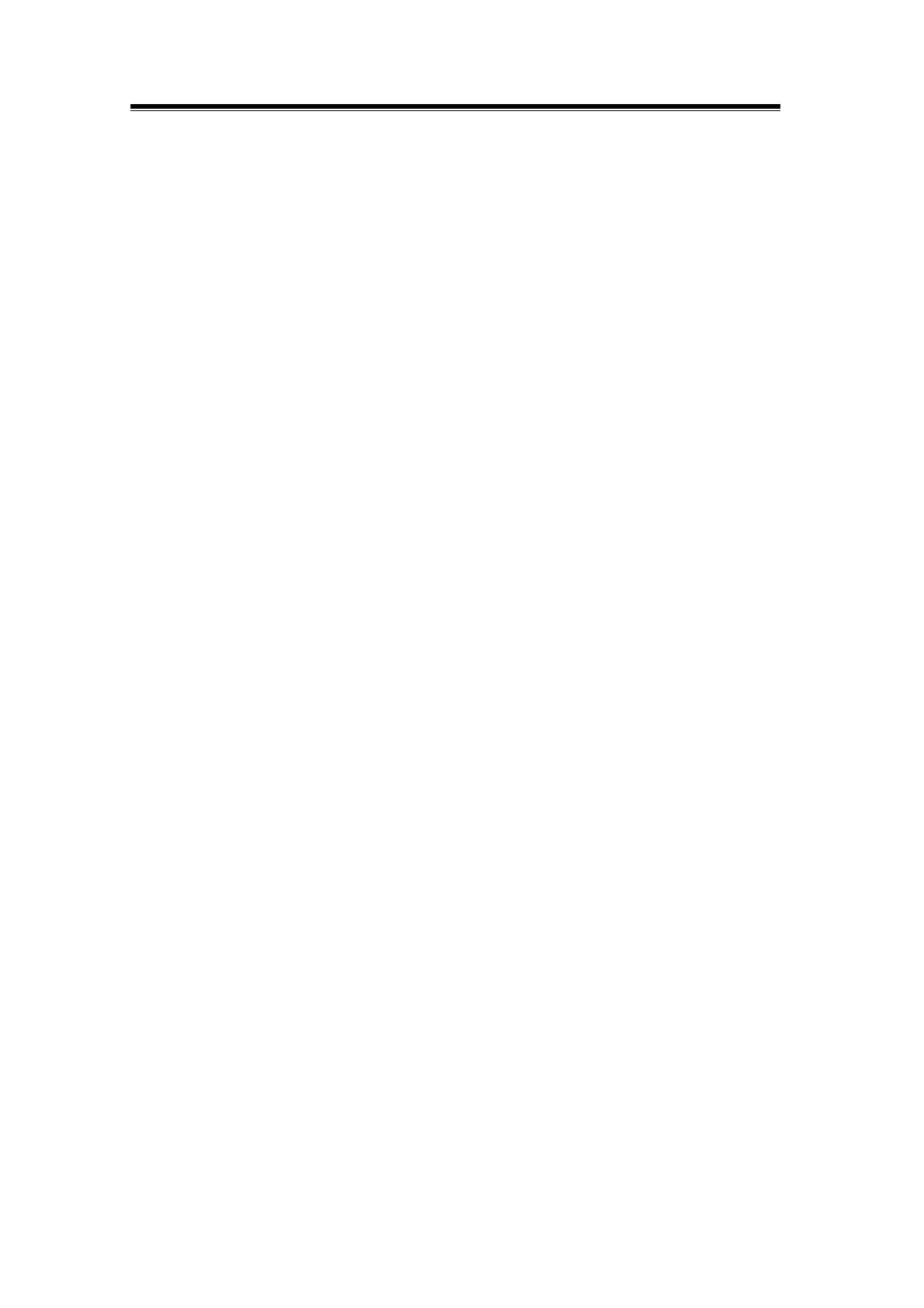
1
1-1 General Information
1. INFORMATION
Laguna Tools, Inc. is specialized to supply full range of panel saw
from 1600, 2300, 2500, 3200 to 3800mm. The outlook design of this machine
is so unique with complete cast iron bracket instead of sheet metal, enlarged
outrigger and carriage, direct dust collection outlet.
Besides of our Band Saw series, these Table Saw series are also innovative
products. Please enjoy your operation on this machine and if you have any
comment to improve them, please don’t hesitate to contact us through your
agent.
As woodworking machines with the quality design, our Panel Saw series are
designed to well rip solid wood, chipboard, berboard, plywood and similar
materials. During the usage, be careful of rigidity of working materials and
don’t try forbidden materials such as low ash point metals and high sti stone,
etc. HSS (High Speed Steel) saw blade and milling tools should not be used.
The saw blade made in accordance with EN847-1: 1997 shall be used on the
machine. Generally speaking, this machine will be installed as the following
conditions:
1) Supply voltage: 0.9 - 1.1 normal supply voltage
2) Source frequency: 0.99 - 1.01 normal frequency
3) Ambient temperature: 5°C - 40°C.
4) Altitude: shall be at altitudes up to 1000m above the middle sea level.
5) Relative humidity: not exceed 50% at 40°C.
6) Atmosphere: Free from excessive dust, acid fume, corrosive gases and
salt.
7) Avoid exposing to direct sunlight or heat rays which can change the
environmental temp.
8) Avoid exposing to abnormal vibration.
9) Electrical equipment shall withstand the eects of transportation and
storage temperature within a range of -25°C to 55°C. Then, for short
periods, it does not exceed 24 hours at up to +70°C.
This machine was designed for certain applications only. We strongly
recommend that this machine NOT be modied and/or used for any application
which for other than its design.
If you have any question, which is relative to its application, DO NOT use the
machine until you have had detail instruction from your dealer.