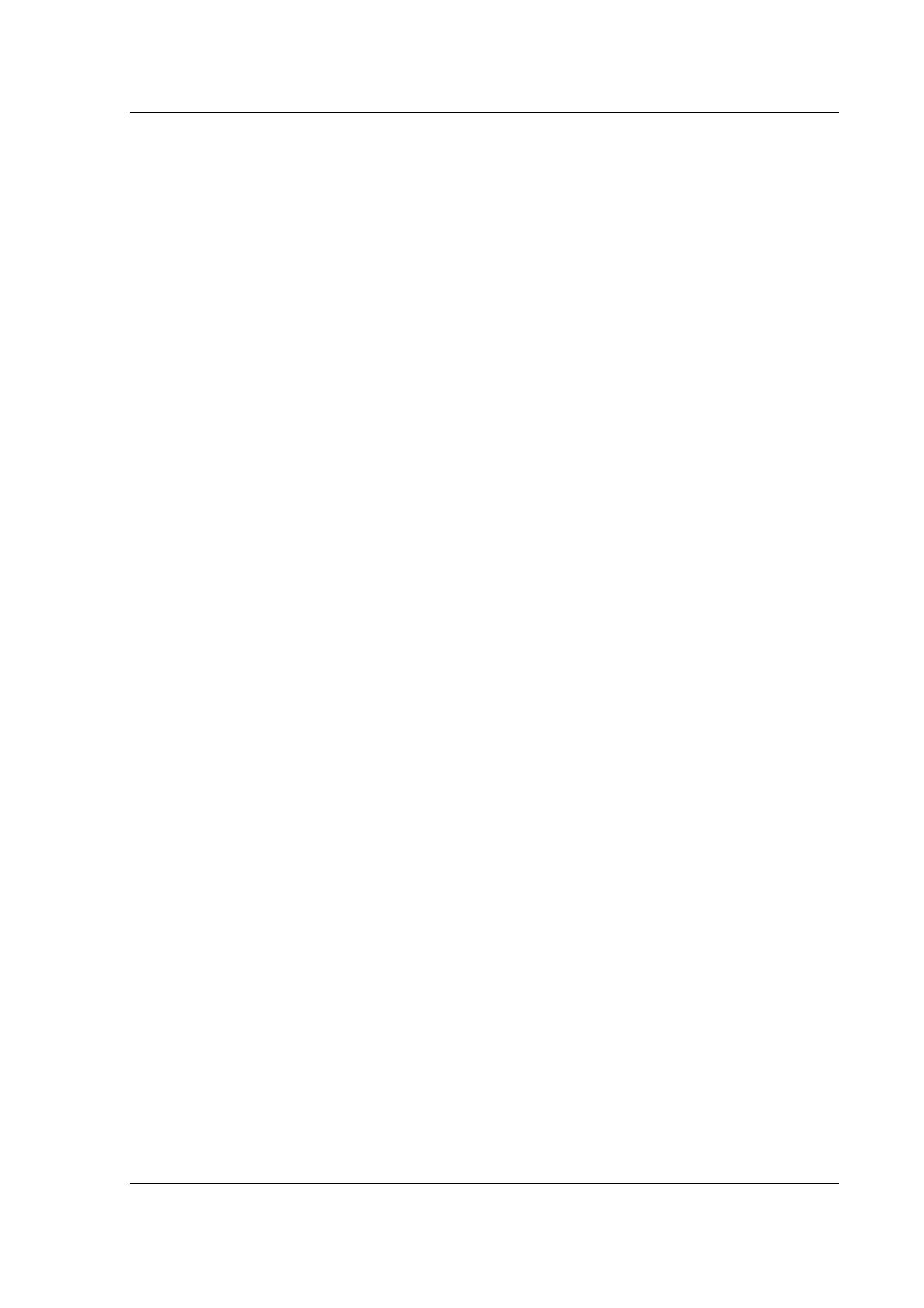
01/10 347LB 444 K-40
I
Operating Manual Potassium Meter
LB 444 K-40
Contents
1 GENERAL INFORMATION ..................................................... 1
2 OVERVIEW........................................................................... 2
3 SYSTEM DESCRIPTION......................................................... 4
4 INSTALLATION OF THE DETECTORS..................................... 5
4.1 Selection of the Measuring Site .............................................................. 5
4.2 Installation of the Detector LB 5430 on a Bunker................................... 6
4.3 Installation of the Detector LB 5402 in a Bunker.................................... 7
4.4 Measurement in a Pipe ........................................................................... 7
4.5 Measurement on a Conveyor Belt ........................................................... 9
4.6 Installation of the Evaluation Electronics ............................................. 10
4.7 Installation of the Detector .................................................................. 10
4.7.1 Installation in a Container .............................................................. 10
5 CONNECTIONS................................................................... 11
5.1.1 Evaluation Unit LB 444 K-40........................................................... 11
5.2 Evaluation Unit LB 444 K-40 ................................................................. 13
5.2.1 General Description....................................................................... 13
5.2.2 Display........................................................................................ 13
5.2.3 Keypad Function ........................................................................... 13
5.2.4 Softkeys...................................................................................... 14
5.2.5 Menu Structure............................................................................. 14
5.2.6 Menu Potassium Content Measurement ............................................ 15
6 SOFTWARE FUNCTIONS AND SYSTEM CONFIGURATION ... 19
6.1 General Data......................................................................................... 19
6.2 Operating Mode .................................................................................... 20
6.3 Parameter............................................................................................. 21
6.4 Product Data......................................................................................... 23
6.5 Calibrate............................................................................................... 24
6.6 Live Display .......................................................................................... 26
6.7 Service Menu ........................................................................................ 26
7 GETTING STARTED............................................................. 27
7.1 Quick Installation Overview.................................................................. 27
7.2 Getting Started..................................................................................... 28
7.2.1 Basic Settings............................................................................... 28
7.2.2 Calibration ................................................................................... 29
7.2.3 Checking the Calibration ................................................................ 31
7.3 Live Display .......................................................................................... 31
7.4 Correcting the Results: Addition and Multiplication .............................. 32
7.4.1 Additive Constant.......................................................................... 32
7.4.2 Multiplication Factor ...................................................................... 32
7.5 Automatic Measuring Time Switchover................................................. 33
7.6 Batch Measurement.............................................................................. 34
7.7 Radiating Interference Detection.......................................................... 35
7.8 Error Messages ..................................................................................... 36
7.8.1 Acknowledging Error Messages ....................................................... 36