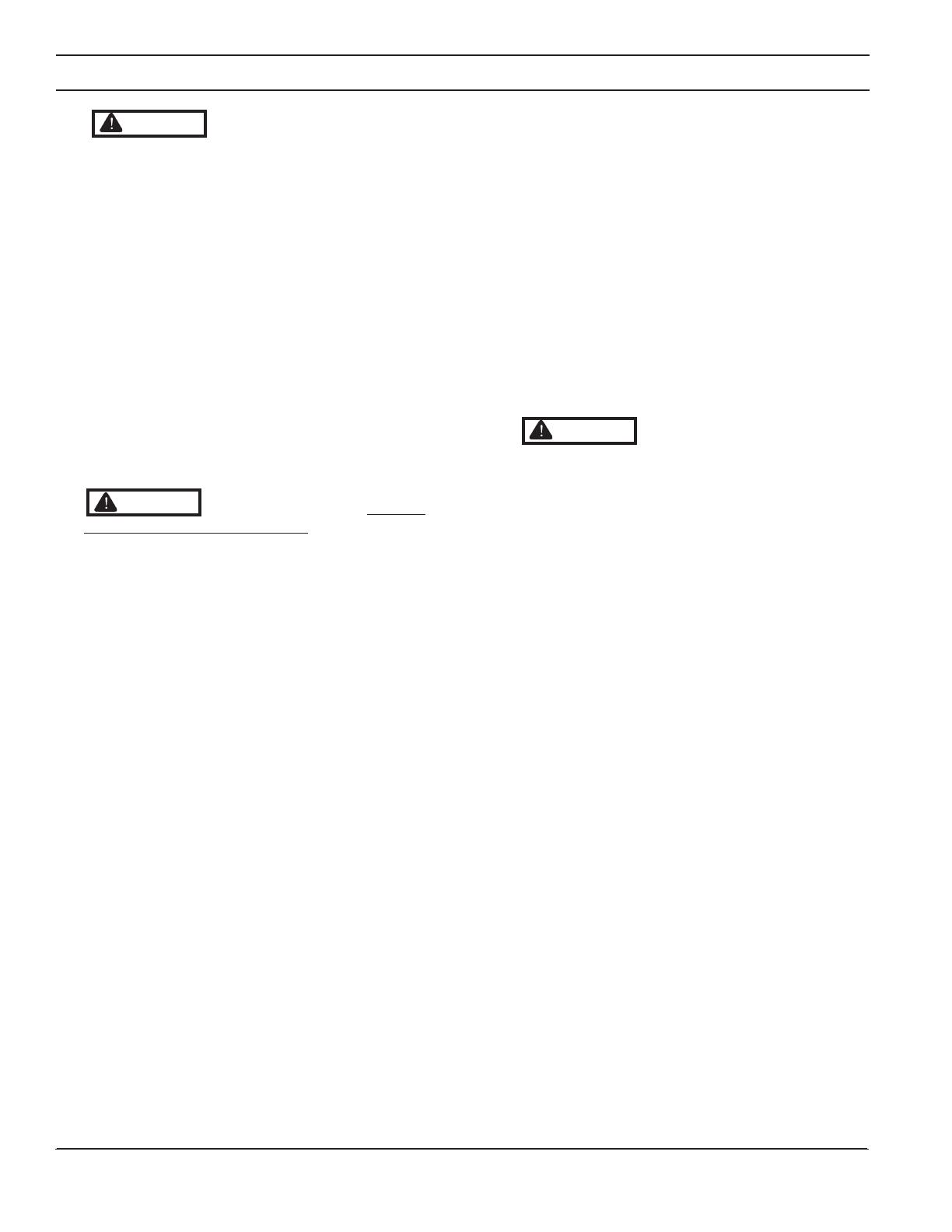
10
103448-10- 6/18
A. Installation must conform to the requirements
of the authority having jurisdiction in or, in the
absence of such requirements, to the National
Fuel Gas Code, ANSI Z223.1/NFPA 54, and/or
Natural Gas and Propane Installation Code, CAN/
CSA B149.1.
Where required by the authority having
jurisdiction, the installation must conform to the
Standard for Controls and Safety Devices for
Automatically Fired Boilers, ANSI/ASME CSD1.
B. Boiler is certified for installation on combustible
flooring. Do not install boiler on carpeting.
C. Provide clearance between boiler jacket and
combustible material in accordance with local fire
ordinance. Refer to Figure 2A or 2B for minimum
listed clearances from combustible material.
Recommended service clearance is 24 in. (610
mm) from left side, front, top and rear of the boiler.
Recommended front clearance may be reduced
to the combustible material clearance providing:
1. Access to boiler front is provided through a
door or removable front access panel.
III. Pre-Installation and Boiler Mounting
2. Access is provided to the condensate trap
located underneath the heat exchanger.
3. Access is provided to thermal link
located at boiler rear.
D. Protect gas ignition system components from
water (dripping, spraying, rain, etc.) during boiler
operation and service (circulator replacement,
condensate trap, control replacement, etc.).
E. Provide combustion and ventilation air in
accordance with section “Air for Combustion
and Ventilation,” of National Fuel Gas Code, ANSI
Z223.1/NFPA 54, or Clause 8.2, 8.3, or 8.4 of
Natural Gas and Propane Installation Code, CAN/
CSA B149.1, or applicable provisions of local
building Codes.
F. The boiler should be located so as to minimize
the length of the vent system. The combustion
air piping must terminate where outdoor air is
available for combustion and away from areas that
may contaminate combustion air. In particular,
avoid areas near chemical products containing
chlorines, chlorofluorocarbons, paint removers,
cleaning solvents and detergents. Avoid areas
containing saw dust, loose insulation fibers, dry
wall dust etc.
G. General
1. Alpine boilers are intended for installations
in an area with a floor drain or in a suitable
drain pan to prevent any leaks or relief valve
discharge to cause property damage.
2. Alpine boilers are not intended to support
external piping and venting. All external piping
and venting must be supported independently
of the boiler.
3. Alpine boilers must be installed level to
prevent condensate from backing up inside the
boiler.
4. Alpine boilers can be installed either as
floor standing (ALP080B through ALP285B)
or as wall hung (ALP080B through ALP210B).
WARNING
WARNING
NOTICE Due to the low water content of the
boiler, mis-sizing of the boiler with regard to
the heating system load will result in excessive
boiler cycling and accelerated component
failure. U.S. Boiler Company DOES NOT
warrant failures caused by mis-sized boiler
applications. DO NOT oversize the boiler to
the system. Multiple boiler installations greatly
reduce the likelihood of boiler oversizing.
Explosion Hazard.
Asphyxiation Hazard. Electrical Shock Hazard.
Installation of this boiler should be undertaken
only by trained and skilled personnel from
a qualified service agency. Follow these
instructions exactly.
Improper installation, adjustment, service,
or maintenance can cause property damage,
personal injury or loss of life.
Asphyxiation Hazard. Models
with Two-Pipe Vent Connector:
Apply supplied dielectric grease to gasket
inside vent section of two-pipe vent connector.
Failure to apply the grease could result in flue
gas leaks from gasket rupture during vent
pipe installation or gasket deterioration due to
condensate exposure.
Indicates a potentially
hazardous situation which, if not avoided,
could result in death, serious injury or
substantial property damage.
WARNING
NOTICE Avoid operating this boiler in an
environment where sawdust, loose insulation
fibers, dry wall dust, etc. are present. If boiler
is operated under these conditions, the
burner interior and ports must be cleaned and
inspected daily to insure proper operation.