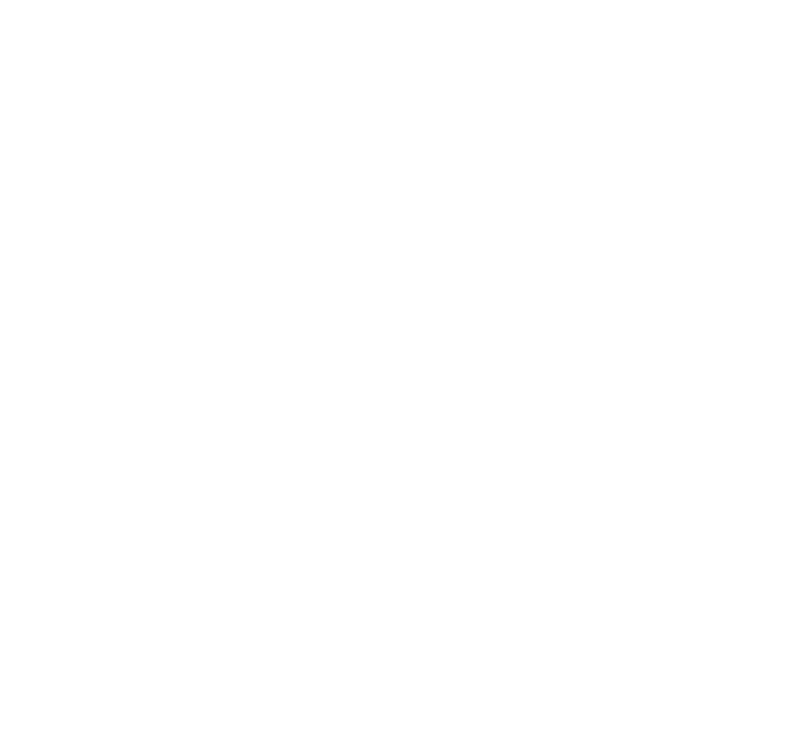
4
TABLE OF CONTENTS
Step 3: Changing the Processing Board’s MAC Address . . . . . . . . . . . . .18
Step 4: Determining the Processing Board’s IP Address . . . . . . . . . . . . .19
Step 5: Connecting to the Processing Board via RDP . . . . . . . . . . . . . . .21
Step 6: Acquiring Images Using the pylon Viewer . . . . . . . . . . . . . . . . . 22
NEXT STEPS . . . . . . . . . . . . . . . . . . . . . . . . . . . . . . . . . . . . . . . . . . . . . . . . . 23
Developer Resources . . . . . . . . . . . . . . . . . . . . . . . . . . . . . . . . . . . . . . . . . . . 23
Technical Support . . . . . . . . . . . . . . . . . . . . . . . . . . . . . . . . . . . . . . . . . . . . . . 23
SPECIFICATIONS . . . . . . . . . . . . . . . . . . . . . . . . . . . . . . . . . . . . . . . . . . . . .24
Camera Specifications . . . . . . . . . . . . . . . . . . . . . . . . . . . . . . . . . . . . . . . . . . 24
Processing Board Specifications . . . . . . . . . . . . . . . . . . . . . . . . . . . . . . . . . 25
Carrier Board Specifications . . . . . . . . . . . . . . . . . . . . . . . . . . . . . . . . . . . . . 25
Lens Specifications . . . . . . . . . . . . . . . . . . . . . . . . . . . . . . . . . . . . . . . . . . . . . 26
Power Supply Specifications . . . . . . . . . . . . . . . . . . . . . . . . . . . . . . . . . . . . 26
Block Diagram of Carrier Board . . . . . . . . . . . . . . . . . . . . . . . . . . . . . . . . . . 27
DISCLAIMER AND LICENSING INFORMATION . . . . . . . . . . . . . . . . . . . . . 28
Disclaimer . . . . . . . . . . . . . . . . . . . . . . . . . . . . . . . . . . . . . . . . . . . . . . . . . . . . . 28
Software Licensing . . . . . . . . . . . . . . . . . . . . . . . . . . . . . . . . . . . . . . . . . . . . . 29