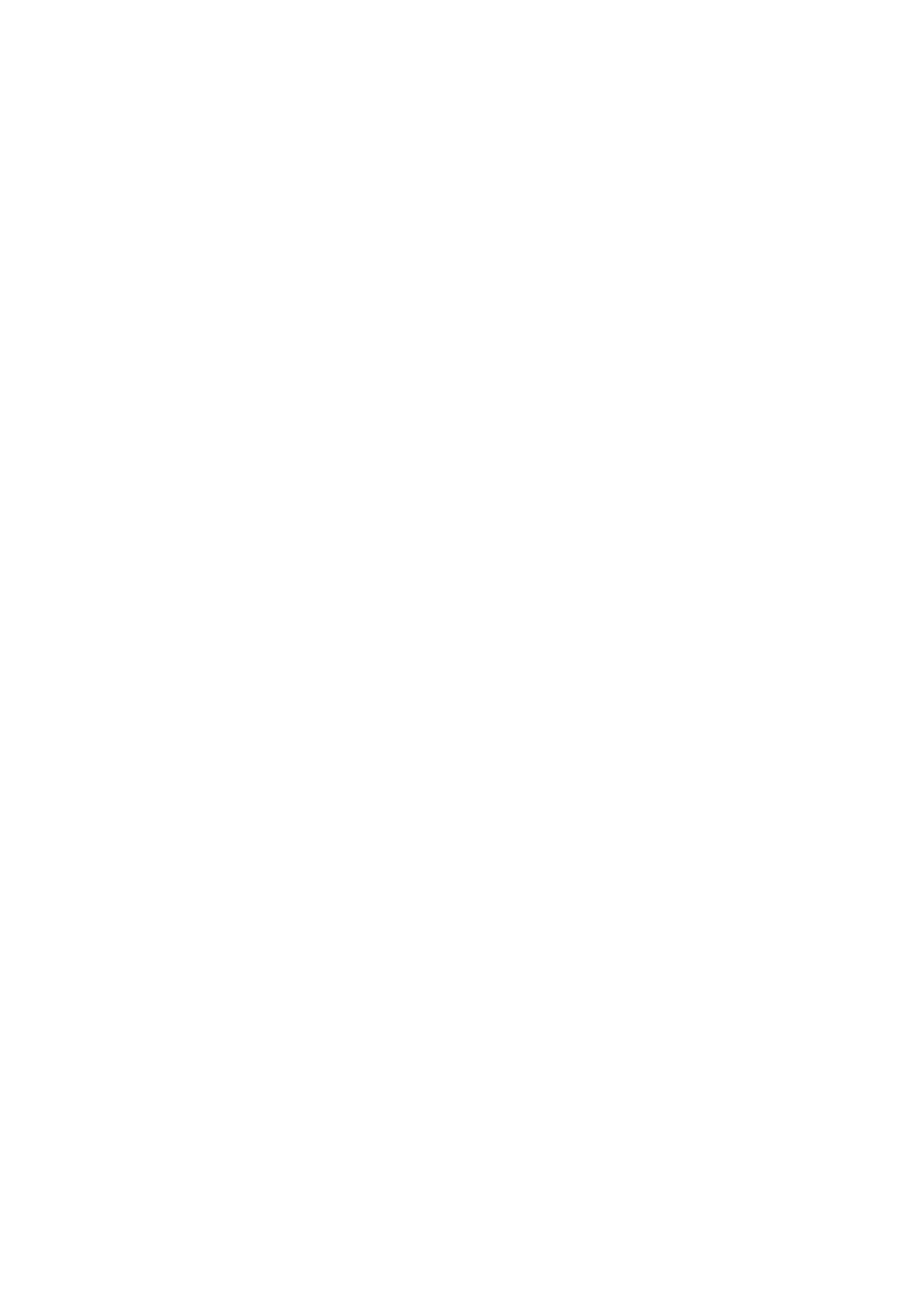
4
induction air inlet and filter is not longer located on the lower part of the front engine cowling (this is
now for cabin heating purposes), but on the rear upper right hand side of it, as seen from the cabin.
The main difference between a turbocharger and a supercharger is that the latter is mechanically
driven by the engine crankshaft, whereas the former is driven by the exhaust gases acting on a
turbine which, in turn, drives a compressor through which the induction air passes on its way to the
cylinder inlet valves. As this compressed air reaches considerable temperatures, an additional
intercooler is often located downstream of the compressor. The TAE 125-1 features such an
intercooler, the cooling outside air originating from the right upper inlet in the front of the engine nose
cowl, as seen from the cabin.
Turbochargers are fitted with a so-called waste-gate which can either be fixed or of the variable type,
either manually, or automatically by hydraulic or, as is the case for the TAE 125-01, mechanical
means. The waste-gate is a valve which offers free passage to a part of the exhaust gases on their
way to the exhaust, while another part of the gases is deviated towards the turbine driving the
compressor. In the variable type, the wastegate is modulated (usually automatically) in order to admit
more or less gases to the turbine, depending on the density altitude and the power setting.
Turbochargers are compact pieces of equipment. However, as they can reach rotation speeds in
excess of 100000 RPM, they are liable to become extremely hot. This is the reason why, whenever a
turbocharger is installed, the temperature of the exhaust gases must be kept in check and may not
exceed a maximum value, which is 900°C for the TAE 125-01. Nonetheless, as the temperature
regulation of the exhaust gases is automatically taken care of, you will not find an EGT (exhaust gas
temperature) indicator on the instrument panel.
One might rightly believe that the basic purpose of the addition of a turbocharger is to allow higher
cruising altitudes. With the TAE 121-1 engine, it is only 16500 ft for the Robin 135CDI. So, why a
turbocharger? Fact is that many diesel engines perform well without it, but lack somewhat “spirit”.
The main reason for the turbocharger is to increase the volumetric efficiency of the cylinders. In other
words, the more air can be crammed into the cylinders during the induction stroke, the greater will be
the power output. In addition, the presence of an intercooler, located downstream of the compressor,
contributes even more to improve efficiency. Indeed, compressed air heats up and tends to expand
when leaving the turbocharger, but the cooling effect of the intercooler significantly reduces its
volume, thereby increasing its specific mass which leads to a greater weight of air entering the
cylinders at each induction stroke. Both the turbocharger and intercooler, in association with the
constant speed propeller system (see below), contribute to the fact that the performances of the
diesel equipped Robin are fairly close to the original aircraft, despite the considerable lower HP rating.
The engine develops 132.8 HP at 2300 RPM (propeller RPM). However, the propeller is not driven
directly by the crankshaft but through a gearbox whose purpose it is to reduce the
propeller RPM by 1.69. This means that if the propeller RPM is 2300, the crankshaft
rotates in fact at 3887 RPM. In other words, if the TAE 125-01’s propeller would rotate at the
same speed as the crankshaft, i.e. nearly 4000 RPM, the noise would probably exceed tolerable values
and the propeller efficiency would suffer severe losses at the tips.
Besides being driven by the gearbox, and despite the fact that only one single thrust lever is available
on the control pedestal, the propeller is referred to as a constant speed type. Perhaps this calls for
some explanations:
1°) The usual constant speed system implies a variable pitch propeller, i.e. a propeller whose blade
angle can be changed (see PILOT NOTES). A propeller lever allows the pilot to select a chosen RPM
for a selected manifold air pressure, or MAP, which is set by means of the throttle. Variable pitch
propellers are mostly fitted with a so-called constant speed unit, or CSU. The CSU is controlled by
normal engine oil. It includes a flyweight and valve system which ensures that, once a certain RPM
value has been selected for cruise, this value remains unchanged even when the aerodynamic forces
on the propeller vary, hence the term “constant speed propeller”. Remember that on a fixed pitch
propeller, i.e. a propeller whose blade angle cannot be changed, if you increase speed by diving the
Versie oktober 07