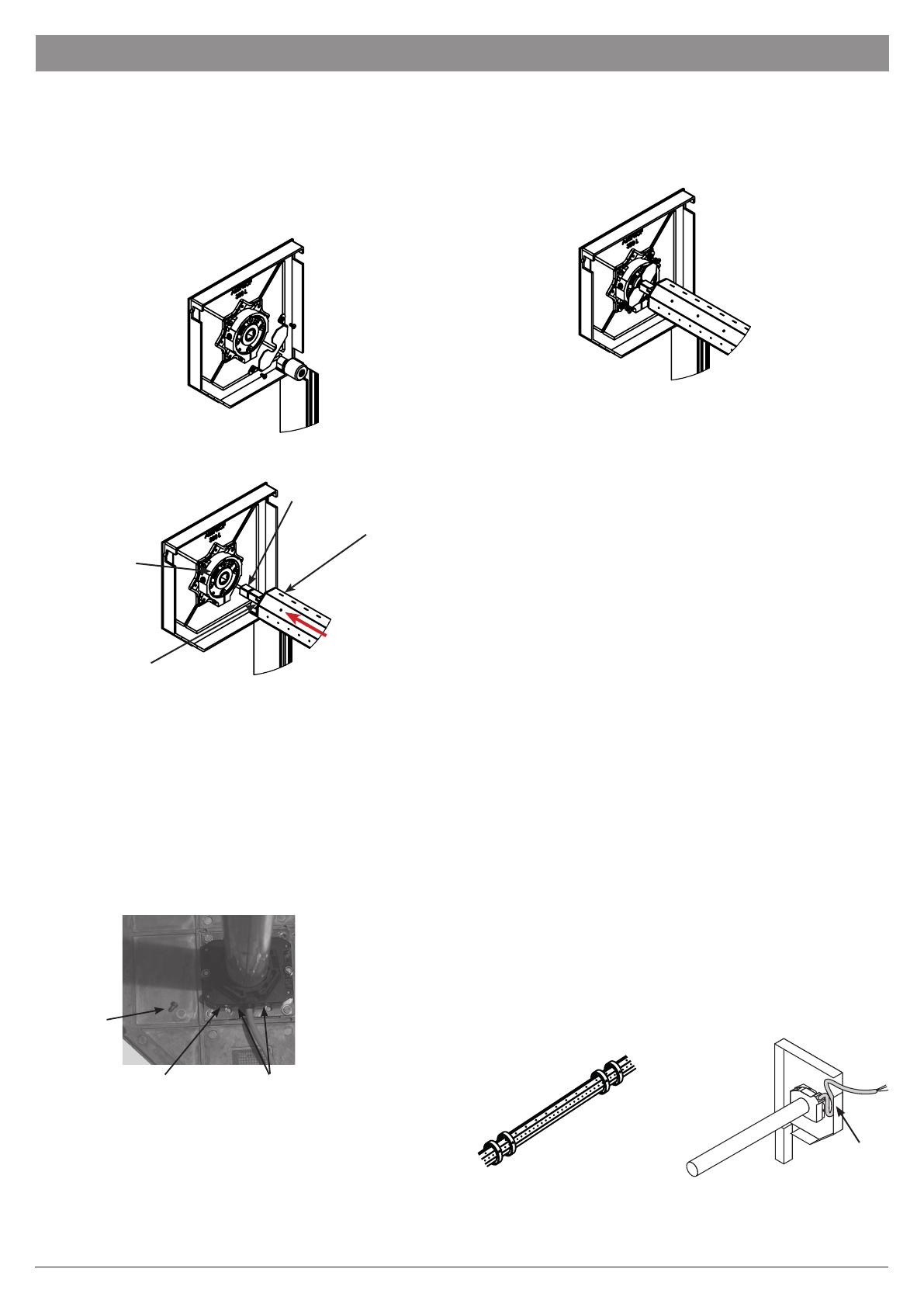
6MK3001RP April 2023 R1
Anti-Fall Back Device
Note: The rivet securing the dummy end into the axle is use for
transport purposes only and MUST be removed before installing
the axle.
i. Remove the retaining plate from the pre-built end plate (see
Drawing A). If retaining plate is not on the endplate, check
your accessories box.
ii. Loosen the safety collar on the dummy end shaft and extend
the shaft fully into the safety brake (see Drawing B).
iii. Attach the motor side of the axle to the opposite end plate.
iv. Re-install the retaining plate over the safety brake and onto
the end plate (see Drawing C). Ensure the retaining plate sits
inside the shaft groove to prevent movement.
v. Fix the reaining plate securely to the end plate using the pre-
existing fixings supplied or spare fixings from the accessories
kit.
vi. Slide the safety collar tight up to the dummy end and tighten.
i. Fasten the motor end of the axle, using the bracket supplied,
to the other end plate using the screws provided and the
prepared tapped holes in the end plate.
ii. Ensure that the motor limits are facing down and that the
override hole is towards the chamfered front end of the
end plate.
iii. Ensure that the collars are the correct way around
(see Drawing C).
iv. Ensure the motor power lead is securely fastened to the end
plate and away from the curtain. – (see Drawing D).
v. You must ensure that you allow for a drip loop in the motor
cable to prevent water from running down the cable and into
the motor. Cable ties can be attached to the motor cable
to act as drip loop to prevent water entering the motor.
D
Screw &
Washer
Override Exit Motor Limits C
Fix the Motor End of the Axle
Drip Loop
06. INSTALL THE AXLE ASSEMBLY (CONTINUED)
IMPORTANT INFORMATION: In the event that the door fails and the safety brake is triggered to prevent the door from falling, the safety
brake MUST BE REPLACED with a like-for-like brake. This includes activation of the interlock switch OR turning of the inner dial.
A
Detail 1:
Remove retaining plate from pre-build endplate.
If retaining plate is not on the endplate, check your
accessories box.
C
Detail 2:
Slide axle into safety brake. Attach motor side to
the endplate.
D
Detail 3:
Install retaining plate back over the safety brake
and onto the endplate as shown. Ensure plate sits
inside of shaft grove to prevent movement. Use
pre-existing fixings that was supplied on the endplate
or fixings can be found inside of fixing kit
E
Detail 4:
Push fixing clip upto axle as close as possible. Screw clip to axle
to prevent shaft movement.
WEIGHT:3.89
A3
SHEET 1 OF 1
SCALE: 1:20
STATUS:
REVISION:
MATERIAL:
DATE
FINISH:
UNLESS OTHERWISE SPECIFIED:
(ALL DIMENSIONS ARE IN 'mm'
)
TOLERANCES:-
LINEAR:
ANGULAR:
APPV'D
CHK'D
DRAWN
CONFIDENTIAL. COPYRIGHT
© OF SECURITY WINDOWS AND SHUTTERS UK LTD (SWS UK LTD).
THE REPRODUCTION OR TRANSMISSION OF ALL OR PART OF THIS DOCUMENT, WHETHER BY
PHOTOCOPYING OR STORING IN ANY MEDIUM BY ELECTONIC MEANS OR OTHERWISE,
WITHOUT THE WRITTEN PERMISSION OF SWS UK LTD, IS PROHIBITED.
ALL SUPPLIERS OR COMPONENTS, ARTICLES, MIXTURES OR SUBSTANCES TO SWS UK LTD, OR ANY
AFFILIATE OF SWS UK LTD, MUST BE FULLY COMPLIANT WITH EU REGULATION (EC) NO. 1907/2006
(REACH) AND ALL APPLICABLE RELATED LEGISLATION.
NAME
Stock Code:
TITLE:
PROJECT:
Retaining plate installation
N/A
Part/Assy locale: C:\PDM\Library\Assembly File\
Drawing locale: C:\Users\thomasb\Security Window Shutters Limited\Development - Engineering\Engineering\03 - Projects\01 - Current\P161 - Allugaurd\03 - Documents\04 - General Documents\Marketing Material\CAD Files\Fitting Instructions\
AB
BA
B
C
D
E
G
H
J
K
L
N
R
S
T
U
V
W
X
Y
Z
AC
AD
AE AG
AH
AJ
AK
AL
AP
AR
AU
AV
AW
AX
AY
AZ
BC
BD
BF
BG
BH
BJ
BK
BL
BM
BN
BP
BR
BT
BU
BV
BW
BX
BZ
A
A A
B B
C C
D D
E E
F F
8
8
7
7
6
6
5
5
4
4
3
3
2
2
1
1
Notes:
N/A
SeceuroGlide Alluguard 77
Assembly
CN
ZONE
DESCRIPTION
APPROVED
DATE
REV
MD No.:
DO NOT SCALE DRAWING
mm
deg
A
Safety Brake
Shaft
Dummy End
Safety Collar
or Jubilee Clip
depending on
configuration
B
A
Detail 1:
Remove retaining plate from pre-build endplate.
If retaining plate is not on the endplate, check your
accessories box.
C
Detail 2:
Slide axle into safety brake. Attach motor side to
the endplate.
D
Detail 3:
Install retaining plate back over the safety brake
and onto the endplate as shown. Ensure plate sits
inside of shaft grove to prevent movement. Use
pre-existing fixings that was supplied on the endplate
or fixings can be found inside of fixing kit
E
Detail 4:
Push fixing clip upto axle as close as possible. Screw clip to axle
to prevent shaft movement.
WEIGHT:3.89
A3
SHEET 1 OF 1
SCALE: 1:20
STATUS:
REVISION:
MATERIAL:
DATE
FINISH:
UNLESS OTHERWISE SPECIFIED:
(ALL DIMENSIONS ARE IN 'mm'
)
TOLERANCES:-
LINEAR:
ANGULAR:
APPV'D
CHK'D
DRAWN
CONFIDENTIAL. COPYRIGHT
© OF SECURITY WINDOWS AND SHUTTERS UK LTD (SWS UK LTD).
THE REPRODUCTION OR TRANSMISSION OF ALL OR PART OF THIS DOCUMENT, WHETHER BY
PHOTOCOPYING OR STORING IN ANY MEDIUM BY ELECTONIC MEANS OR OTHERWISE,
WITHOUT THE WRITTEN PERMISSION OF SWS UK LTD, IS PROHIBITED.
ALL SUPPLIERS OR COMPONENTS, ARTICLES, MIXTURES OR SUBSTANCES TO SWS UK LTD, OR ANY
AFFILIATE OF SWS UK LTD, MUST BE FULLY COMPLIANT WITH EU REGULATION (EC) NO. 1907/2006
(REACH) AND ALL APPLICABLE RELATED LEGISLATION.
NAME
Stock Code:
TITLE:
PROJECT:
Retaining plate installation
N/A
Part/Assy locale: C:\PDM\Library\Assembly File\
Drawing locale: C:\Users\thomasb\Security Window Shutters Limited\Development - Engineering\Engineering\03 - Projects\01 - Current\P161 - Allugaurd\03 - Documents\04 - General Documents\Marketing Material\CAD Files\Fitting Instructions\
AB
BA
B
C
D
E
G
H
J
K
L
N
R
S
T
U
V
W
X
Y
Z
AC
AD
AE AG
AH
AJ
AK
AL
AP
AR
AU
AV
AW
AX
AY
AZ
BC
BD
BF
BG
BH
BJ
BK
BL
BM
BN
BP
BR
BT
BU
BV
BW
BX
BZ
A
A A
B B
C C
D D
E E
F F
8
8
7
7
6
6
5
5
4
4
3
3
2
2
1
1
Notes:
N/A
SeceuroGlide Alluguard 77
Assembly
CN
ZONE
DESCRIPTION
APPROVED
DATE
REV
MD No.:
DO NOT SCALE DRAWING
mm
deg
A
Detail 1:
Remove retaining plate from pre-build endplate.
If retaining plate is not on the endplate, check your
accessories box.
C
Detail 2:
Slide axle into safety brake. Attach motor side to
the endplate.
D
Detail 3:
Install retaining plate back over the safety brake
and onto the endplate as shown. Ensure plate sits
inside of shaft grove to prevent movement. Use
pre-existing fixings that was supplied on the endplate
or fixings can be found inside of fixing kit
E
Detail 4:
Push fixing clip upto axle as close as possible. Screw clip to axle
to prevent shaft movement.
WEIGHT:3.89
A3
SHEET 1 OF 1
SCALE: 1:20
STATUS:
REVISION:
MATERIAL:
DATE
FINISH:
UNLESS OTHERWISE SPECIFIED:
(ALL DIMENSIONS ARE IN 'mm'
)
TOLERANCES:-
LINEAR:
ANGULAR:
APPV'D
CHK'D
DRAWN
CONFIDENTIAL. COPYRIGHT
© OF SECURITY WINDOWS AND SHUTTERS UK LTD (SWS UK LTD).
THE REPRODUCTION OR TRANSMISSION OF ALL OR PART OF THIS DOCUMENT, WHETHER BY
PHOTOCOPYING OR STORING IN ANY MEDIUM BY ELECTONIC MEANS OR OTHERWISE,
WITHOUT THE WRITTEN PERMISSION OF SWS UK LTD, IS PROHIBITED.
ALL SUPPLIERS OR COMPONENTS, ARTICLES, MIXTURES OR SUBSTANCES TO SWS UK LTD, OR ANY
AFFILIATE OF SWS UK LTD, MUST BE FULLY COMPLIANT WITH EU REGULATION (EC) NO. 1907/2006
(REACH) AND ALL APPLICABLE RELATED LEGISLATION.
NAME
Stock Code:
TITLE:
PROJECT:
Retaining plate installation
N/A
Part/Assy locale: C:\PDM\Library\Assembly File\
Drawing locale: C:\Users\thomasb\Security Window Shutters Limited\Development - Engineering\Engineering\03 - Projects\01 - Current\P161 - Allugaurd\03 - Documents\04 - General Documents\Marketing Material\CAD Files\Fitting Instructions\
AB
BA
B
C
D
E
G
H
J
K
L
N
R
S
T
U
V
W
X
Y
Z
AC
AD
AE AG
AH
AJ
AK
AL
AP
AR
AU
AV
AW
AX
AY
AZ
BC
BD
BF
BG
BH
BJ
BK
BL
BM
BN
BP
BR
BT
BU
BV
BW
BX
BZ
A
A A
B B
C C
D D
E E
F F
8
8
7
7
6
6
5
5
4
4
3
3
2
2
1
1
Notes:
N/A
SeceuroGlide Alluguard 77
Assembly
CN
ZONE
DESCRIPTION
APPROVED
DATE
REV
MD No.:
DO NOT SCALE DRAWING
mm
deg
C