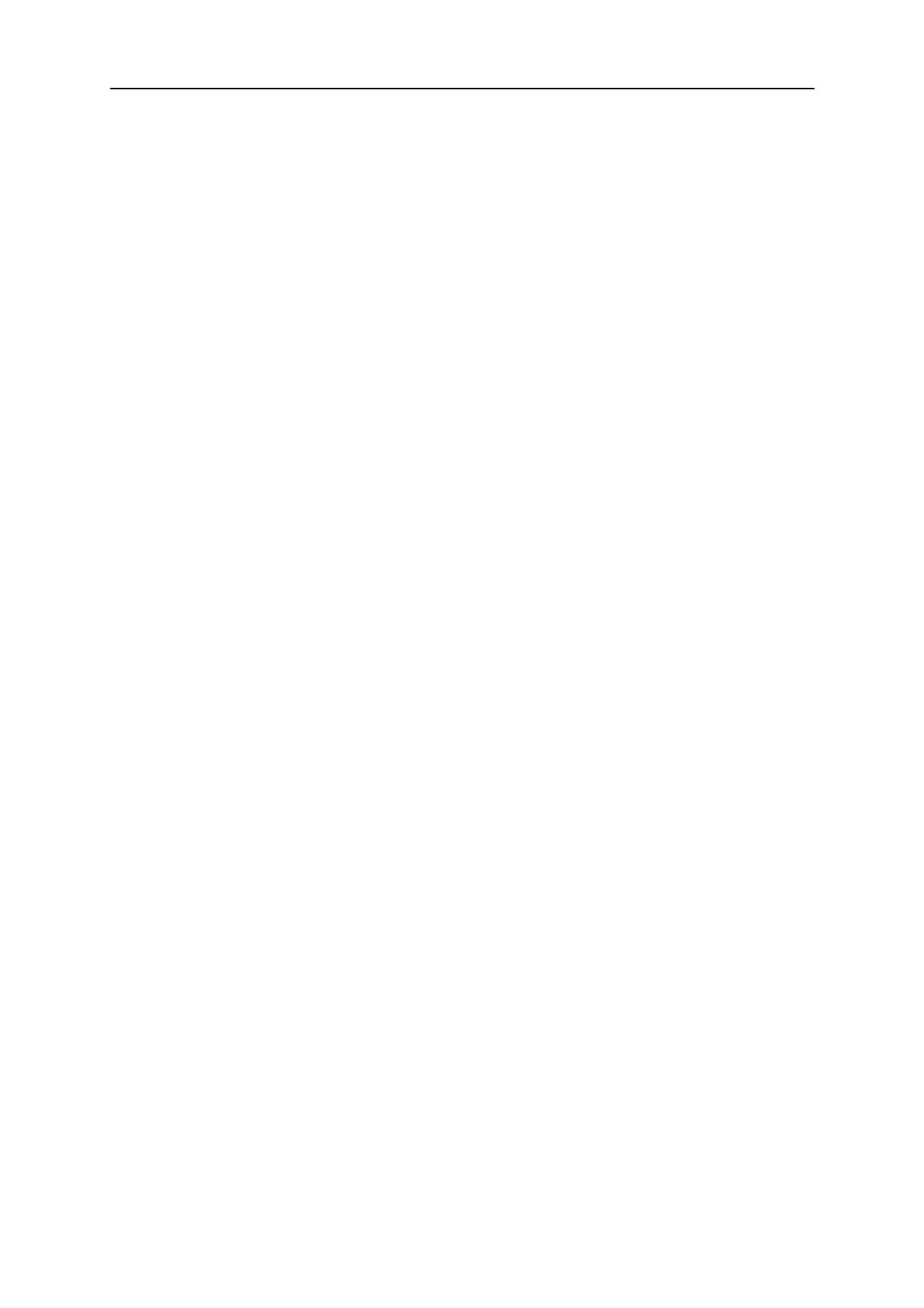
TABLE OF CONTENTS
0463 601 001 © ESAB AB 2019
1
SAFETY ....................................................................................................... 4
1.1 Meaning of symbols ............................................................................... 4
1.2 Safety precautions ................................................................................. 4
2
INTRODUCTION.......................................................................................... 7
2.1 Equipment ............................................................................................... 7
2.2 Before setup of your WeldCloud™ Universal Connector................... 7
2.2.1 Charging the lithium-ion battery ........................................................... 7
3
TECHNICAL DATA ...................................................................................... 8
4
INSTALLATION............................................................................................ 9
4.1 Main components ................................................................................... 9
4.2 Inserting the lithium-ion battery into the electronics box .................. 9
4.3 Installing WeldCloud™UniversalConnector ...................................... 10
4.3.1 Replacing the OKC connector.............................................................. 11
4.4 Setup of WeldCloud™UniversalConnector........................................ 12
4.4.1 Downloading and installing the UCMon application ............................. 12
4.4.2 Powering up the WeldCloud™ Universal Connector............................ 13
4.4.3 Pairing the Android device to the WeldCloud™ Universal Connector.. 13
4.4.4 Connecting the WeldCloud™ Universal Connector to a local Wi-Fi
network.................................................................................................
14
4.4.5 Connecting the WeldCloud™ Universal Connector to WeldCloud™
Cloud Platform......................................................................................
15
4.4.6 Changing the default name of the WeldCloud™ Universal Connector. 16
4.4.7 Setup additional weld parameters ........................................................ 16
5
OPERATION ................................................................................................ 18
5.1 Power supply .......................................................................................... 18
5.2 Operation modes .................................................................................... 18
5.3 Status indication LEDs .......................................................................... 18
5.4 Measuring and storing data................................................................... 20
6
MAINTENANCE........................................................................................... 21
6.1 Inspection and cleaning......................................................................... 21
6.2 Validation ................................................................................................ 21
6.3 Charging the lithium-ion battery ........................................................... 21
7
TROUBLESHOOTING ................................................................................. 22
8
ORDERING SPARE PARTS ........................................................................ 23
DIAGRAM ............................................................................................................ 24
ORDERING NUMBERS....................................................................................... 25
WEAR PARTS...................................................................................................... 26
ACCESSORIES ................................................................................................... 27
Rights reserved to alter specifications without notice.