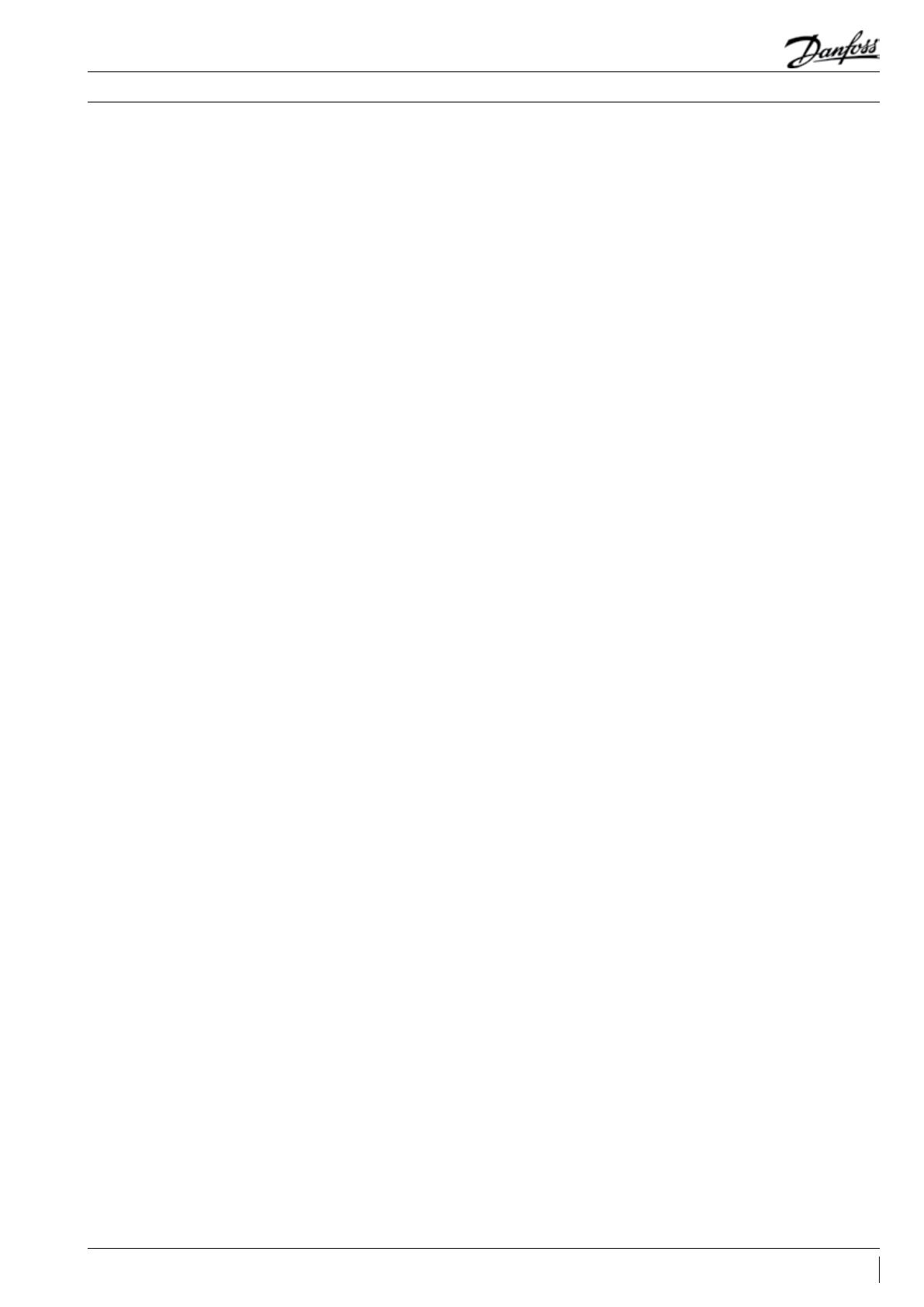
Content
3FRCC.PC.005.A7.02
Compressor model designation ............. 4
Nomenclature ............................................................4
General overview ..................................... 5
Benets ......................................................................... 5
Scope .............................................................................5
Design challenge ......................................................5
Oil management concepts ...................... 7
Static systems .............................................................7
Dynamic systems ......................................................7
Compressor parallel assembly
nomenclature ........................................... 8
Technical specications 50 Hz data ........ 9
Technical specications 60 Hz data ...... 10
Operating conditions ............................. 11
Motor supply ............................................................11
Compressor ambient temperature ..................11
Application envelope ............................................11
Discharge temperature protection .................13
High and low pressure protection ....................14
Cycle rate limit ..........................................................14
System design recommendations ........ 15
Essential piping design considerations ..........15
Expansion device ....................................................16
Refrigerant charge limits ......................................16
Sump heater..............................................................17
External check valve ..............................................17
Specic application recommendations 18
Required tests .........................................................18
Defrost cycle logic ..................................................18
Sound and vibration management ...... 19
Running sound level ..............................................19
Sound generation in a refrigeration or air
conditioning system ..............................................19
Tandem units S 170 to 425 (except
SM248-272-294) & S485 ......................... 21
Operation principle ................................................21
Ordering information ........................................... 22
Compressor mounting ......................................... 23
Oil equalisation connection ............................... 24
Restrictor assembly ............................................... 24
Tandem units SM248-272-294 ............... 25
Operation principle ............................................... 25
Ordering information ........................................... 25
Compressor mounting ......................................... 25
Oil equalisation connection ............................... 25
Suction washer ....................................................... 26
Tandem units SY/SZ482-540-600-620-
680-760 .................................................... 27
Operation principle ............................................... 27
Ordering information ........................................... 27
Compressor mounting ......................................... 27
Oil equalisation connection ............................... 28
Suction washer ....................................................... 28
Trio units SM/SZ444 - 483 ...................... 29
Operation principle ............................................... 29
Ordering information ........................................... 29
Compressor mounting ......................................... 29
Oil equalisation connection ............................... 30
Suction line ............................................................... 30
Trio units SM/SZ550 ............................... 31
Operation principle ................................................31
Ordering information ............................................31
Compressor mounting ......................................... 32
Oil equalisation connection ............................... 32
Restrictors assembly ............................................. 32
Trio units SY/SZ720 - 900 - 1140 ............ 33
Operation principle ............................................... 33
Ordering information ........................................... 33
Compressor mounting ......................................... 33
Oil equalisation connection ............................... 34
Suction line ............................................................... 34
Quadro units SM/SZ740 ......................... 35
Operation principle ............................................... 35
Ordering information ........................................... 35
Compressor mounting ........................................ 36
Oil equalisation connection ............................... 36
Restrictor assembly ............................................... 36
Installation & service ............................. 37
Compressor mounting ..........................................37
Tandem, trio & quadro piping design .............37
Wiring and rotation direction.............................37
Oil level ...................................................................... 38
Failure analysis ........................................................ 38
Oil equalisation connection ............................... 38
Accessories .............................................. 39
Application Guidelines