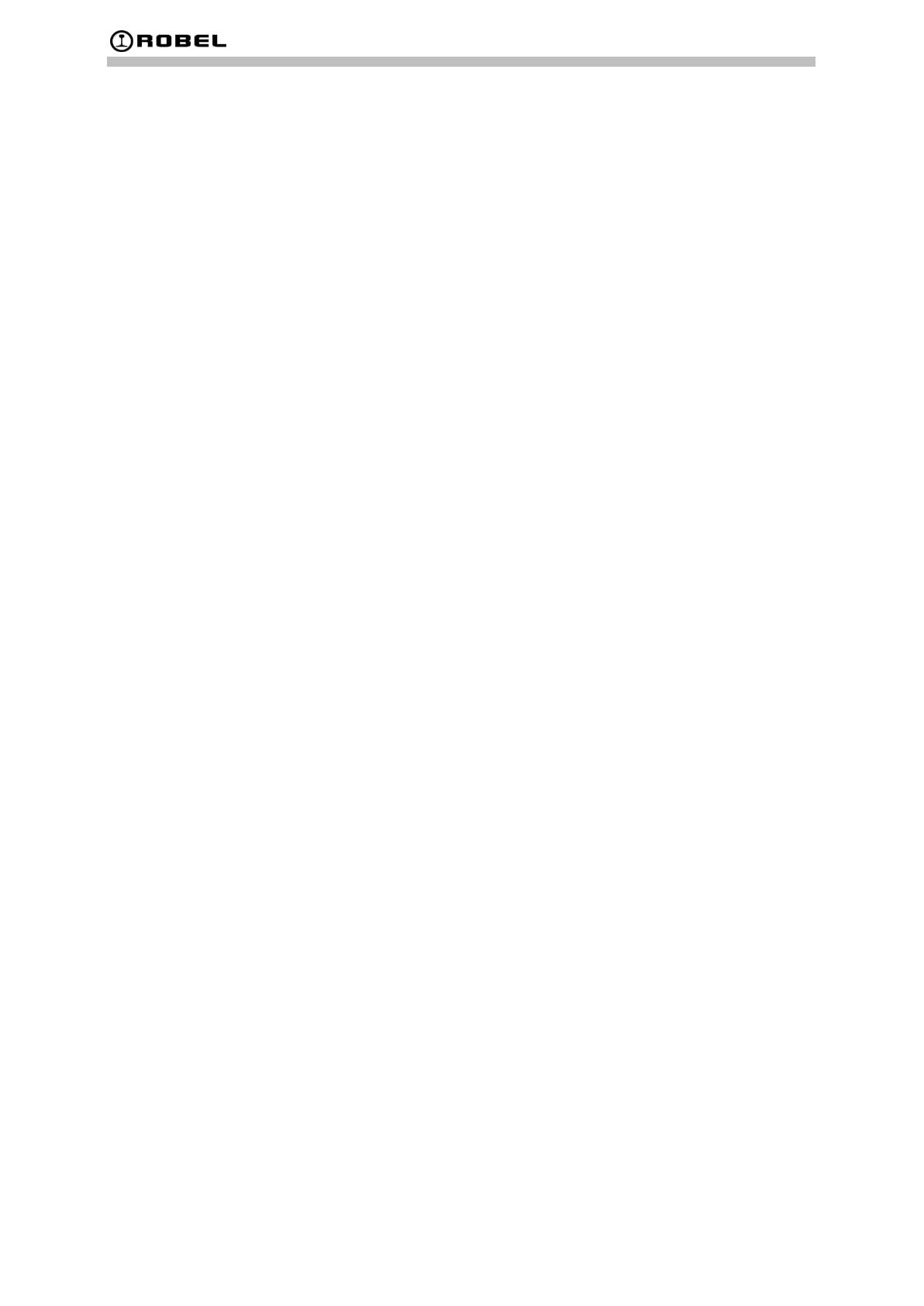
2. Safety
•
Personnel who can prove that they are qualified to use
this product either through training or experience,
• Personnel familiar with the safety concepts that relate
to machinery and equipment,
• Maintenance and service personnel who are specially trained
to repair machines, appliances and its accessories.
Only persons who can read and understand this manual are
allowed to use the product. They should sign to indicate that
they have read and understood the manual.
Replacement, maintenance and operation of the product
should only occur where official regulations are strictly fol-
lowed for its use and safety, especially where they relate to
safety and protection of the workplace and environment as
well as the operating, maintenance and safety regulations or
other instructions supplied by the manufacturer or supplier.
1.4 Liability Exclusions
The manufacturer declares himself to be exempt from any
responsibility for damage arising when the product is not
used in a designated way. This also includes use of the
machine without safety mechanisms.
Any use of the product other than that specified above is not
designated and endangers the lives and health of operating
and maintenance personnel as well as the material property of
the operator. The manufacturer of the product declares
himself free from liability for damage to people or property
belonging to the operator or a third party if:
• the product is not used as specified,
• operating and maintenance personnel have not read and
understood the aforementioned directions and have used
the product for other purposes,
•
operating or maintenance personnel are not
sufficiently qualified
•
the product has been used under conditions
exceeding limiting values,
• the product has not been serviced within the time
speci-fied,
• the product has not been serviced using other than
original spare parts,
•
product components or attachments have been
altered without authorisation.
These exclusions from liability for damage to people or
materi-al property do not affect other exclusions.
1.5 Copyright
Specific characteristics and particular attributes of the product
are the intellectual property of ROBEL Bahnbaumaschinen GmbH.
The copyright on its use remains with ROBEL Bahnbaumaschinen
GmbH. It may not be reproduced either in full or in part,
published or otherwise exploited for competitive purposes,
whether for payment or not. Its contents may not be
7