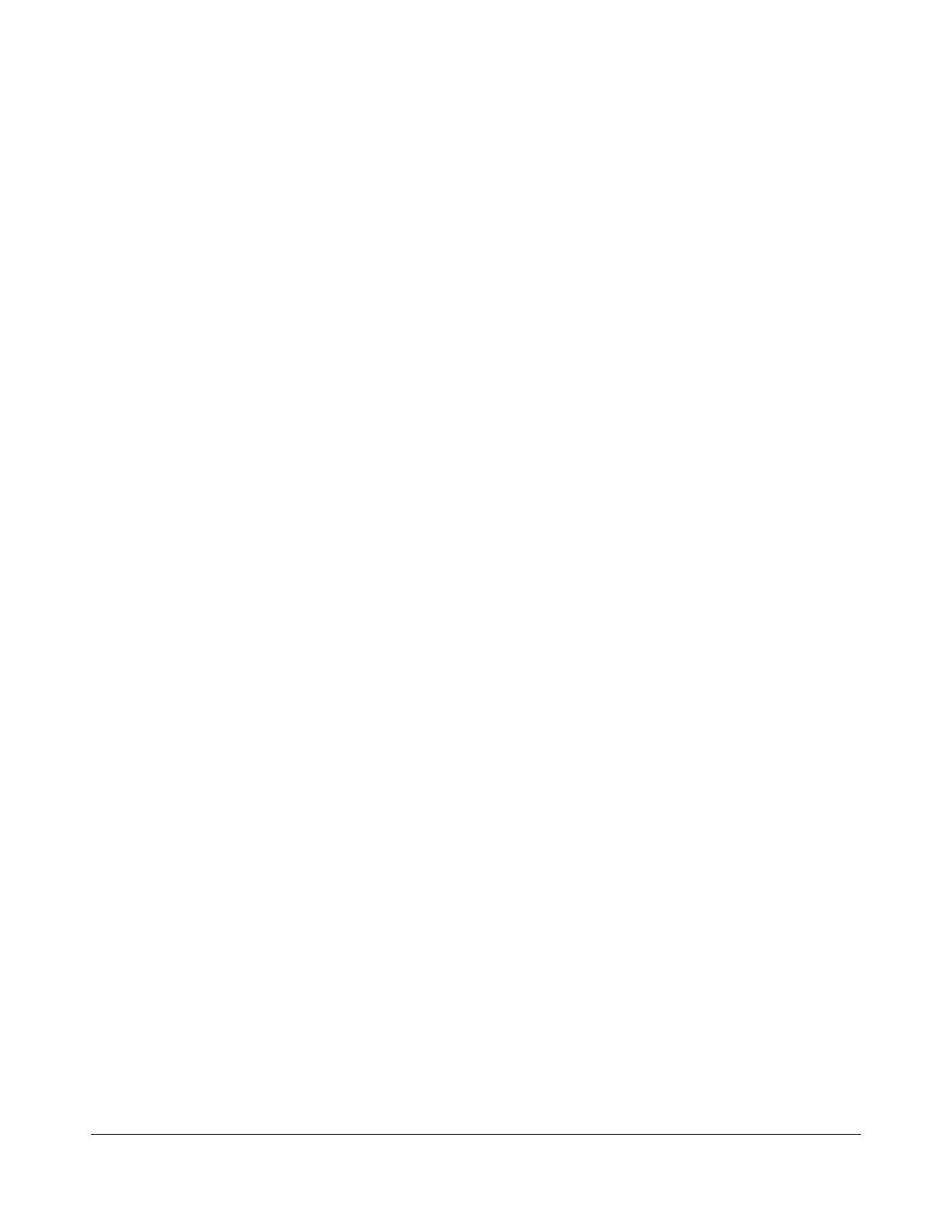
Table of Contents
Customer Service Information...................................................1
Returning Parts / Equipment to KVAL.......................................1
Returning Parts / Equipment to KVAL.......................................2
When you call: ................................................................................2
When sending merchandise back:..................................................2
Getting Started..........................................................................3
Safety First Danger! ..................................................................4
Responsibility.............................................................................5
PROCEDURE ...........................................................................5
LOCK OUT AND TAG OUT PROCEDURE ....................................7
LOCK RULES.................................................................................8
P-R-O-P-E-R ELECTRICAL LOCK-OUT..................................................8
P-R-O-P-E-R HYDRAULIC AND/OR PNEUMATIC LOCK-OUT..............9
P-R-O-P-E-R FLUIDS AND GASES LOCK-OUT...................................10
P-R-O-P-E-R MECHANICAL ENERGY LOCK-OUT..............................11
ZERO ENERGY START UP...................................................................12
Safety Guidelines..........................................................................13
Electrical................................................................................................13
Compressed Air:...................................................................................13
Operating Safety:..................................................................................13
Compliance with Codes and Regulations:.........................................13
Operators Training: ..............................................................................13
Other Hazard Control Action:..............................................................13
UNCRATING & ASSEMBLY OF HANDLER...........................14
SPECIFICATIONS..................................................................16
Option(s):......................................................................................16
Option A: Reverse Stack ........................................................................16
Option B: Reverse Feed Direction..........................................................16
Option D: Modifications to make the Handler a Stacker Rather than a
Feeder.....................................................................................................16
Option E: Variable Speed A.C. Drive......................................................16
Option H: Remote Switch for Manual Feed-Through .............................16
Option H1: Remote Foot Switch for Manual Call....................................16
Option I: Center Clamping for Multiple Width Stacks of Doors...............16
Option L: Ability to Feed Doors with Raised Molding .............................17
Option M: Ball Catch Drills......................................................................17
Option Q: Automatic Door Stack Loading and Pallet Eject ....................17