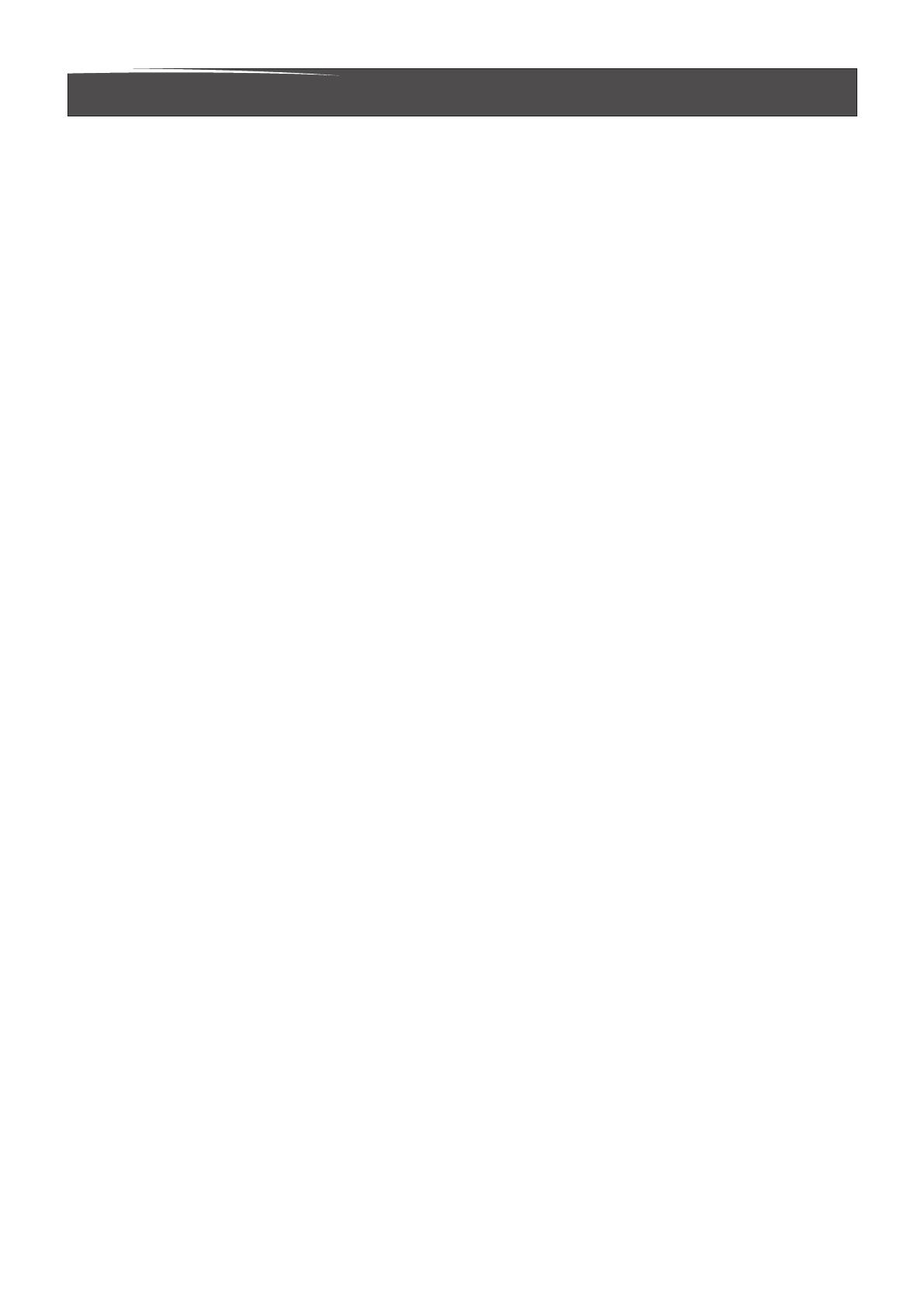
Installation & Servicing instructions ATAG XL
3
Content
1 Introduction .............................................................................................................................................4
2 Regulations ............................................................................................................................................7
3 Scope of delivery .................................................................................................................................... 9
4 Description ...........................................................................................................................................10
5 Installation and mounting ..................................................................................................................... 11
5.1 Wall-mounted in line ............................................................................................................................. 12
5.2 Free-standing in line .....................................................................................................................13
5.3 Free-standing back to back .......................................................................................................... 14
5.4 Connecting the boiler ...................................................................................................................15
6 Hydraulic and gas line system ..............................................................................................................16
6.1 Heating system ............................................................................................................................16
6.2 Expansion vessel .........................................................................................................................17
6.3 Water quality ................................................................................................................................17
6.4 Gas line ........................................................................................................................................19
6.5 Condensate drain ......................................................................................................................... 20
6.6 Hot water supply ..........................................................................................................................22
7 Flue gas system ...................................................................................................................................23
7.1 Parallel boiler connection .............................................................................................................24
7.2 Concentric boiler connection ........................................................................................................ 24
7.3 Connectingtheuegasoutlet/airsupplysystem ......................................................................... 25
7.4 Individualuegasoutlet ...............................................................................................................25
7.5 Collectiveuegasoutlet ..............................................................................................................28
7.6 Condensateventcollectiveuegassystem ................................................................................31
8 Electrical connections ...........................................................................................................................32
8.1 External controls ..........................................................................................................................34
8.2 Wiring diagram .............................................................................................................................36
9 Boiler control ........................................................................................................................................38
9.1 Operational status ........................................................................................................................39
9.2 Operation .....................................................................................................................................39
9.3 Commissioning .............................................................................................................................40
9.4 Filling heating system ...................................................................................................................43
10 Basic settings .......................................................................................................................................45
11 Parameters ........................................................................................................................................... 47
11.1 Activate factory settings ...............................................................................................................50
12 Put out of operation .............................................................................................................................50
13 Inspection and maintenance ................................................................................................................51
13.1 Maintenance intervals ..................................................................................................................51
13.2 Checks prior to commissioning ....................................................................................................51
13.2.1 Pollution check .................................................................................................................. 52
13.2.2 Control O
2
......................................................................................................................... 53
13.3 Maintenance activities .................................................................................................................. 54
13.4 Counter running hours .................................................................................................................57
13.5 Warranty ....................................................................................................................................... 57
14 Error report ...........................................................................................................................................58
AnnexATechnicalspecications ................................................................................................................ 59
Annex B System water additives ................................................................................................................60
Annex C Dimensions ..................................................................................................................................61
Annex D Resistance table sensors.............................................................................................................66
Annex E Declaration of conformity .............................................................................................................67
Annex Benchmark commissioning checklist and service record ............................................................. 68