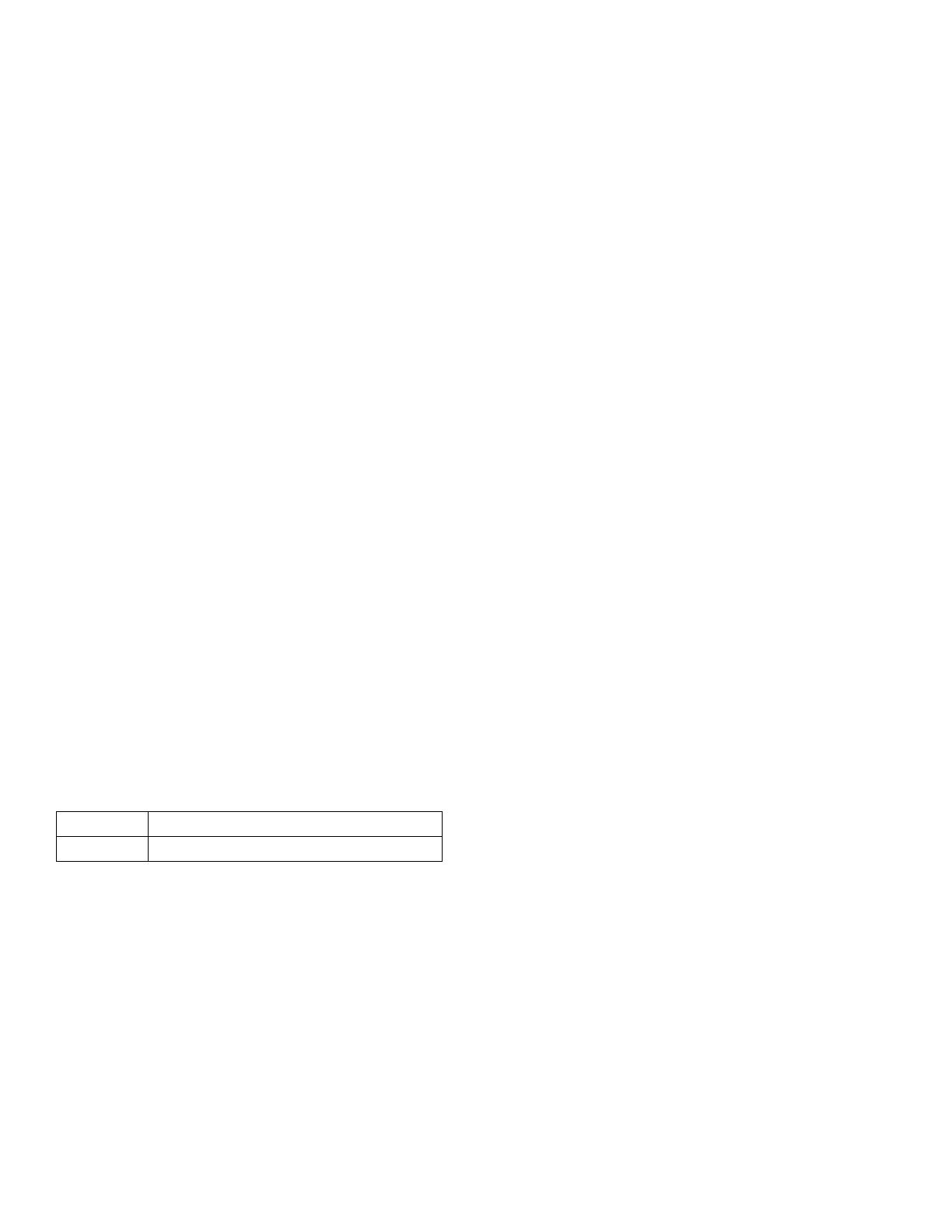
2334513C
Contents
Related Manuals . . . . . . . . . . . . . . . . . . . . . . . . . 2
Models and Approvals . . . . . . . . . . . . . . . . . . . . . . 3
Wolverine Basic . . . . . . . . . . . . . . . . . . . . . . . . . 3
Wolverine Advanced . . . . . . . . . . . . . . . . . . . . . . 3
Wolverine Hazardous Location . . . . . . . . . . . . . . 4
Key Points . . . . . . . . . . . . . . . . . . . . . . . . . . . . . . 5
Warnings . . . . . . . . . . . . . . . . . . . . . . . . . . . . . . . . . 7
Component Identification . . . . . . . . . . . . . . . . . . . . 9
Installation . . . . . . . . . . . . . . . . . . . . . . . . . . . . . . . 11
Grounding . . . . . . . . . . . . . . . . . . . . . . . . . . . . . 11
Accessories . . . . . . . . . . . . . . . . . . . . . . . . . . . . 11
Flush Before Using Equipment . . . . . . . . . . . . . 11
Typical Installation - Ordinary Locations . . . . . . 12
Typical Installation - Hazardous Locations . . . . 13
Choosing an Installation Location . . . . . . . . . . . 14
Fluid Connections . . . . . . . . . . . . . . . . . . . . . . . 14
Motor Electrical Connections . . . . . . . . . . . . . . 14
Second Pump Add-On . . . . . . . . . . . . . . . . . . . 17
Operation . . . . . . . . . . . . . . . . . . . . . . . . . . . . . . . . 18
Pressure Relief Procedure . . . . . . . . . . . . . . . . 18
Flush the Equipment . . . . . . . . . . . . . . . . . . . . . 18
Prime the Pump . . . . . . . . . . . . . . . . . . . . . . . . 18
Calibrate Chemical Dosage . . . . . . . . . . . . . . . 19
Preventive Maintenance Schedule . . . . . . . . . . 22
Tighten Threaded Connections . . . . . . . . . . . . . 22
Tighten Packings . . . . . . . . . . . . . . . . . . . . . . . 22
Storage . . . . . . . . . . . . . . . . . . . . . . . . . . . . . . . 22
Troubleshooting . . . . . . . . . . . . . . . . . . . . . . . . . . . 23
Repair . . . . . . . . . . . . . . . . . . . . . . . . . . . . . . . . . . . 24
Wolverine Basic Pump Repair . . . . . . . . . . . . . . 24
Wolverine Advanced and Hazardous Location
Pump Repair . . . . . . . . . . . . . . . . . . . . . . . . 29
DC Motor Brush Repair (not for Hazardous
Location) . . . . . . . . . . . . . . . . . . . . . . . . . . . 33
Check Valve Repair . . . . . . . . . . . . . . . . . . . . . . 34
Parts . . . . . . . . . . . . . . . . . . . . . . . . . . . . . . . . . . . . 35
Wolverine Basic Pump . . . . . . . . . . . . . . . . . . . 35
Wolverine Advanced Pump . . . . . . . . . . . . . . . . 38
Wolverine Hazardous Location Pump . . . . . . . . 41
Kits and Accessories . . . . . . . . . . . . . . . . . . . . . . . 46
Wolverine (All) . . . . . . . . . . . . . . . . . . . . . . . . . . 46
Wolverine Advanced and Hazardous Location . 46
Dimensions . . . . . . . . . . . . . . . . . . . . . . . . . . . . . . . 47
Wolverine Basic Dimensions . . . . . . . . . . . . . . . 47
Wolverine Advanced Dimensions . . . . . . . . . . . 48
Wolverine Hazardous Location Dimensions . . . 49
Performance Charts . . . . . . . . . . . . . . . . . . . . . 50
Technical Data . . . . . . . . . . . . . . . . . . . . . . . . . . . . 57
Graco Standard Warranty . . . . . . . . . . . . . . . . . . . 58
Related Manuals
Manual No. Description
334993 Harrier Chemical Injection Controller