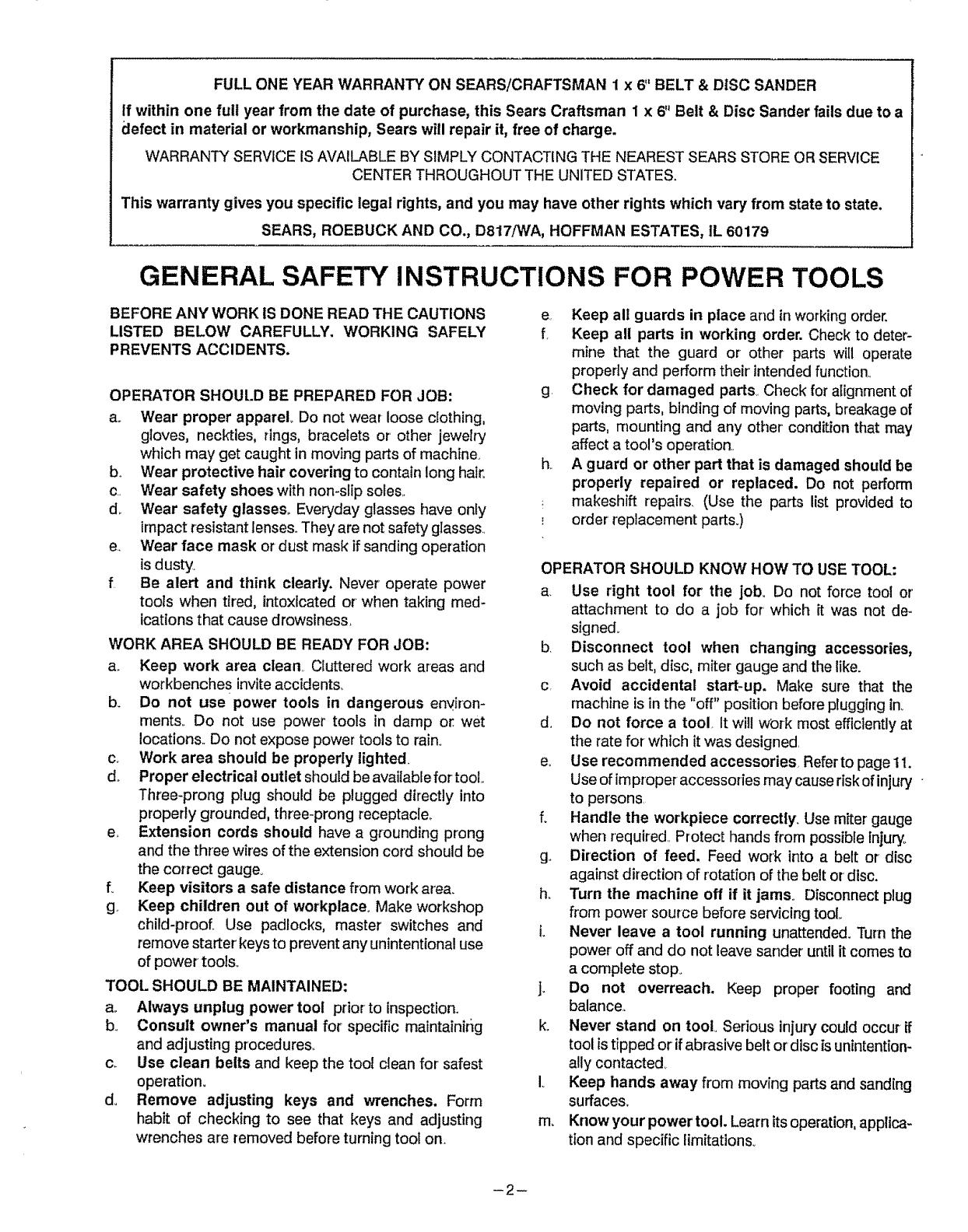
FULL ONE YEAR WARRANTY ON SEARS/CRAFTSMAN 1 x 6" BELT &DISC SANDER
if within one full year from tile date of purchase, this Sears Craftsman 1x 6" Belt & Disc Sander fails due to a
defect in material or workmanship, Sears will repair it, free of charge.
WARRANTY SERVICE iS AVAILABLE BY SIMPLY CONTACTING THE NEAREST SEARS STORE ORSERVICE
CENTER THROUGHOUT THE UNITED STATES.
This warranty gives you specific legal rights, and you may have other rights whictl vary from state to state,
SEARS, ROEBUCK AND CO., D817/WA, HOFFMAN ESTATES, IL 60179
GENERAL SAFETY INSTRUCTIONS FOR POWER TOOLS
BEFORE ANY WORK IS DONE READ THE CAUTIONS
LISTED BELOW CAREFULLY, WORKING SAFELY
PREVENTS ACCIDENTS,
OPERATOR SHOULD BE PREPARED FOR JOB:
a+ Wear proper apparel+ Do not wear loose clothing,
gloves, neckties, rings, bracelets or other jewelry
which may get caught in moving parts of machine
b. Wear protective hair covering to contain long hair.
cWear safety shoeswith non-slip soles+
d.. Wear safety glasses+ Everyday glasses have only
impact resistant lenses+They are not safety glasses
e. Wear face mask or dust mask ifsanding operation
isdusty+
f Be alert and think clearly. Never operate power
tools when tired, intoxicated or when taking med-
ications that cause drowsiness.
WORK AREA SHOULD BE READY FOR JOB:
a+ Keep work area clean+ Cluttered work areas and
workbenches invite accidents,,
b+ Do not use power tools in dangerous environ-
merits+ Do not use power' tools in damp or. wet
locations. Do not expose power tools to rain.
c+ Work area should be properly lighted.
d+ Proper electrical outlet should beavailablefortooL
Three-prong plug should be plugged directly into
properly grounded, three-prong receptacle+
e+ Extension cords should have a grounding prong
and the three wires of the extension cord should be
the correct gauge+
f+ Keep visitors a safe distance from work area+
g+ Keep children out of workplace+ Make workshop
child-proof. Use padlocks, master' switches and
remove starter' keys to prevent any unintentional use
of power tools,
TOOL SHOULD BE MAINTAINED:
a+ Always unplug power tool prior,to inspection.
b+ Consult owner's manual for specific maintainirlg
and adjusting pr.ocedureso
c+ Use clean belts and keep the tool clean for safest
operation+
d. Remove adjusting keys and wrenches. Form
habit of checking to see that keys and adjusting
wrenches are removed before turning tool on.
e+ Keep all guards in place and in workingorder.
f+ Keep all parts in working order. Check to deter-
mine that the guard or other parts will operate
propedy and perform their' intendedfunction+
g Check for damaged parts+ Check for atignment of
moving parts, binding of moving parts, breakage of
parts, mounting and any other condition that may
affect a tool's operation
h+ A guard or other part that is damaged should be
properly repaired or replaced. Do not perform
makeshift repairs_ (Use the parts list provided to
+ order replacement parts+)
OPERATOR SHOULD KNOW HOW TO USE TOOL:
a+ Use right tool for the job. Do not force tool or'
attachment to do a job for which it was not de+
signed.
b. Disconnect tool when changing accessories,
such as belt, disc, miter gauge and the like.
c Avoid accidental start-up. Make sure that the
machine is in the "off" position before plugging in+
d° Do not force atool It will work most efficiently at
the rate for which it was designed
e+ Use recommended accessories, Referto page 11.
Use of improper accessories may cause risk of injury
to persons
f+ Handle the workpiece correctly. Use m_tergauge
when required, Protect hands from possibleinjury+
g+ Direction of feed. Feed work into a belt or disc
against direction of rotation of the belt or+disc.
h+ Turn the machine off if it jams. Disconnect plug
from power' source before servicing tool.,
LNever leave a tool running unattended+ Turn the
power off and do not leave sander until it comes to
a complete stop+
j+ Do not overreach. Keep proper footing and
balance,
k+ Never stand on tool Serious injury could occur if
tool is tipped or'if abrasive belt or disc isunintention-
ally contacted+
I+ Keep hands away from moving parts and sanding
surfaces+
m+ Know your power tool. Learn itsoperation, applica-
tion and specific limitations+
-2-