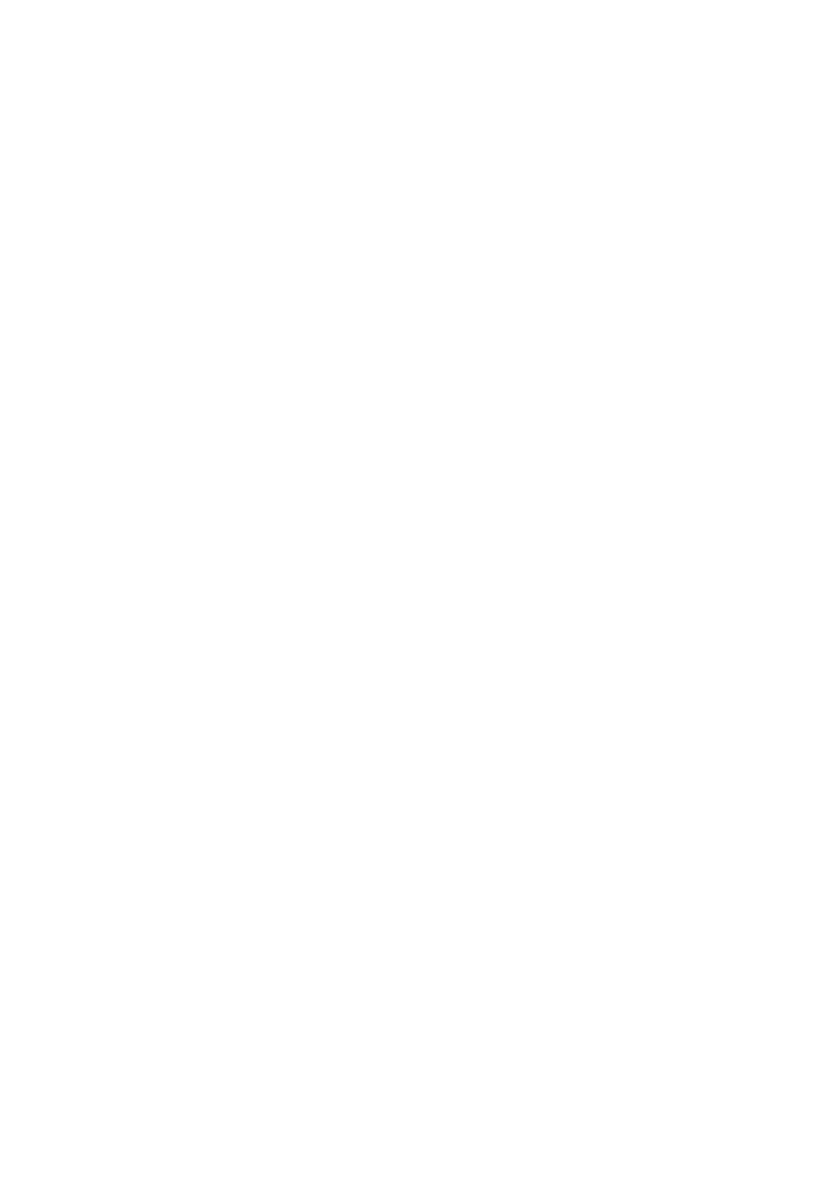
4Table of Contents
V 2.1S user manual V6860, version 3.2
Connecting the Device to the Computer . . . . . . . . . . . . . . . . . . . . . . . . 23
Configuring the LAN Settings . . . . . . . . . . . . . . . . . . . . . . . . . . . . . . 23
Connecting the Cables . . . . . . . . . . . . . . . . . . . . . . . . . . . . . . . . . . . . 24
Configuring the Router . . . . . . . . . . . . . . . . . . . . . . . . . . . . . . . . . . . 24
Integrating the LAN into a Company Network . . . . . . . . . . . . . . . . . . 25
Controlling Several Systems Separately in a LAN . . . . . . . . . . . . . . . . 25
Connecting the Remote Connector . . . . . . . . . . . . . . . . . . . . . . . . . . . . . 25
GROUND . . . . . . . . . . . . . . . . . . . . . . . . . . . . . . . . . . . . . . . . . . . . . . . 26
HOME . . . . . . . . . . . . . . . . . . . . . . . . . . . . . . . . . . . . . . . . . . . . . . . . . . 26
BIN 0 - 3 . . . . . . . . . . . . . . . . . . . . . . . . . . . . . . . . . . . . . . . . . . . . . . 27
Binary Code . . . . . . . . . . . . . . . . . . . . . . . . . . . . . . . . . . . . . . . . . . . . 27
Ground . . . . . . . . . . . . . . . . . . . . . . . . . . . . . . . . . . . . . . . . . . . . . . . . . . 28
Operation . . . . . . . . . . . . . . . . . . . . . . . . . . . . . . . . . . . . . . . . . . . . . . . . . . 28
Operating with the Keypad . . . . . . . . . . . . . . . . . . . . . . . . . . . . . . . . . . . 28
Operation with Chromatography Software . . . . . . . . . . . . . . . . . . . . . . . 29
Switch On and Self Test . . . . . . . . . . . . . . . . . . . . . . . . . . . . . . . . . . . . . 29
Setting the Valve Position . . . . . . . . . . . . . . . . . . . . . . . . . . . . . . . . . . . . 30
Injecting the Sample . . . . . . . . . . . . . . . . . . . . . . . . . . . . . . . . . . . . . . . . 30
Application Examples . . . . . . . . . . . . . . . . . . . . . . . . . . . . . . . . . . . . . . . . . 31
Valve Positions . . . . . . . . . . . . . . . . . . . . . . . . . . . . . . . . . . . . . . . . . . . . 31
Valve Position Load (L) . . . . . . . . . . . . . . . . . . . . . . . . . . . . . . . . . . . . . 31
Valve Position Inject (I) . . . . . . . . . . . . . . . . . . . . . . . . . . . . . . . . . . . . . 32
Selecting the Column . . . . . . . . . . . . . . . . . . . . . . . . . . . . . . . . . . . . . . . 33
Backflushing the Column . . . . . . . . . . . . . . . . . . . . . . . . . . . . . . . . . . . . 34
Backflushing the Precolumn . . . . . . . . . . . . . . . . . . . . . . . . . . . . . . . . . . 34
Functional Tests IQ and OQ . . . . . . . . . . . . . . . . . . . . . . . . . . . . . . . . . . . . 36
Troubleshooting . . . . . . . . . . . . . . . . . . . . . . . . . . . . . . . . . . . . . . . . . . . . . 37
LAN . . . . . . . . . . . . . . . . . . . . . . . . . . . . . . . . . . . . . . . . . . . . . . . . . . . . 37
Error Messages . . . . . . . . . . . . . . . . . . . . . . . . . . . . . . . . . . . . . . . . . . . . 37
Maintenance and Care . . . . . . . . . . . . . . . . . . . . . . . . . . . . . . . . . . . . . . . . 38
Cleaning and Caring for the Device . . . . . . . . . . . . . . . . . . . . . . . . . . . . 38
Valve Assembly . . . . . . . . . . . . . . . . . . . . . . . . . . . . . . . . . . . . . . . . . . . . 38
Disassembling the Valve . . . . . . . . . . . . . . . . . . . . . . . . . . . . . . . . . . . . . 39
Orientating the Rotor Seal in the Valve . . . . . . . . . . . . . . . . . . . . . . . . . . 41