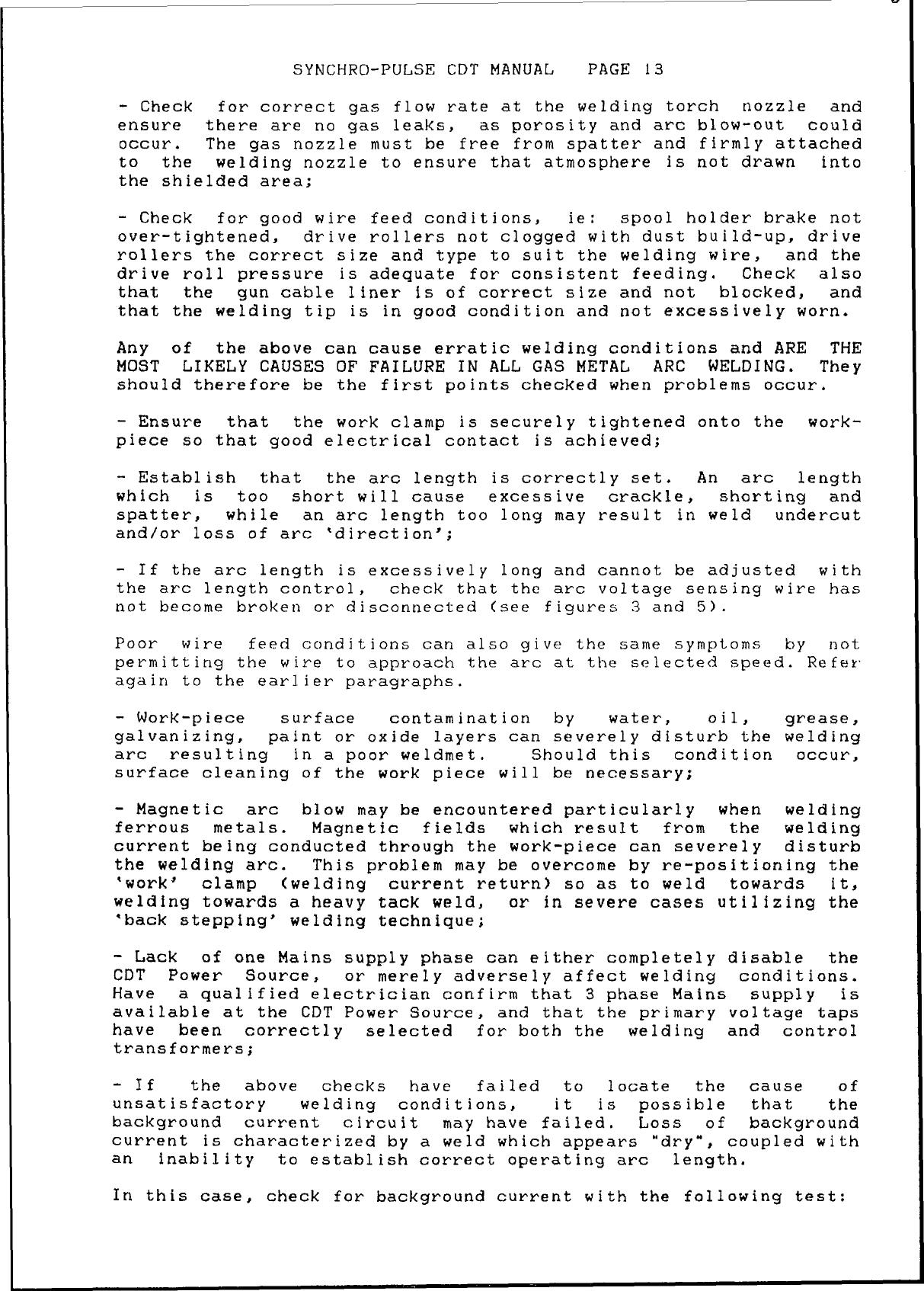
SYNCHRO-PULSE
CDT
MANUAL
PAGE
13
-
Check for correct gas
flow
rate at the welding torch nozzle and
ensure there
are
no gas leaks,
as
porosity
and
arc
blow-out could
occur.
The
gas nozzle must be free from spatter and firmly attached
to the welding nozzle to ensure that atmosphere is not drawn into
the shielded area;
-
Check
for
good wire feed conditions, ie:
spool
holder brake
not
over-tightened, drive
rollers
not clogged with dust build-up, drive
rollers
the correct size and type to
suit
the welding wire, and the
drive
roll
pressure
is
adequate for consistent feeding. Check
also
that the gun
cable
liner
is
of
correct size and not blocked, and
that the welding tip
is
in
good condition and not excessively worn.
Any
of
the above can cause erratic welding conditions and
ARE
THE
MOST
LIKELY
CAUSES
OF
FAILURE
IN
ALL
GAS
METAL
ARC
WELDING.
They
should therefore be the
first
points checked when problems occur.
-
Ensure
that
the
work clamp
is
securely tightened onto the work-
piece
so
that good electrical contact
is
achieved;
-
Establish that the arc length is correctly set. An arc length
which is too short will
cause
excessive crackle, shorting
and
spatter, while an arc length too long may
result
in weld undercut
and/or
loss
of
arc 'direction';
-
If
the
arc length
is
excessively long and cannot
be
adjusted with
the arc length control,
check
that
the arc voltage
sensing wire
has
not become broken
or
disconnected (see figures
3
and
5).
Poor
wire
feed conditions can also
give
the same symptoms by
not
permitting
the
wire
to
approach
the
arc
at;
the selected speed.
Refar,
again
to
the earlier paragraphs.
-
Work-piece surface contamination
by
water, oil, grease,
galvanizing, paint
or
oxide layers can severely disturb the welding
arc
resulting
in
a
poor weldmet. Should this condition
occur,
surface cleaning
of
the work piece
will
be
necessary;
-
Magnetic arc blow may be encountered particularly when welding
ferrous metals. Magnetic fields which
result
from
the
welding
current being conducted through the work-piece can severely disturb
the welding arc.
This
problem
may
be
overcome by
re-positioning
the
'work'
clamp (welding current return)
so
as to weld towards
it,
welding
towards
a
heavy
tack
weld,
or
in
severe
cases
utilizing
the
'back
stepping' welding technique;
-
Lack
of
one
Mains supply phase can either completely
disable
the
CDT Power Source,
or
merely adversely affect welding conditions.
Have
a
qualified electrician
confirm
that
3
phase
Mains supply
is
available
at
the CDT Power Source, and that the primary voltage
taps
have been correctly selected
for
both the welding and control
transformers;
-
If
the above checks have failed
to
locate the cause
of
unsatisfactory welding conditions,
it
is possible that the
background current circuit
may
have failed.
Loss
of background
current is characterized by
a
weld which appears "dry", coupled with
an inability
to
establish correct operating arc
length.
In
this case, check for background current
with
the following test: