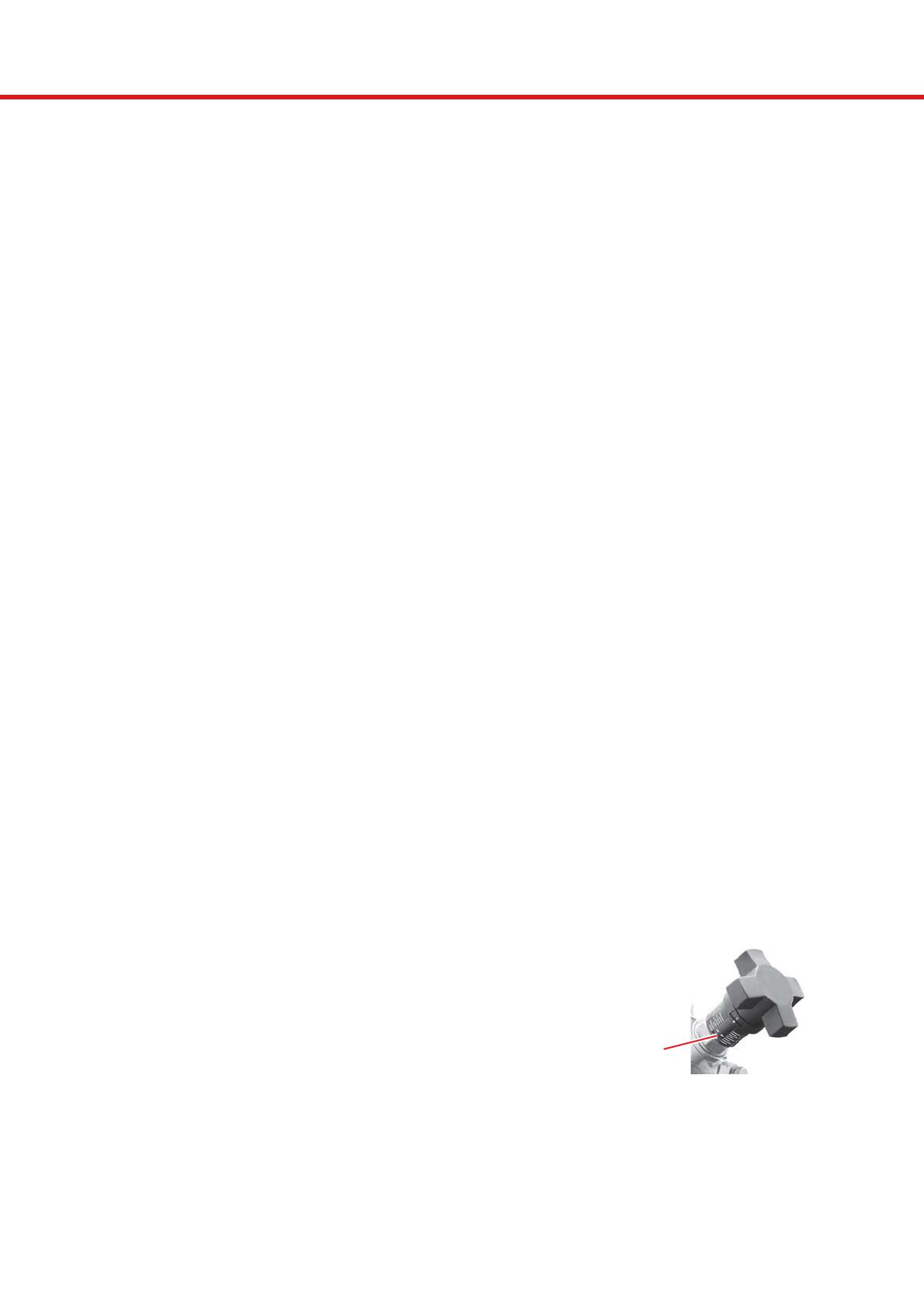
20
step 12 If a makeup module is installed, the operating mode must be selected.MCF
The operating mode is depending on several criteria such as size of the system,
age of the system, possible known leakage and so on.
If there are known and regular leakages (e.g. a known makeup amount within a
known period) we recommend to use the operating mode ”time-controlled”.
For a description of the different operating modes see instruction manual
multicontrol , -_1, chapter 5.7 - “user level 3”.MCK MCM
step 13 If a degassing module is installed, the operating mode ”degassing module”MAE
must be selected. If the selection happened incorrectly, degassing can‘t work
correctly!
:Adjustment of the degassing module
- Shut off the regulating valve and the ball valve at the degassing module.
- Go to manual mode (user level 3) see instruction manual ,( multicontrol MCK
-_1 chapter 5.7 “user level 3”) and switch on the output ”degassing valve”MCM ,
(”output: on”)
- Wait until the motor valve opened completely (ca. 35 sec.; the scale resp., the
red axis at the electric actuator must not rotate anymore).
- Open the ball valve at the intake side.
- Open the regulating valve slowly until you hear a flow (ca. 1/4 turn). The plant
pressure decreases, the pressure maintenance pump starts.
- Look for the plant pressure shown at the display.
- The regulating valve is set correctly, if pump 1 is able to increase the plant
pressure and stops. If the pump can‘t increase the plant pressure resp. the
second pump (systems Duo, Maxi) starts, the regulating valve is set incorrectly
(opened too much).
- After this, the output ”degassing valve” must be set to ”Auto” again.
- (1)The setting of the regulating valve must be notated
at the plant- resp. commissioning record.
: _________setting regulating valve MAE (1)
step 14 The device is now ready for operation.
All shut off devices from/to system return must be secured against unintended
closing (e.g. by dismantling the handle,...)
Further settings (e.g. water treatment, operating modes etc.) must be done in
menu ”settings” (see instruction manual , -_1).MCK MCM
5. Commissioning