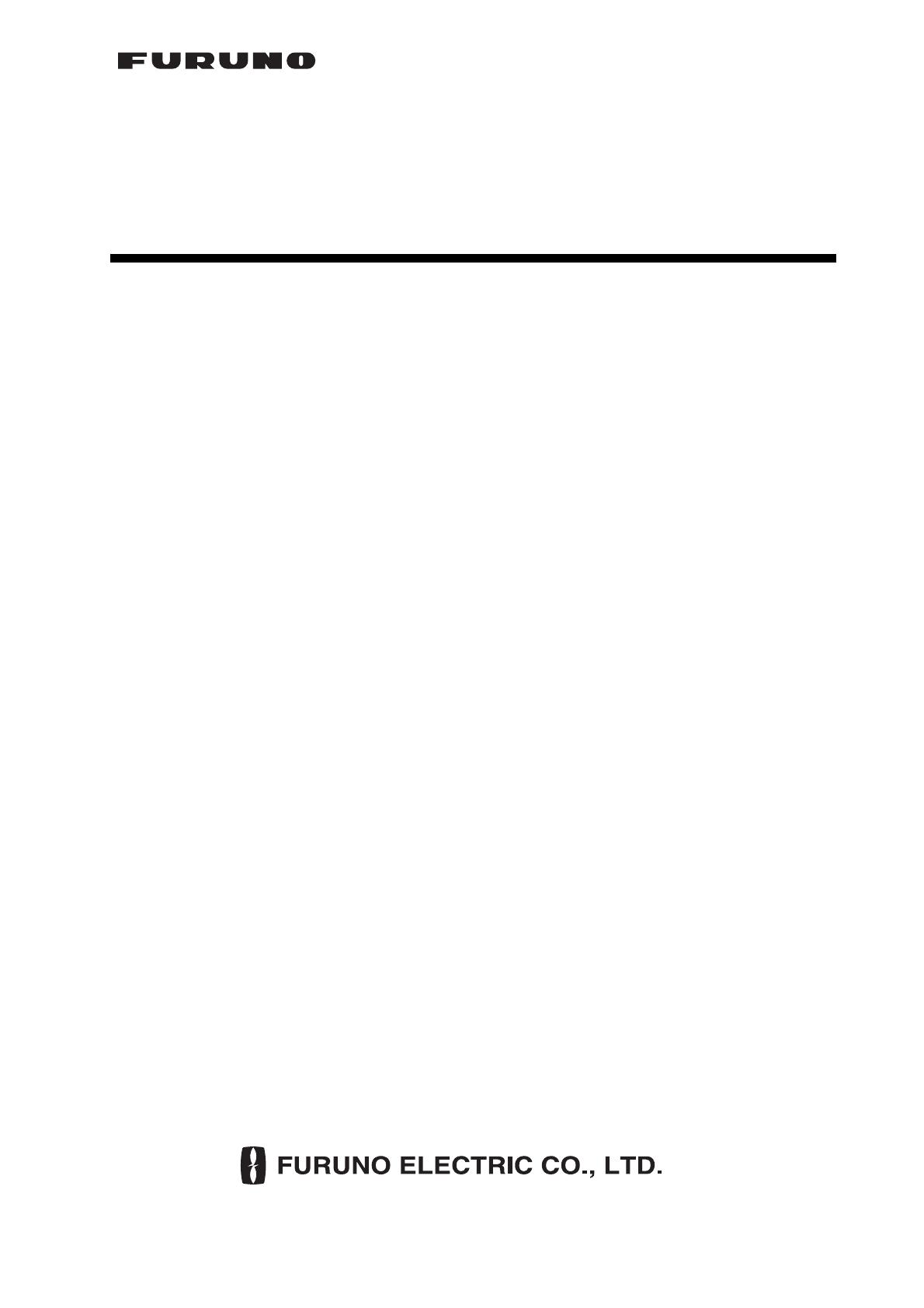
www.furuno.com
All brand and product names are trademarks, registered trademarks or service marks of their respective holders.
Installation Manual
DOPPLER SONAR
CURRENT INDICATOR
CI-68
SAFETY INSTRUCTIONS .............................................................................................................i
SYSTEM CONFIGURATIONS.....................................................................................................iii
EQUIPMENT LISTS.....................................................................................................................iv
1. INSTALLATION OVERVIEW................................................................................................1-1
1.1 Selection of Installation Site for Transducer....................................................................1-1
1.2 Ground ............................................................................................................................1-3
1.3 Changing Power Supply Voltage ....................................................................................1-5
2. MOUNTING ...........................................................................................................................2-1
2.1 Monitor Unit/Control Unit.................................................................................................2-1
2.2 Transceiver Unit ..............................................................................................................2-7
2.3 Junction Box (option) ......................................................................................................2-8
2.4 Transducer (Hull Unit) .....................................................................................................2-8
2.5 DC/AC Inverter..............................................................................................................2-12
3. WIRING .................................................................................................................................3-1
3.1 Wiring the Control Unit ....................................................................................................3-1
3.2 Wiring the Transceiver Unit.............................................................................................3-2
3.3 Connecting the Junction Box ..........................................................................................3-4
3.4 External Equipment.........................................................................................................3-6
3.5 DC/AC Inverter................................................................................................................3-8
4. ADJUSTMENTS....................................................................................................................4-1
4.1 [INSTALLATION] menu...................................................................................................4-1
4.2 Input/Output Data............................................................................................................4-8
4.3 External Noise and Interference Check ..........................................................................4-9
4.4 Setting Output Data.......................................................................................................4-12
4.5 DIP Switch Setting ........................................................................................................4-13
4.6 Sea Trial Check.............................................................................................................4-14
PACKING LIST ......................................................................................................................... A-1
OUTLINE DRAWINGS.............................................................................................................. D-1
INTERCONNECTION DIAGRAM ............................................................................................. S-1