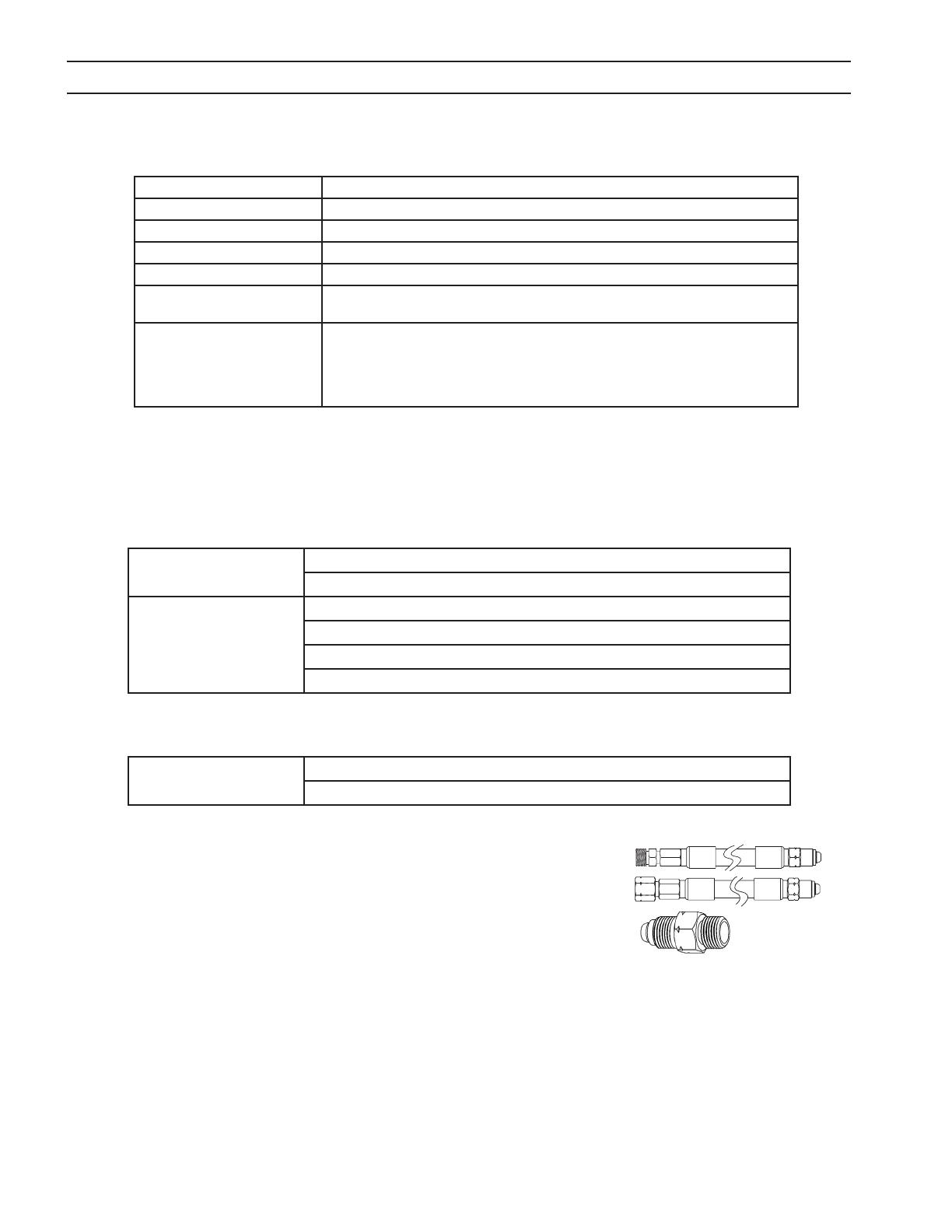
120
SECTION 2 DESCRIPTION
2.4 Plasma Gas Box Water Supply Requirements
Cooling Water ......................................................................................175 PSI (12,1 bar), 1.5 gallons per minute (5.68 liters/minute)
2.5 Plasma Gas Box Electrical Input Requirements
Voltage Supply +24 VDC for proportional valves, mfc
+15 VDC for pressure switch
Voltage Signals 24 VAC input to start gas solenoid valve
120 VAC input to arc starter
0-10 VDC input to proportional valves
0-10 VDC for mass ow valve
2.6 Shield Gas Box Electrical Input Requirements
Voltage Supply +24 VDC for 120/230 transformer and I/O board
+24 VDC for proportional valves and mfc’s
2.7 System Accessories
Adapter Coolant EPP-200 ..............................................................................................0558006162
Coolant Hose Adaptor Kit ............................................................................................ 0558006698
2.3 System Gas Requirements
Argon 125 PSI (8,6 bar) with 0.25” NPT, 99.995% purity, Filtered to 25 microns
Nitrogen 125 PSI (8,6 bar) with 0.25” NPT, 99.99% purity, Filtered to 25 microns
Oxygen 125 PSI (8,6 bar) with 0.25” NPT, 99.5% purity, Filtered to 25 microns
H-35 (Argon/Hydrogen) 75 PSI (5,2 bar), Speciality Gas, 99.995% purity, Filtered to 25 microns
Methane 75 PSI (5,2 bar) with 0.25” NPT, 93% purity, Filtered to 25 microns
Compressed Air
(Air Curtain )
80 PSI (5,5 bar) with 0.25” NPT, clean, dry, oil-free and ltered to 25 microns
Compressed Air
(Process)
80 PSI @ 1200cfh (5,5 bar @ 35 m
3
h) ltered to 25 microns
DIN Quality ISO 8573-1
Oil quality mg/m3 = 0.1 class 2
Particle Size 0.1um class 1
Temparature +3 C class 4