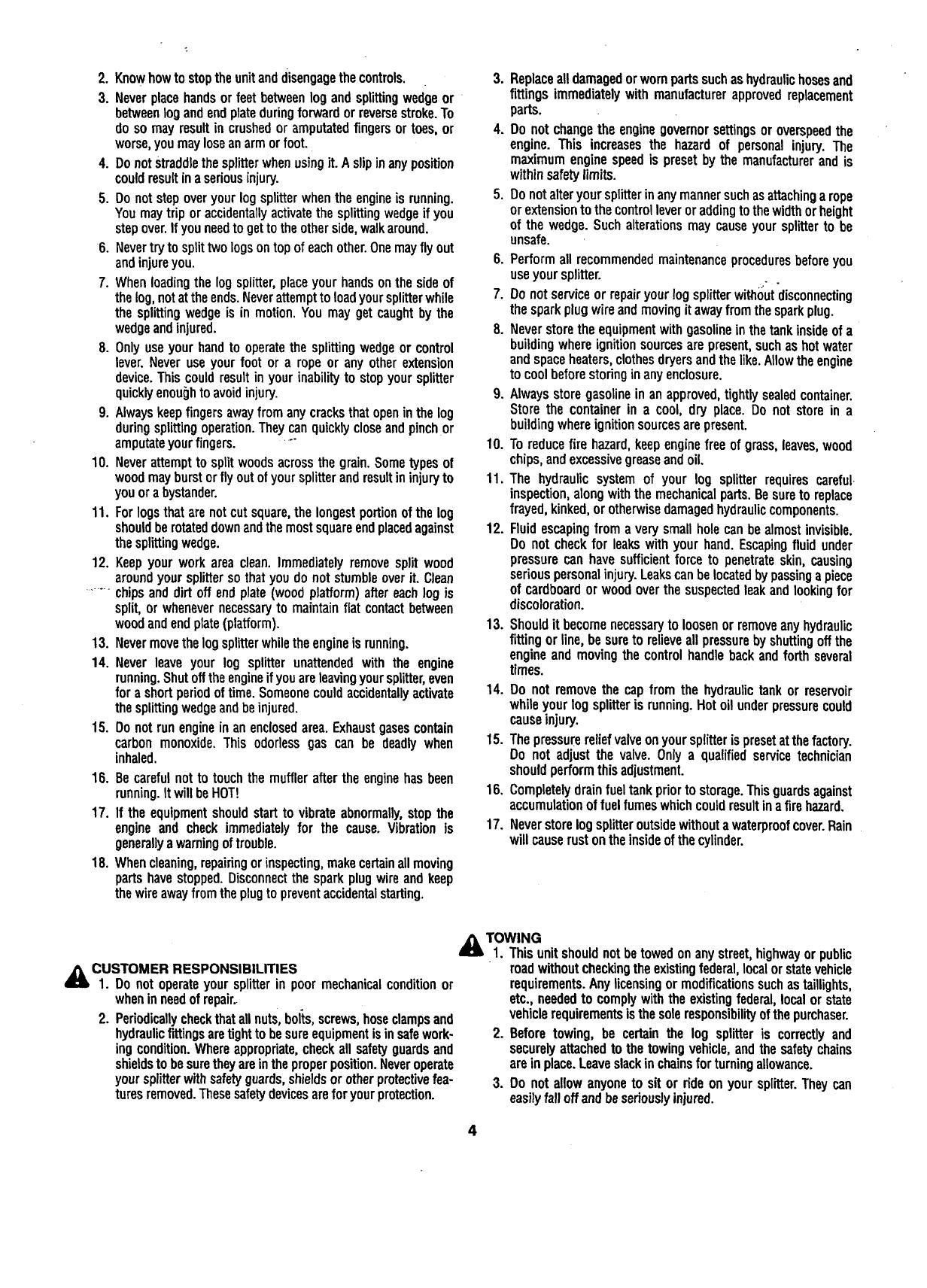
2. Knowhowtostoptheunitanddisengagethecontrols.
3. Neverplacehandsorfeetbetweenlogandsplittingwedgeor
betweenlogandendplateduringforwardorreversestroke.To
do somay resultincrushedor amputatedfingersor toes,or
worse,youmayloseanarmorfoot.
4. DonotStraddlethesplitterwhenusingit.Aslipinanyposition
couldresultinaseriousinjury.
5. Donotstepoveryourlogsplitterwhentheengineisrunning.
Youmaytriporaccidentallyactivatethesplittingwedgeifyou
stepover.Ifyouneedtogettotheotherside,walkaround.
6. Nevertrytosplittwologsontopofeachother.Onemayflyout
andinjureyou.
7. Whenloadingthelogsplitter,placeyourhandsonthesideof
thelog,notattheends.Neverattempttoloadyoursplitterwhile
thesplittingwedgeisin motion.Youmaygetcaughtbythe
wedgeandinjured.
8. Onlyuseyourhandtooperatethesplittingwedgeor control
lever.Neveruseyourfoot or a ropeor anyotherextension
device.Thiscouldresultin yourinabilityto stopyoursplitter
quicklyenou_ihtoavoidinjury.
9. Alwayskeepfingersawayfrom anycracksthatopeninthelog
duringsplittingoperation.Theycanquicklycloseandpinchor
amputateyourfingers. -
10. Neverattempttosplitwoodsacrossthegrain.Sometypesof
woodmayburstor flyoutofyoursplitterandresultininjuryto
youora bystander.
11. Forlogsthatarenotcutsquare,thelongestportionofthelog
shouldberotateddownandthemostsquareendplacedagainst
thesplittingwedge.
12. Keepyourworkareaclean.Immediatelyremovesplitwood
aroundyoursplittersothatyoudonotstumbleoverit. Clean
.......chipsanddirtoffendplate(woodplatform)aftereachlogis
split,orwhenevernecessaryto maintainflat contactbetween
woodandendplate(platform).
13. Nevermovethelogsplitterwhiletheengineisrunning.
14. Neverleaveyour log splitterunattendedwith the engine
running.Shutofftheengineifyouareleavingyoursplitter,even
fora shortperiodoftime.Someonecouldaccidentallyactivate
thesplittingwedgeandbeinjured.
15. Donotrunengineinanenclosedarea.Exhaustgasescontain
carbonmonoxide.Thisodorlessgas can be deadlywhen
inhaled.
16. Becarefulnottotouchthemuffleraftertheenginehasbeen
running.ItwillbeHOT!
17. Ifthe equipmentshouldstartto vibrateabnormally,stopthe
engineand checkimmediatelyfor the cause.Vibrationis
generallyawarningoftrouble.
18. Whencleaning,repairingorinspecting,makecertainallmoving
partshavestopped.Disconnectthesparkplugwireandkeep
thewireawayfromtheplugtopreventaccidentalstarting.
3. Replacealldamagedorwornpartssuchashydraulichosesand
fittingsimmediatelywithmanufacturerapprovedreplacement
parts.
4. Donotchangetheenginegovernorsettingsor overspeedthe
engine.This increasesthe hazardof personalinjury.The
maximumenginespeedispresetbythemanufacturerandis
withinsafetylimits.
5. Donotalteryoursplitterinanymannersuchasattachingarope
orextensiontothecontrolleveroraddingtothewidthorheight
of thewedge.Suchalterationsmay causeyoursplitterto be
unsafe.
6. Performall recommendedmaintenanceproceduresbeforeyou
useyoursplitter.
7. Donotserviceor repairyourlog splitterwithoutdisconnecting
thesparkplugwireandmovingit awayfromthesparkplug.
8. Neverstoretheequipmentwithgasolineinthetankinsideofa
buildingwhereignitionsourcesarepresent,suchashotwater
andspaceheaters,clothesdryersandthelike.Allowtheengine
to coolbeforestoringinanyenclosure.
9. Alwaysstoregasolinein anapproved,tightly sealedcontainer.
Store the containerin a cool,dry place.Do not store in a
buildingwhereignitionsourcesarepresent.
10. Toreducefire hazard,keepenginefree ofgrass,leaves,wood
chips,andexcessivegreaseandoil.
11. The hydraulic system of your log splitter requirescareful-
inspection,alongwiththemechanicalparts.Besureto replace
frayed,kinked,or otherwisedamagedhydrauliccomponents.
12. Fluidescapingfrom a very smallholecanbealmostinvisible.
Do not checkfor leakswith your hand.Escapingfluid under
pressurecanhavesufficientforceto penetrateskin,causing
seriouspersonalinjury.Leakscanbelocatedbypassingapiece
of cardboardor woodoverthe suspectedleakandlookingfor
discoloration.
13.
Shouldit becomenecessarytoloosenor removeanyhydraulic
fitting orline,besureto relieveallpressurebyshuttingoffthe
engineandmovingthecontrolhandlebackandforth several
times.
14. Do not removethecapfrom the hydraulictankor reservoir
whileyourlogsplitterisrunning.Hotoilunderpressurecould
causeinjury.
15. Thepressurereliefvalveonyoursplitterispresetatthefactory.
Do not adjustthe valve.Onlya qualifiedservicetechnician
shouldperformthisadjustment.
16, Completelydrainfueltankpriortostorage.Thisguardsagainst
accumulationoffuelfumeswhichcouldresultina firehazard.
17. Neverstorelogsplitteroutsidewithouta waterproofcover.Rain
willcauserustontheinsideofthecylinder.
_lb CUSTOMER RESPONSIBILITIES
1. Do notoperateyoursplitterin poor mechanicalconditionor
wheninneedofrepair_
2. Periodicallycheckthatallnuts,bolts,screws,hoseclampsand
hydraulicfittingsaretighttobesureequipmentisinsafework-
ingcondition.Whereappropriate,checkallsafetyguardsand
shieldstobesuretheyareintheproperposition.Neveroperate
yoursplitterwithsafetyguards,shieldsorotherprotectivefea-
turesremoved.Thesesafetydevicesareforyourprotection.
dl_ TOWING
1. Thisunitshouldnotbetowedonanystreet,highwayorpublic
roadwithoutcheckingtheexistingfederal,localorstatevehicle
requirements.Anylicensingormodificationssuchastaillights,
etc.,neededto complywiththe existingfederal,localorstate
vehiclerequirementsisthesoleresponsibilityofthepurchaser.
2. Beforetowing,be certainthe log splitteris correctlyand
securelyattachedtothetowingvehicle,andthesafetychains
areinplace.Leaveslackinchainsforturningallowance.
3. Do notallowanyoneto sitor rideon yoursplitter.Theycan
easilyfalloffandbeseriouslyinjured.
4