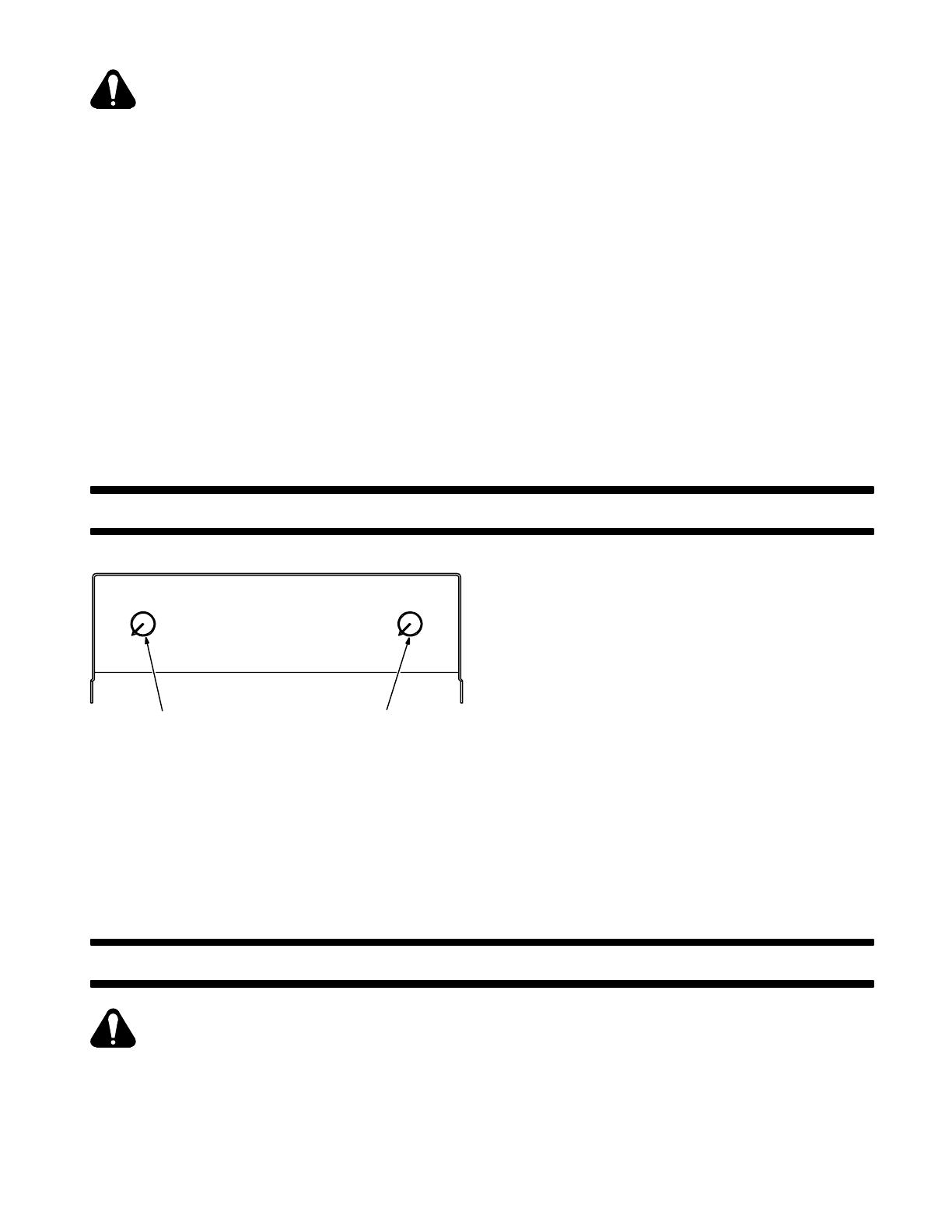
OM-895 Page 3
WARNING: ELECTRIC SHOCK can kill.
• Do not touch live electrical parts.
• Shut down welding power source and wire
feeder, and disconnect input power employing
lockout/tagging procedures before inspecting or
installing.
Lockout/tagging procedures consist of pad-
locking line disconnect switch in open position,
removing fuses from fuse box, or shutting off
and red-tagging circuit breaker or other discon-
necting device.
3-1. INSTALLATION
The remote control unit is designed to mount on top of
the dual wire feeder. To install the unit, proceed as fol-
lows:
1. Place unit on top of wire feeder with front panels fac-
ing same direction.
2. Loosen wire feeder wrapper screws (4) that match
the remote control unit wrapper screw slots.
3. Slide remote control unit down onto screws.
4. Tighten the wire feeder wrapper screws.
3-2. CONNECTIONS TO WIRE FEEDER (Figure 3-1
And Figure 3-2)
1. Connect 4-socket Amp 115 Volts AC/Contactor
Control plug to 115 Volts/Contactor receptacle on
rear of wire feeder control as follows: align keyway,
insert plug, and rotate threaded collar fully clock-
wise.
2. Connect 4-pin Amp Right Contactor Control plug to
Right Contactor Control receptacle on rear of wire
feeder control as follows: align keyway, insert plug,
and rotate threaded collar fully clockwise.
3-3. CONNECTIONS TO WELDING POWER
SOURCE (Figure 3-1 And Figure 3-2)
Connect 14-pin Amphenol 115 Volts AC/Contactor/Re-
mote Voltage Control plug to Control receptacle on front
of welding power source as follows: align keyway, insert
plug, and rotate threaded collar fully clockwise.
SECTION 4 − OPERATOR CONTROLS
SA-047 978-B
Left Voltage
Control
Right Voltage
Control
Figure 4-1. Front Panel View
4-1. VOLTAGE CONTROLS (Figure 4-1)
The VOLTAGE controls provide remote voltage control
within the welding power source load voltage range.
When the wire feeder Left control is active, the remote
control LEFT VOLTAGE control is active. When the wire
feeder Right control is active, the remote control RIGHT
VOLTAGE control is active. Rotating the VOLTAGE
controls in a clockwise direction increases the load volt-
age.
The scale surrounding the VOLTAGE controls is cali-
brated in percent and does not indicate an actual volt-
age value. The 0 (zero) setting represents welding pow-
er source minimum voltage, and 100 represents welding
power source maximum voltage.
IMPORTANT: The output voltage control on the weld-
ing power source must be in its maximum position when
used with the remote control unit in order for the remote
control to provide the full range of the welding power
source output voltage.
IMPORTANT: The VOLTAGE controls can be adjusted
while welding.
SECTION 5 − SEQUENCE OF OPERATION
WARNING: ELECTRIC SHOCK can kill;
MOVING PARTS can cause serious injury;
IMPROPER AIRFLOW AND EXPOSURE TO
ENVIRONMENT can damage internal parts.
• Do not touch live electrical parts.
• Keep all covers and panels in place while
operating.
Warranty is void if the welding power source is
operated with any portion of the outer enclosure
removed.
ARC RAYS, SPARKS, AND HOT SURFACES
can burn eyes and skin; NOISE can damage
hearing.
• Wear correct eye, ear, and body protection.
FUMES AND GASES can seriously harm
your health.
• Keep your head out of the fumes.
• Ventilate to keep from breathing fumes and
gases.
• If ventilation is inadequate, use approved
breathing device.