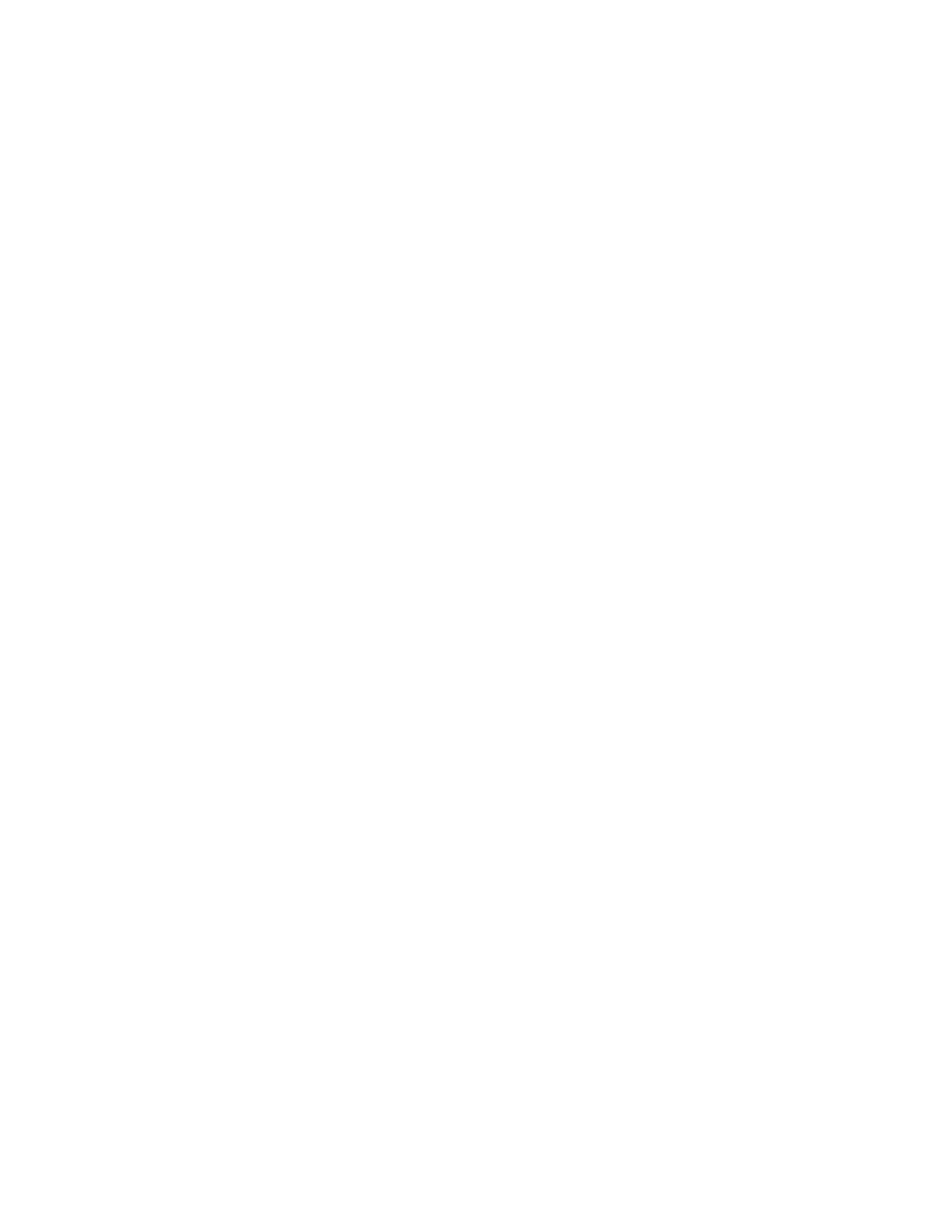
PARTS LIST
FLIGHT-A-ROUND DRIVE ASSEMBLY TYPE "D"
(CLOCKWISE DIRECTION - - - COUNTERCLOCKWISE DIRECTION)
ITEM
NO.
PART NO. DESCRIPTION QTY
REQ.
1 W -2-95461 Rail Weldment Assy (Includes Items 2 thru 4) 1
2 W-1-7118 Screw. SS Hex Hd Mach., 1/4-20 x 1/2" Ig. 8
3 W-1-7007 Lockwasher, SS Split. 1/4" 15
4 W-1-7905 Stat-0-Seal, 1/4" 2
5 W-1-5998 Nut, SS Hex, 3/8-16 5
6 W-1-7524 Lockwasher. SS Split, 3/8" 5
7 W-2-95173 Drive Arm Pivot Weldment 1
8 W-0-14146 Screw, SS Truss Hd Slotted Mach., 3/8-16 x 1-1/2" Ig 2
9 W-0-14185 Screw, SS Truss Hd Slotted Mach., 3/8.16 x 1" Ig. 3
10 W-1-7235 Micro Switch 1
11 W-1-7654 Connector, Straight Liquid Tight, 3/8" 1
12 W-1-95453 Overload Switch Bracket 1
13 W-1-7023 Lockwasher, Plated Split. 1/4" 10
14 M-1-3571 Screw, Hex Hd Plated Steel Cap. 1/4-20 x 1/2" Ig. 5
15 W-2-95158 Drive Base Support, R.H. 1
16 W-0-14784 Bolt. Hex Hd Plated Steel. 5/16-18 x 3/4" 9
17 W-1-8491 Screw. SS Truss Hd Slotted Mach., 1/4-20 x 5/8" Ig. 3
18 W-1-7146 Nut, SS Hex. 1/4-20 9
19 W-1-12977 Conduit Clamp. One Hole, 1/2" 2
20 W-1-7012 Nut, Hex, Plated Steel, 1/4-20 6
21 W-1-8348 Screw. Hex Hd Steel, 1/4-20 x 3/4" Ig. 2
22 W-1-7657 Bolt. Hex Hd, Plated Steel, 3/8-16 x 1-1/4" Ig. 2
23 W-1-7584 Washer, 16 Ga, SS Plat, 13/32" I.D.x 1" O.D. 2
24 W-1-16493 Washer, Nylon Pivot 4
25 W-1-16492 Sleeve, Driven Base Pivot 2
26 P-1-17245 Lockwasher, Plated Split, 3/8" 5
27 W -0-14785 Nut, Hex, Plated Steel. 3/8-16 7
28 W-1-95I62 Overload Spring Bar 1
29 1-9268 Compression Spring (.177 Dia. Wire) 1-1/32" I.D. x 2" high 2
30 W-1-95191 Spring Washer 4
31 M-1-15062 Bolt. Hex Hd Steel. 3/8-16 x 3-1/2" Ig. 2
32 W-1-95199 Drive Base End Panel 1
33 W-1-95193 Drive Belt Tightener Assy (Consists of Items 34 thru 38) 4
34 W-0-95192 Flat Plate 1
35 P-1-17235- Lockwasher, Plated Split, 5/16" 18
36 W-0-14786 Nut, Hex Plated Steel, 5/16-18 18
37 M-1-15069 Screw, Hex Hd Steel. Fully Threaded, 5/16-18 x 2-1/2" Ig 1
38 W-0-14099 Bolt. Carriage, Plated Steel, 5/16-18 x 3/4" Ig. 4
39 W-1-11312 Motor, 1/2 HP 115/230V Single Phase, Type 56-4 Frame 1
39A W-1-11314 Motor, 1/2 HP 208/230/460V Three Phase. Type 56-4 Frame 1
40 W-1-14945
1
41 W -1-9859 Washer. 16 Ga. SS Flat, .337" I.D. x 7/8" O.D. 2
42 W -1-95163 Motor Mount Hanger 1
43 W -0-95465 Bolt, Sq. Hd Plated Steel, 3/8-16 x 7" Ig. 1
44 W -1-11328
1
44A W -0-14753
1
44C W -0-10984
1
8