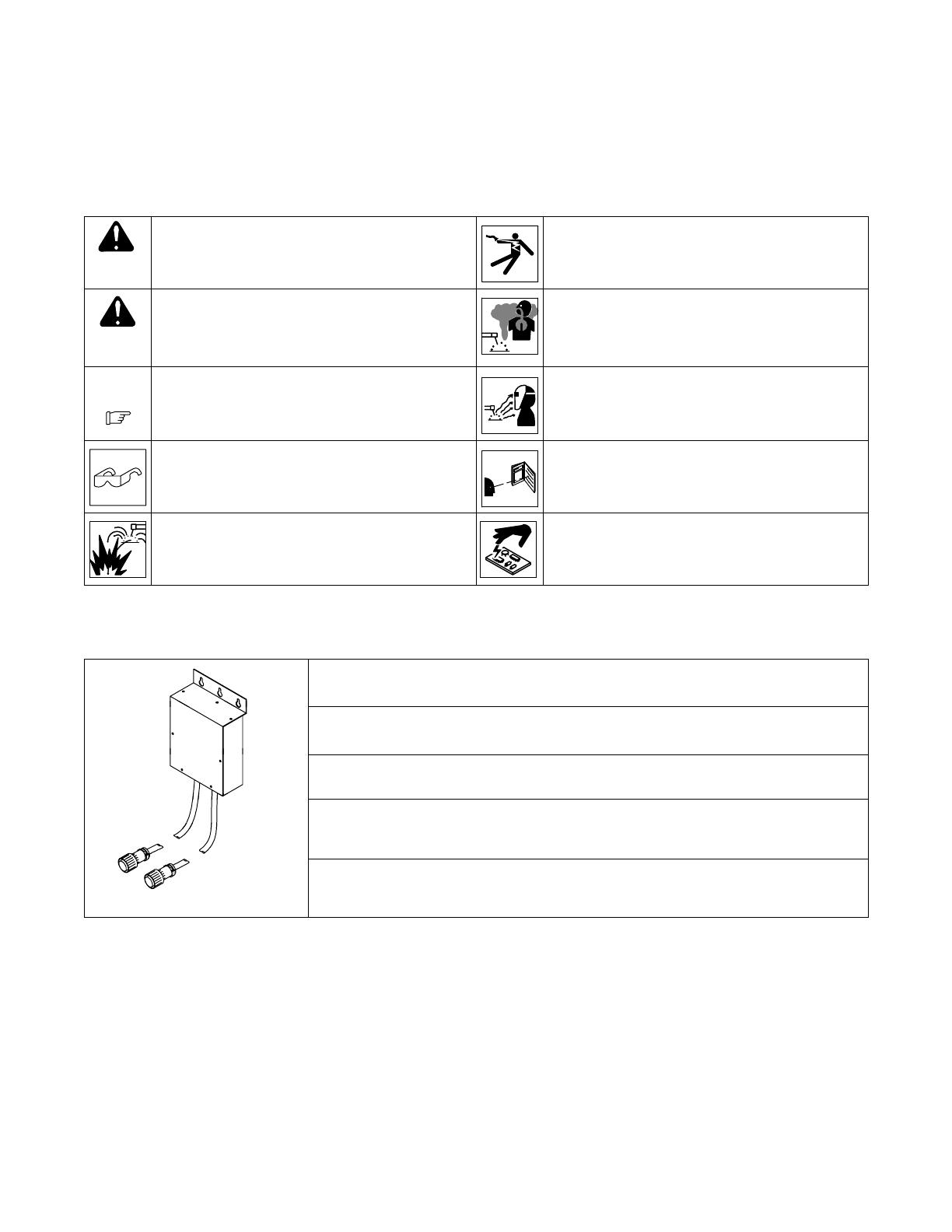
OWNER’S MANUAL
OM-201 344B
2007−07
For Paralleling Controller
1 Safety Symbol Definitions
DANGER! − Indicates a hazardous situation which, if not
avoided, will result in death or serious injury. The pos-
sible hazards are shown in the adjoining symbols or
explained in the text.
Beware of electric shock from wiring. Disconnect input
power before working inside machine. Reinstall all pan-
els and covers.
Indicates a hazardous situation which, if not avoided,
could result in death or serious injury. The possible ha-
zards are shown in the adjoining symbols or explained in
the text.
Breathing welding fumes and gases can harm your
health. Welding requires good ventilation. If ventilation is
impossible, such as when welding in a confined space,
use an air-supplied respirator.
NOTICE
Indicates statements not related to personal injury.
Indicates special instructions.
Arc rays can burn eyes and skin − wear a welding hel-
met with correct filter, and cover exposed skin with non-
flammable clothing.
Wear safety glasses with side shields. Have only trained and qualified persons install, operate,
or service this unit. Call your distributor if you do not
understand the directions. For WELDING SAFETY and
EMF information, read owner’s manual(s).
Welding sparks can cause fire or explosion. Move flam-
mables away. Do not weld on closed tanks or barrels −
they can explode. Clean tanks or barrels properly.
Static electricity can damage parts on circuit boards. Put
on grounded wrist strap before touching board.
2 Specifications
Allows Easy Connection Of Multiple Welding Power Sources For Increased Amperage Applications
Welding Power Source Must Have Full Remote 14-Pin Capability
Uses 24 volts AC, Input Power Supplied Through Welding Power Source 14-Pin Receptacle
Remote Control Connections Through 14-Pin Receptacle
802 737
Dimensions: 3 in (76 mm) Deep, 7-1/2 in (191 mm) Wide, 10 in (254 mm) High
Weight: 6.1 lb (2.8 kg)