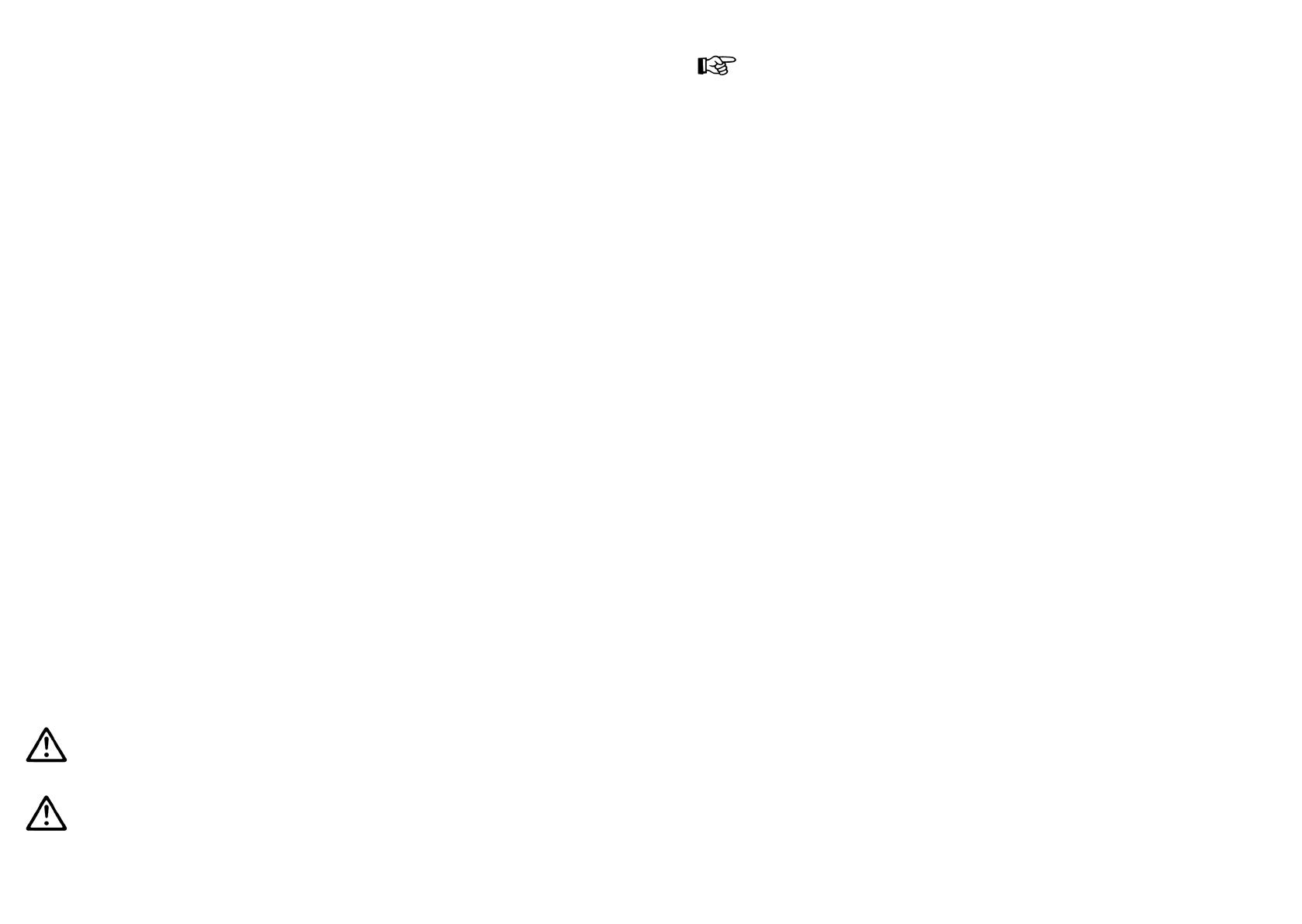
3938
With internal control:
Actuation of the 3/2-way control valve directs control air into the cylinder inside the
gun so as to open - in sequence - the atomizing air and the material input.
The shape of the spray is set on the gun with the models PILOT WA 900 / WA 920-
HVLP/ WA 940-HVLP
PLUS
/ WA 903-K and WA 923-HVLP-K using regulating screws
(Pos. 28 and 29).
If the control air through the 3/2-way valve is interrupted, compressed air remaining
in the cylinder chamber will first escape. The spring pressure of the piston spring
subsequently pushes the material needle to its original position, closes the material
supply and finally the spray air.
Without internal control:
The atomizer air (round and wide jet air) should first be switched on via an external
3/2-way control valve provided by the customer. Then the control air is opened via a
second 3/2 way valve, which presses both the piston and the material needle back
in order to open the material supply.
For the models PILOT WA 905/ WA 925-HVLP/ WA 945-HVLP
PLUS
/ WA 908-K and
WA 928-HVLP-K the shape of the spray jet is adjusted via the two customer supplied
compressed air regulators in the plant.
If the control air is interrupted by the 3/2-way control valve, spring pressure will move
the piston and the material needle back to their initial position and close the material
supply to the material nozzle. The atomizer air should then be switched off.
The material flow volume is on all models set via the material pressure and the cap
(item 26). The flow of material in the automatic spray gun series PILOT WA 900 can
also be manually opened by means of the drawbar (Pos. 27).
The spray guns of the PILOT WA 900 series can be connected to material pressure
tanks or pumping systems.
The models PILOT WA 920-HVLP/ WA 925-HVLP/ WA 923-HVLP-K and
WA 928-HVLP-K are pure low-pressure spray guns working with a spraying air
pressure of 0.7 bar at an intake air pressure of 3,3 bar.
With the models PILOT WA 940-HVLP
PLUS
bis WA 945-HVLP
PLUS
the intake air
pressure ranges from 3.0 to 3.3 bar for a spraying air pressure of 1.2 to 1.4 bar.
3 Safety Warnings
3.1 Safety Warning Symbols
Warning
This pictograph and the accompanying warning note „Warning“ indicate possible
risks and dangers for yourself. Possible consequences: Injuries of any kind.
Caution
This pictograph and the accompanying warning note „Caution“ indicate possible
damage to equipment. Possible consequences: Damage to equipment, workpieces,
etc.
Notice
This pictograph and the accompanying note „Notice“ indicate additional and useful
information to help you handling the spray gun with even greater confidence and
efficiency.
3.2 Generally Applicable Safety Precautions
â–º All applicable accident prevention rules and regulations as well as other recognis-
ed industrial safety and health rules and regulations must be observed at all times.
â–º Use the spray gun only in well-ventilated rooms. Fire, naked flames and smoking
are strictly prohibited within the working area. WARNING – during the spraying of
flammable materials (e.g. lacquers, adhesives, cleaning agents, etc.), there is an
increased risk to health as well as an increased risk of explosion and fire.
â–º You must ensure that the spray gun is properly earthed (grounded) either separa-
tely or in connection with the equipment with which it is being used (max. resistance
10
6
Ω).
â–º Before carrying out maintenance or servicing work, always ensure that the air and
material feed to the spray gun have been de-pressurised. Risk of injury!
â–º When spraying materials, do not place your hands or other parts of the body in
front of the pressurised nozzle or the spray gun. Risk of injury!
â–º Never point the spray gun at persons or animals. Risk of injury!
â–º Always observe the spraying and safety instructions given by the manufacturers
of the spraying material and the cleaning agent. Aggressive and corrosive
materials in particular can be harmful to health.
â–º Always wear hearing protection when using the gun or when in the vicinity of a
gun that is in use. The noise level generated by the spray gun is approx. 86 dB(A).
â–º Exhaust air containing particles (overspray) must be kept away from the working
area and personnel. In spite of these measures, always wear the regulation
breathing masks and protective overalls when using the gun. Airborne particles
represent a serious health hazard!
â–º After carrying out assembly or maintenance work, always ensure that all nuts,
bolts and screw connections have been fully tightened before the gun is used.
â–º Use only original replacement parts, since WALTHER can only guarantee safe
and fault-free operation for original parts.
â–º For further information on the safe use of the spray gun and the spraying
materials, please contact WALTHER Spritz- und Lackiersysteme GmbH,
D-42327 Wuppertal, Germany.
4 Assembly / Installation
4.1 Radial or circulation method
The spray guns series WA 900 arrive completely assembled from the factory. They
are by standard delivered with a sealing pin (Pos. 30).