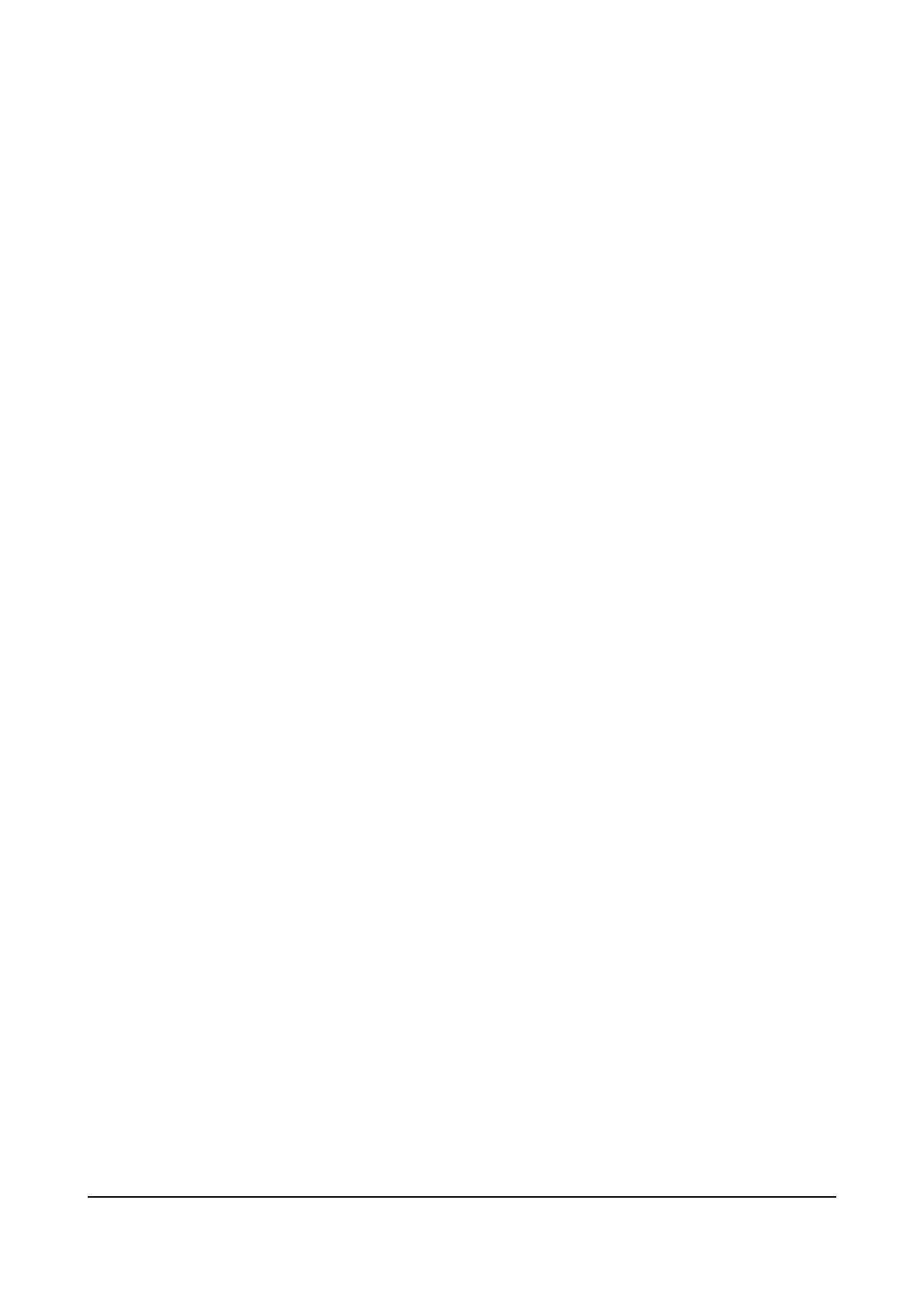
Contents Page
CAN-CBM-AI410 Hardware Manual Rev. 1.1 1
1. Overview .................................................................... 3
1.1 Module Description ..................................................... 3
1.2 Summary of Technical Data .............................................. 4
1.2.1 General Technical Data .......................................... 4
1.2.2 CAN- and Microcontroller Units ................................... 4
1.2.3 Analog Inputs .................................................. 5
1.2.4 Software Support ............................................... 5
1.3 Order Notes ........................................................... 6
2. View of the Housing and LED Description ........................................ 7
2.1 Housing .............................................................. 7
2.2 Front View with Position of LEDs and Coding Switches ........................ 7
2.3 LED-Displays ......................................................... 8
3. Hardware Configuration ...................................................... 11
3.1 PCB-View ........................................................... 11
3.2 Default Setting of Bridges and Coding Switches ............................. 12
3.3 Manual Configuration via Coding Switches ................................. 13
3.3.1 Save Default Configuration in EEPROM ............................ 13
3.3.2 Changing Parameters ........................................... 14
3.3.3 Setting the Module Number ...................................... 16
4. Description of Units .......................................................... 17
4.1 Transmit and Receive Circuit of CAN-Interface (Physical Layer) ................ 17
4.2 Analog Inputs ......................................................... 17
5. Connector Assignments ....................................................... 19
5.1 CAN-Bus (X200, 5-pole Combicon Style) .................................. 20
5.2 Analog Inputs and Power Supply (X300, 12-pole Combicon Style) ............... 21
6. Correctly Wiring Electrically Isolated CAN Networks ............................. 23