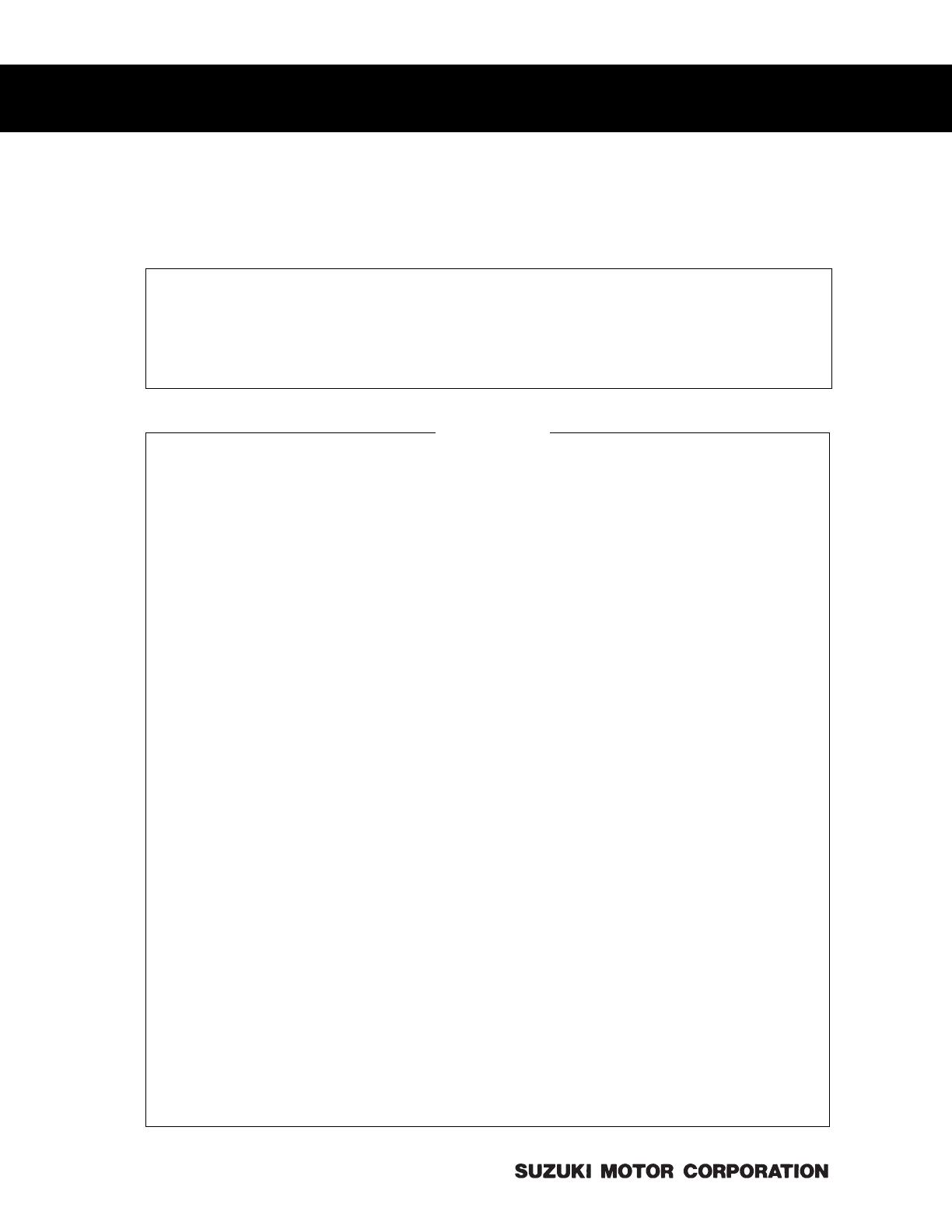
RV125K7 (’07-MODEL) 1
CONTENTS
RV125K7 (’07-MODEL)
© COPYRIGHT SUZUKI MOTOR CORPORATION 2006
This manual describes service data, service specifications, troubleshooting for FI system and
servicing procedures which differ from those of the K6 (’06-model).
NOTE:
• Any differences between the K6 (’06-model) and K7 (’07-model) in specifications and
service data are indicated with an asterisk mark (*).
• Please refer to the K6 (’06-model) service manual and service information for details
which are not given in this manual.
ABBREVIATIONS USED IN THIS MANUAL ....................................................... 3
SPECIFICATIONS (RV125K7) ............................................................................. 4
ENGINE ....................................................................................................... 4
DRIVE TRAIN .............................................................................................. 4
CHASSIS ..................................................................................................... 5
ELECTRICAL .............................................................................................. 5
CAPACITIES ............................................................................................... 5
PERIODIC MAINTENANCE SCHEDULE ............................................................ 6
PERIODIC MAINTENANCE CHART .......................................................... 6
MAINTENANCE AND TUNE-UP PROCEDURES ............................................... 7
THROTTLE CABLE PLAY.......................................................................... 7
FUEL LINE .................................................................................................. 8
SDS CHECK ......................................................................................................... 9
FI SYSTEM DIAGNOSIS .................................................................................... 13
PRECAUTIONS IN SERVICING ............................................................... 13
FI SYSTEM TECHNICAL FEATURES...................................................... 20
ECM TERMINAL ....................................................................................... 29
SELF-DIAGNOSIS FUNCTION................................................................. 30
FAIL-SAFE FUNCTION............................................................................. 32
FI SYSTEM TROUBLESHOOTING .......................................................... 33
SENSORS........................................................................................................... 79
CKP SENSOR INSPECTION .................................................................... 79
CKP SENSOR REMOVAL AND INSTALLATION .................................... 79
IAP/TP/IAT SENSOR INSPECTION ......................................................... 79
ET SENSOR INSPECTION ....................................................................... 79
ET SENSOR REMOVAL AND INSTALLATION ....................................... 80
TO SENSOR INSPECTION....................................................................... 80
TO SENSOR REMOVAL AND INSTALLATION....................................... 81
HO2 SENSOR INSPECTION .................................................................... 81
HO2 SENSOR REMOVAL AND INSTALLATION .................................... 81