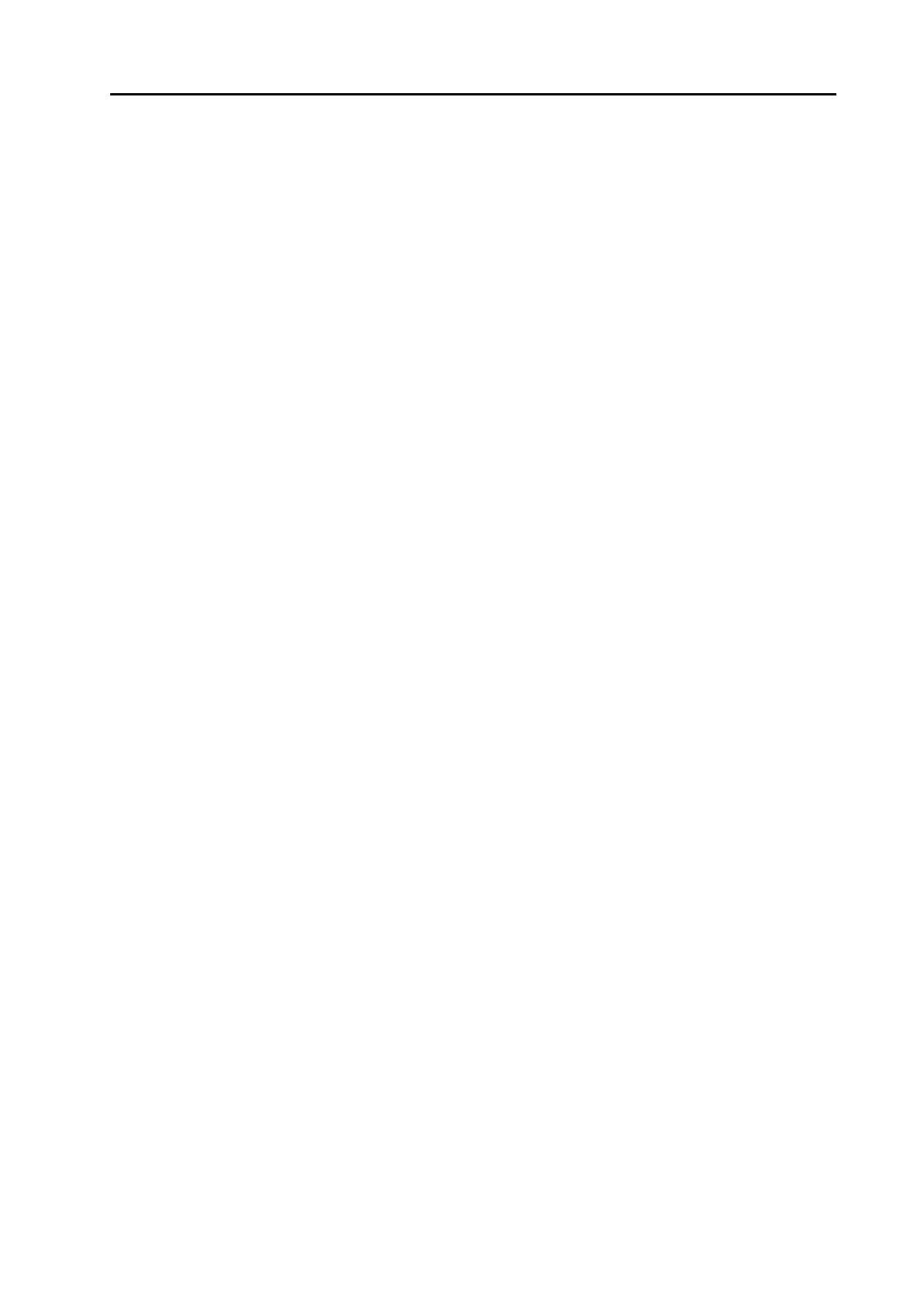
7/48
Table of Contents
1. Specifications .................................................................................................................. 8
1.1. Principle - Intended Use .................................................................................................... 9
1.2. Organisational Measures.................................................................................................. 9
1.3. Staff Selection and Qualification, General Obligations .................................................. 10
1.4. Safety Notes on the Operating Phases ........................................................................... 11
1.4.1. Transport, Assembly and Installation ..................................................................... 11
1.4.2. Commissioning ....................................................................................................... 11
1.4.3. Operation ............................................................................................................... 11
1.4.4. Special Work in the Scope of Use of the Machine ................................................ 12
1.4.5. Relocation of the Masonry saw ............................................................................. 12
1.5. Reference to Special Types of Danger ............................................................................ 13
1.5.1. Dangers to the Operator Caused by the Machine .................................................. 13
1.5.2. Electrical Energy .................................................................................................... 13
1.5.3. Dust........................................................................................................................ 13
1.5.4. Noise ...................................................................................................................... 13
1.6. Transport......................................................................................................................... 14
1.7. Packaging and Storage ................................................................................................... 14
1.8. Environmental Protection ................................................................................................ 14
1.9. Disposal .......................................................................................................................... 14
2. Device Description......................................................................................................... 15
2.1. Designation of the Machine Part .................................................................................... 15
2.2. Protective Devices .......................................................................................................... 15
2.3. Technical Data ................................................................................................................ 17
2.4. Sound Power Level ......................................................................................................... 17
3. Commissioning ............................................................................................................... 18
3.1. Connections and Operating Materials ............................................................................ 18
3.2. Tool Selection ................................................................................................................. 18
3.3. Mounting handles ........................................................................................................... 19
3.4. Mounting wheel set ........................................................................................................ 19
3.5. Setting depth stop on the DTS 400 ................................................................................. 20
3.6. Setting depth stop on the DTS 600 ................................................................................. 20
3.7. Setup .............................................................................................................................. 21
3.8. Locking Mechanism Cutting Table .................................................................................. 21
3.9. Height Adjustment of the Saw Head .............................................................................. 22
3.10. Adjust Inclination of the Saw Head (only DTS 400) ...................................................... 22
3.11. Saw Blade Installation DTS 400 ................................................................................... 23
3.12. Saw Blade Installation DTS 600 ................................................................................... 24
4. transport ......................................................................................................................... 25
4.1. Transport Position ........................................................................................................... 25
4.2. Relocation by Crane ........................................................................................................ 25
4.3. Transport Via the Wheel Set .......................................................................................... 26
5. Operation ........................................................................................................................ 27
5.1. Safety ............................................................................................................................. 27
5.2. Start Preparations ........................................................................................................... 27
5.3. Cutting with the Masonry saw ....................................................................................... 27
5.4. Shortening Cuts with the Masonry saw.......................................................................... 28
5.5. Diagonal Cuts ................................................................................................................. 28
6. Disassembly ................................................................................................................... 29
7. Servicing......................................................................................................................... 29
7.1. Maintenance ................................................................................................................... 29
7.2. Troubleshooting Table .................................................................................................... 30
7.3. Torques of Screw Connections ....................................................................................... 31
7.4. Maintenance plan ........................................................................................................... 32
8. Warranty......................................................................................................................... 33
9. Spare parts list ............................................................................................................... 34
9.1. DTS 400 .......................................................................................................................... 34
9.2. DTS 600 .......................................................................................................................... 39