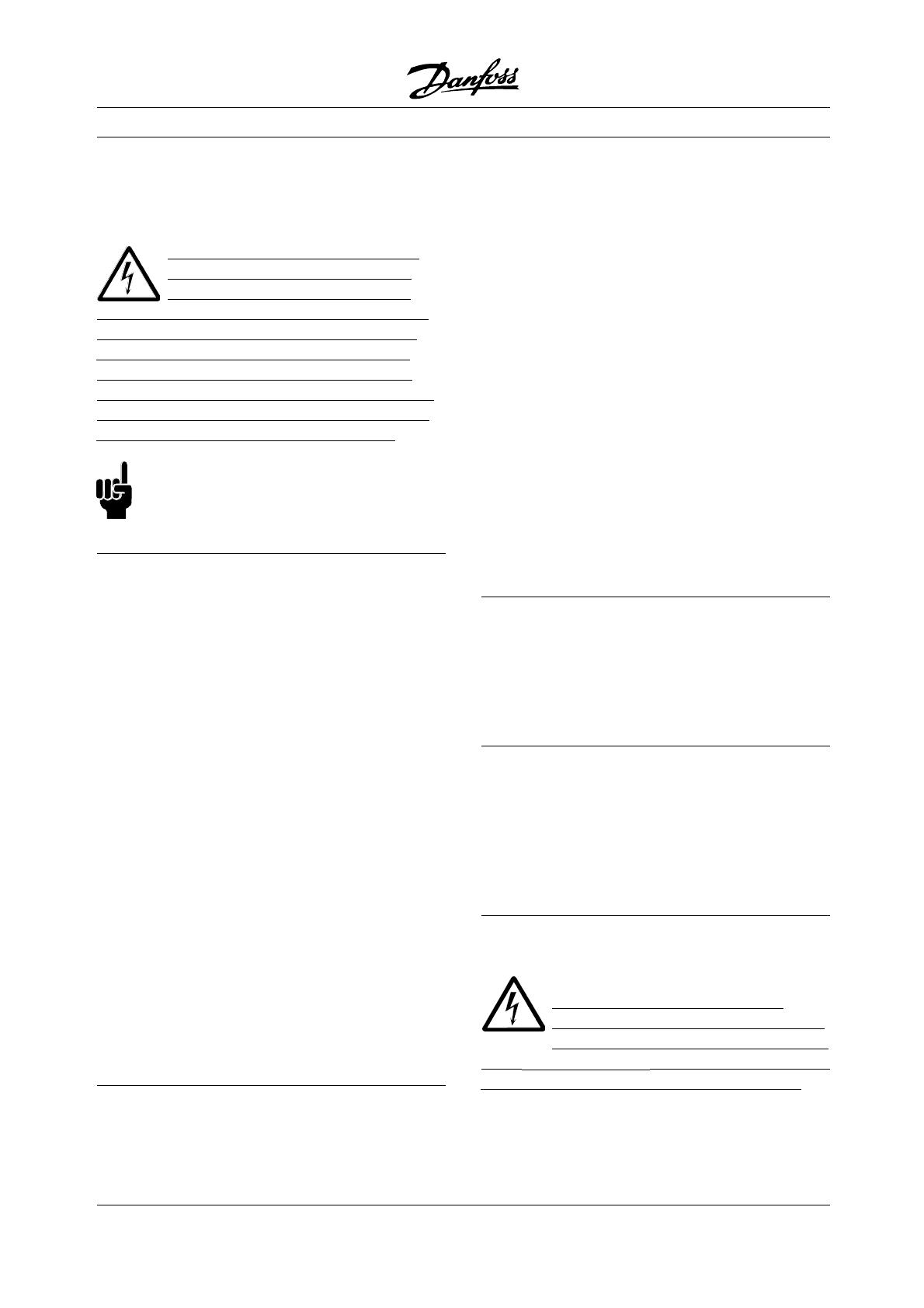
VLT
®
FCD Series
■General information about electrical installation
■High voltage warning
The voltage of the adjustable frequency
drive is dangerous whenever the drive
is connected to the AC line. Incorrect
installation of the motor or drive may cause damage
to the equipment, serious injury or death. Comply
with the safety instructions in this manual as well
as local and national rules and safety regulations.
Touching electrical parts may be fatal - even after the
equipment has been disconnected from the AC line.
Wait at least 4 minutes for current to dissipate.
NOTE
It is the responsibility of the user or installer
to ensure correct grounding and protection in
accordance with national and local standards.
■Cables
The control cable and the power cable should be
installed separately from motor cables to prevent
noisetransfer. Asaruleadistanceof8in(20cm)is
sufficient, but it is recommended that the distance
is as great as possible, particularly when cables are
installed in parallel over large distances.
For sensitive signal cables such as telephone or data
cables the greatest possible distance is recommended.
Please note that the required distance depends on the
installation and the sensitivity of the signal cables, and
that for this reason exact values cannot be given.
When being placed in cable trays, sensitive cables
may not be placed in the same cable tray as the
motor cable. If signal cables run across power
cables, this is done at an angle of 90 degrees.
Remember that all noise-filled inlet and outlet cables
to a cabinet must be shielded/armoured.
See also EMC-compliant electrical installation.
Cable glands
It must be assured that appropriate cable glands needed
for the environment are chosen and carefully mounted.
■Shielded/armoured cables
The shield must have low HF impedance, which is
achieved by a braided shield of copper, aluminium or
iron. Shield reinforcement intended for mechanical
protection, for example, is not suitable for EMC-correct
installation. See also Use of EMC-correct cables.
■Extra protection
ELCB relays, multiple protective grounding or grounding
can be used as extra protection, provided that local
safety regulations are complied with. In the case of an
ground fault, a DC content may develop in the faulty
current. Never use an RCD (ELCB relay), type A, as it
is not suitable for DC faulty currents. If ELCB relays
are used, local regulations must be complied with.
If ELCB relays are used, they must be:
- Suitable for protecting equipment with a DC content
in the faulty current (3-phase bridge rectifier)
- Suitable for a pulse-shaped, brief discharge
on power-up
- Suitable for a high leakage current.
See also RCD Application Note MN.90.GX.02.
■High voltage test
A high voltage test can be performed by short-circuiting
terminals U, V, W, L1, L2 and L3, and applying
max. 2160 V DC in 1 sec. between this
short-circuit and PE-terminal.
■Electronics purchased without installation box
If the electronic part is purchased without the
Danfoss installation part, the ground connection
must be suitable for high leakage current. Use
of original Danfoss installation box or installation
kit 175N2207 is recommended.
■Caution
PE connection
T
he metal pin in the corner(s) of the
electronic part and the bronze spring in the
corner(s) of the installation box a
re essential
for the protective ground connection. Make sure they
are not loosened, removed, or violated in any way.
MG.04.B6.22 - VLT is a registered Danfoss trademark
10