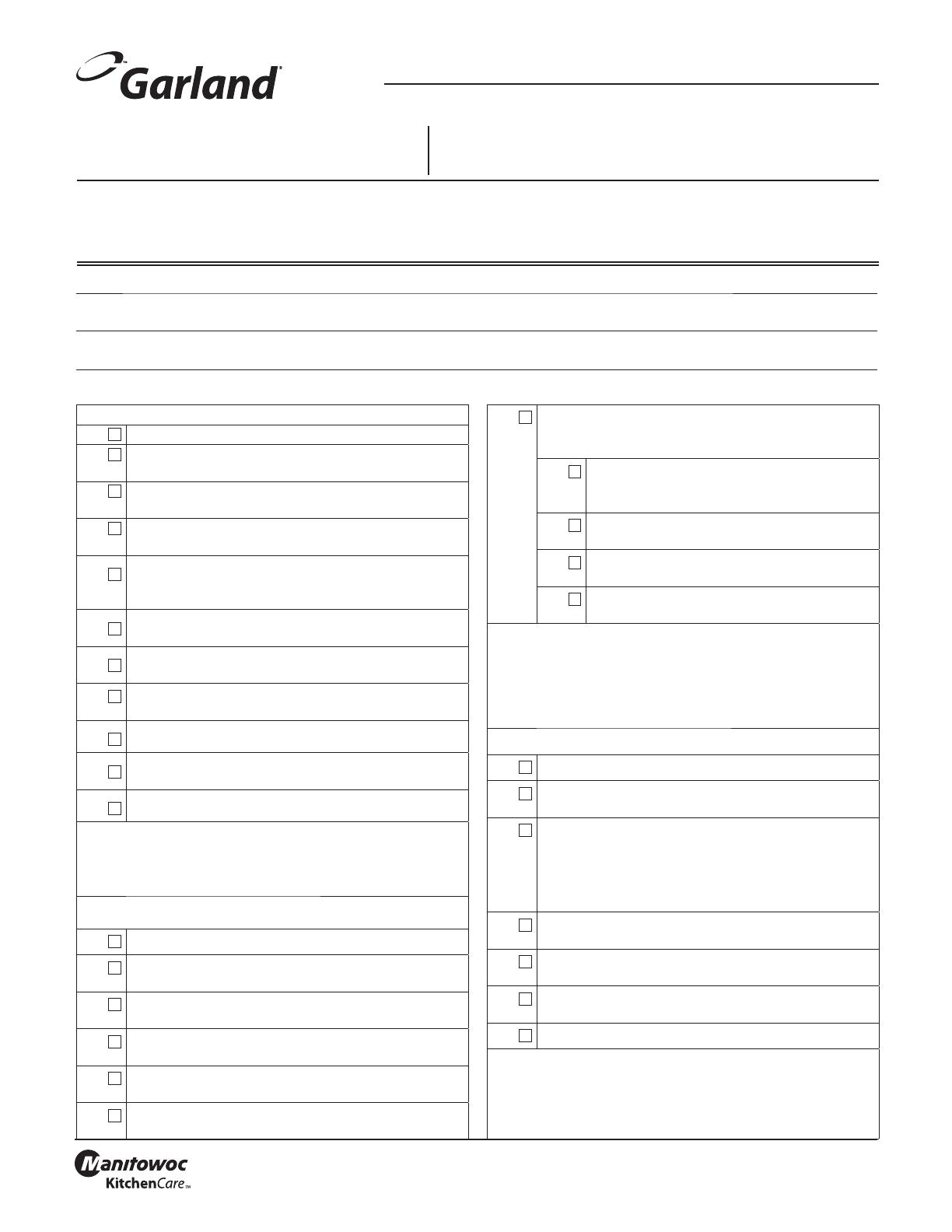
1 of 2
Document Number: GAR_CL_0003_en 5/15
GARLAND
1177 KAMATO ROAD, MISSISSAUGA, ONTARIO, CANADA. L4W1X4
844724CARE 2273
WWW.GARLANDGROUP.COM
Induction Generator
1.
All cables at the device are labelled?
2.
All cables are connected and the screws on the plugs are
fastened?
3.
The tongue from the RJ45 cable is snapped into the
generator socket?
4.
Coil and supply cables are routed separately and sorted
from other low voltage and communication cables?
5.
The installation clearances are maintained — air intake
and exhaust vents, at least 40mm(1.6”) and all sides, at
least 10 mm(0.4”)?
6.
Is there adequate ventilation? For example, separated
paths for fresh air and exhaust air?
7.
Ambient air temperature around the generator is
≤ 40°C (104
o
F) when it is in operation?
8.
Ensure there is no moisture, hot or grease laden air that
goes through the air inlet?
9.
The generator is easily accessible for service?
10.
It is highly recommended to install grease filters to clean
the intake air. Are grease filters installed?
11.
Grease filters can be removed easily for cleaning?
Comments:
Control Unit
12.
All cables at the device are labelled?
13.
All cables are connected and the screws on the plugs are
fastened?
14.
The tongue from the RJ45 cable is snapped into the
control unit socket?
15.
Control unit is mounted securely (mounting brackets
provided)?
16.
Service interface (IR window) is accessible for service?
Installation clearance, minimum 38 mm (1.5”).
17.
Ambient air temperature around the control unit is
≤ 40°C (104
o
F) when it is in operation?
18.
(Outside of the USA/Canada) If a Sicotronic energy
optimization is connected, check if the yellow wire is
connected at RED.
19.
Switch the induction unit on, put a pot of water
on the field and read the EAMMN_Modul the
status.
20.
LED a On? (It is illuminated if the generator
switched on).
21.
LED b On? (It is illuminated if the potentiometer
is between 8 and 12).
22.
LED c On? (It is illuminated if the generator takes
full energy).
Comments:
Coil Carrier
23.
All cables and CONNECTIONS are labelled?
24.
All cables are connected and the screws on the plugs are
fastened?
25.
Coil assemblies must be pressed against the glass-top
with an even compression or contact pressure. Coil
compression is measured by the coil assembly mounting
bolts protruding below the carrier frame by about 5mm.
Is each mounting bolt protruding about 5mm?
26.
Coil assemblies have an even contact pressure against
the glass-top?
27.
There is no ferromagnetic material (installation and
mounting frame) in proximity to the coil?
28.
There is natural air flow or forced ventilation in the coil
area?
29.
Correct glass-top for the model is installed?
Comments:
Today’s Date:
(Day/Month/Year)
Installation Date:
(Day/Month/Year)
Installation
Company:
Model Number:
Store
Contact:
(Name, Phone#)
Serial Number:
Store Name,
Address:
Voltage:
Checklist
Installation Checklist for Induction RTCS
®
mp
Module-
Line Equipment
• This checklist is designed as an installation inspection tool for Fabricators and Installers.
• Service Technicians can also use this checklist to diagnose any potential installation issues.
• We recommend to use one checklist per appliance installed.
• Inspect and ensure client’s cookware is suitable for cooking on the induction equipment.