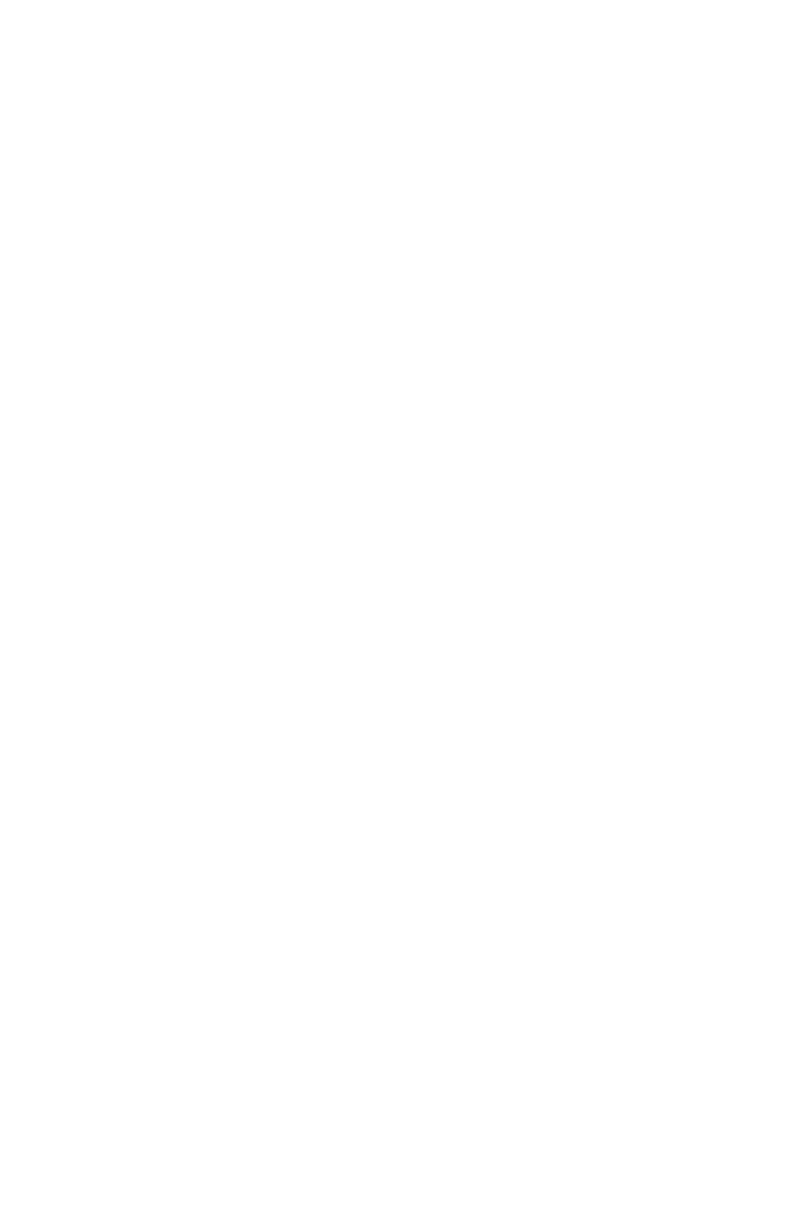
ACC
101,102A,103,301A,310,320
ACCELEROMETERS OPERATOR'S MANUAL
TABLE OF CONTENTS
SECTION
1
- INTRODUCTION
....
..
.......
.
.........
.
.......................
.
.............
.
........ ..1
SECTION 2 -
·UNPACKING
YOUR ACCELEROMETER ...................... 1
SECTION
3 -
UNDERSTANDING YOUR ACCELEROMETER ............
2
What is an Accelerometer?.......
.
.
.
........
..
.......
.
.........
.
.......................
.
.............
.
......
2
How Does it Work?
..
..................
.
.......
.
...............................
.
.............................
...
.
.
2
High Impedance or Low Impedance?
..
..
....
.
..........
.
...........................
.
..
.
..
.
...
.
....
..
2
Low Impedance Micro Circuit
..
....................
.
.
.
.
.
...
.
..
.
.
....
.
...
.
.............
...
....
..
....
.
.......
3
Noise in Accelerometers
..
.....................
.
..........
..
........
...
.
..........
.
.......................... .
3
General Characteristics ...............
.
...
.
.
.
........
.
.
..
...................
...
..........
..
..................... 4
SECTION 4 - POWER REQUIREMENTS ..............................................
5
Power Supplies ......
.
..
.
.
..
.......
.
..
.
......
.
...
.
...............................................................
5
SECTION 5 - CONNECTOR WIRING ...................................................
7
Coaxial Connectors..........
.
..
.
....
.
....
.
....
..
..........
.
.......................... ..
.
.........
.
...
.
.......
7
Two Pin Connectors..........
.
..
.
....
.
....
.
....
..
..........
.
............................
.
.........
.
...
.
.......
7
Four Pin Connectors
...
.
........
.
..........
..
................
.
...
.
...........................
..
.........
..
.....
7
SECTION 6 - CABLING TECHNIQUES.................................................
8
Splicing and Extending Cables..
.
....
.
....
..
..........
.
............................
.
.........
.
...
.
........ .
8
Securing Cables
.
.
...................
.
...
.
.........
..
.......
.
...............
.
............
..
.......................
8
SECTION 7 - MOUNTING THE ACCELEROMETER ............................ 10
Stud Mounting
.
.
..................
..
.................
.
...
.
...
.
....................
.
........................
.
.......
1
0
Adhesive Mounting
.
.
...
...
.
...............
.
.
..
...
.
.........
...
.........
..
........
...
.
.
........................
1
0
Adhesive Mounting Bushings.........
.
.
..
...
.
.........
...
.........
..
........
...
.
.
.......................
11
Magnetic Mounting…………..........
..
.
.....
.
.........
..
.......
.
.....
.
...
.
............
....
.
...............
12
SECTION 8 - SPECIFICATIONS.......................................................... 1
4
Basic Sensitivity ................
.
...
.
..
.
....
.
..............
.
...
.
.......
.
.
..
......
.
...................
..
......
..
.. 14
Basic Frequency Response ........
..
..
...
..
..
....
...............
..
..............
..
.......
.
....
..
.......... 14
ACC 101 Specifications .......
.
.......
....
........
.
............
...
.....
.
......................
...
........... 15
ACC 102A Specifications ..................
..
............................
.
..........
..
..............
..
...... 16
ACC 103 Specifications
.
........
..
.........
.
....
...
..........
.
............................................... 17
ACC 301A Specifications .....
.
...
.
........
....
...
.....
.
..
.
..........
..
....
......
.
........
.............
..
... 18
ACC 310 Specifications
.
........
..
.........
.
....
...
..........
.
............................................... 19
ACC 320 Specifications .....
.
...
.
........
....
...
.....
.
..
.
..........
..
....
......
.
........
.............
..
...... 20
Notes……………………………………………………………………………………. 21
WARRANTY………………………………………………………………………….… 22