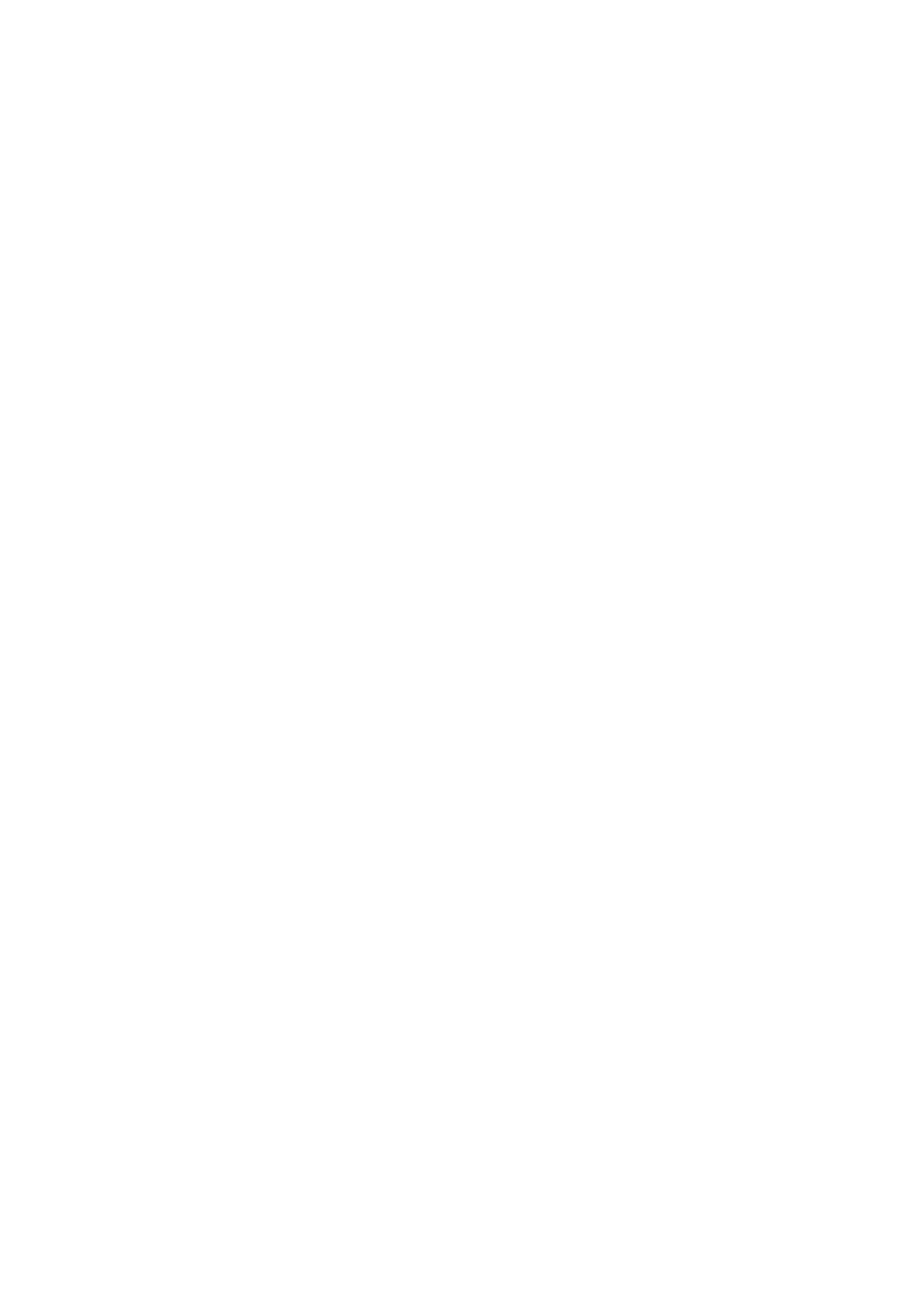
Contents Page:
Part 3: Service Instructions Cl. 975 - 1 - 5
1. General ................................................. 3
2. Machine Head ............................................. 4
2.1 LoopingStroke............................................. 4
2.2 NeedleBarHeightandClearanceoftheHookPointtotheNeedle................ 5
2.3 NeedlePlate .............................................. 6
2.3.1 LateralPositionoftheNeedlePlateCarrier............................. 6
2.3.2 UpperandLowerPositionoftheNeedlePlateCarrier....................... 7
2.3.3 TimingoftheSwitchOperation.................................... 8
2.3.4 Speedof“NeedlePlateUpandDown”............................... 9
2.4 BobbinCaseOpener.......................................... 10
2.4.1 HeightoftheFinger .......................................... 10
2.4.2 SizeoftheOpeningGap(PositionoftheFingerRun)andFingerDepth ............ 11
2.4.3 TimingtheOpening .......................................... 12
2.5 PressureFoot ............................................. 13
2.5.1 PressureFootPressure........................................ 13
2.5.2 HeightAdjustmentRange....................................... 14
2.5.3 TimingofthePressureFootMovement ............................... 15
2.6 ThreadControllerSpring ....................................... 16
2.7 ThreadTensionOpening ....................................... 17
2.8 Lubrication ............................................... 18
2.8.1 RegulatingtheLubrication ...................................... 19
2.9 SewingArm............................................... 21
2.9.1 PositionoftheSewingArm...................................... 21
2.9.2 EndPositionDampeningoftheCylinder............................... 22
2.9.3 TimingoftheOperationoftheSwitches............................... 23
2.10 AdjustmentScrewsfortheTimingBelt................................ 24
3. Thread Trimmer ............................................ 25
3.1 FunctionSequence .......................................... 25
3.2 PositionoftheBasePlateandtheGuideCurve .......................... 26
3.3 ClearancebetweentheDriveSegmentandGuideCurve ..................... 27
3.4 CounterKnifeandThreadPullKnife................................. 28
3.5 CounterKnifePressure ........................................ 29
4. Clamping Table ............................................ 30
4.1 LargeGuideCurve........................................... 30
4.1.1 AttachingtheAluminiumStrips.................................... 31
4.2 ChangingtheStitchLength...................................... 32