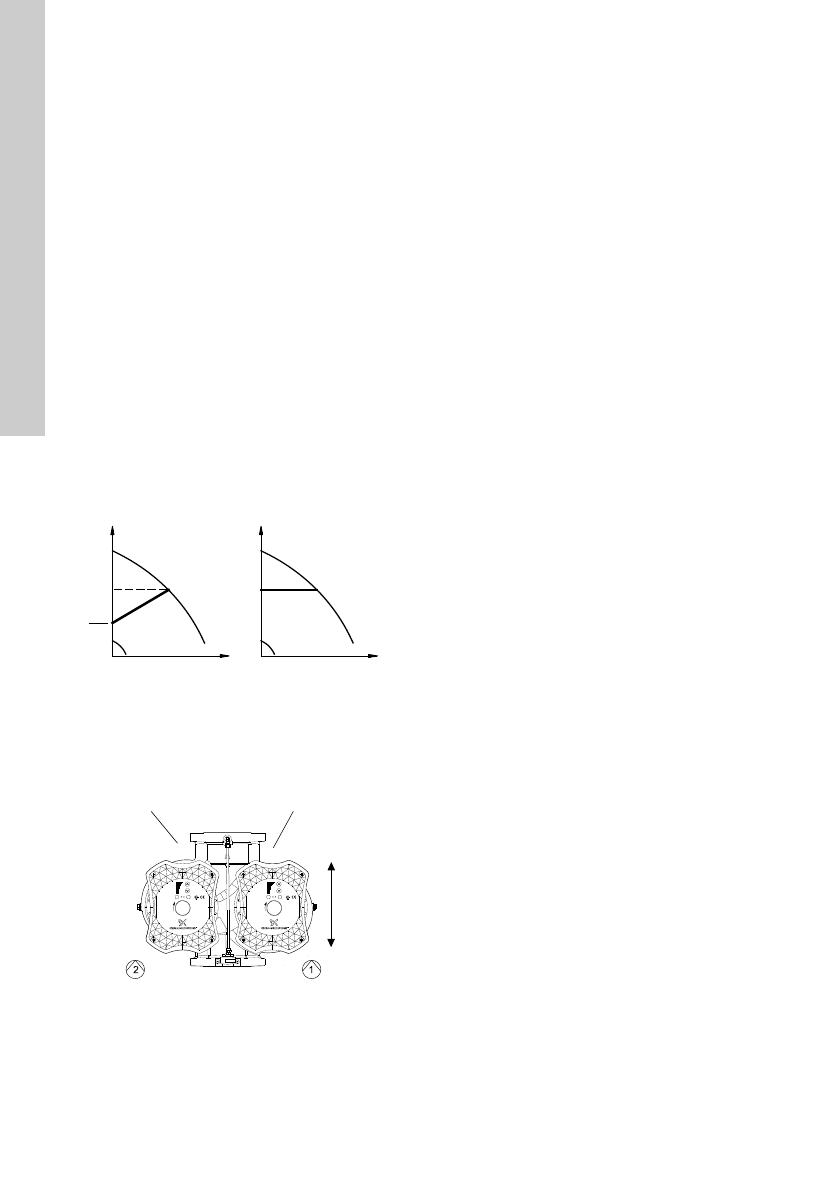
English (GB)
10
7. Functions
Some functions can only be selected with the
Grundfos R100 remote control. Where and how the
various settings are made appear from
section 8. Setting the pump.
7.1 Control modes
The UPE(D) FZ pumps can be set to the control
mode which is most suitable for the individual
system.
Two control modes are available:
• proportional pressure (factory setting)
• constant pressure.
Proportional-pressure control
To be set on the control panel or with the R100.
The pump head is reduced at falling water demand
and increased at rising water demand. See fig. 8.
This is the factory setting as, in most cases, this is
the optimum control mode, and at the same time
it consumes the least energy.
Constant-pressure control
To be set on the control panel or with the R100.
The pump maintains a constant pressure,
irrespective of water demand. See fig. 8.
Fig. 8 Pressure control
7.2 Control of twin-head pumps
The factory setting can be changed with the R100.
Fig. 9 Master and slave pumps
Four operating modes are available. The selection of
operating mode depends on whether reliability,
lifetime or performance has top priority.
• Alternating operation (factory setting).
Pump operation alternates every 24 hours.
If the power supply to the pump has been
switched off, any of the pumps may start when
the power supply is switched on again.
Reaction in case of fault: In case of fault in one
pump, the duty pump will operate continuously as
a single-head pump.
• Standby operation.
The master pump is operating continuously.
Every 25 hours the slave pump will start and run
for approx. 10 seconds to prevent it from seizing
up.
Reaction in case of fault: If the master pump
stops due to a fault, the slave pump will operate
continuously as a single-head pump.
• Synchronous operation.
The pumps are operating at the same motor
frequency. This operating mode is suitable if the
flow demand exceeds the flow of one pump.
Reaction in case of fault: In case of fault in one
pump, the duty pump will operate continuously as
a single-head pump.
• Single-pump operation.
The pumps are operating completely
independently of each other without internal
communication, but the twin-head cable must
be connected. All functions of each pump are
identical to those of a single-head pump.
All the other functions mentioned in sections
7.1 Control modes to 7.13 Remote control are
possible in the four operating modes.
7.2.1 Why select single-pump operation
Select single-pump operation
• when the twin-head pump is to be controlled or
monitored by a Grundfos pump management
system.
• in all other situations where the master and slave
pumps are to operate independently of each
other as two single-head pumps.
7.2.2 R100 remote control
Single-pump operation is to be selected with the
R100. See section 8.6.6 Twin-head pump.
7.2.3 Operation in parallel
In single-head operation mode, the pumps must
never run at the same time, unless the pump is
controlled by a Grundfos pump management system.
7.2.4 Setting the slave pump
When single-pump operation mode has been
selected, the slave pump settings will correspond to
the settings of the last working pump.
TM00 5546 4596TM04 4629 1809
H
set
H
set
H
set
Proportional
pressure
Constant
pressure