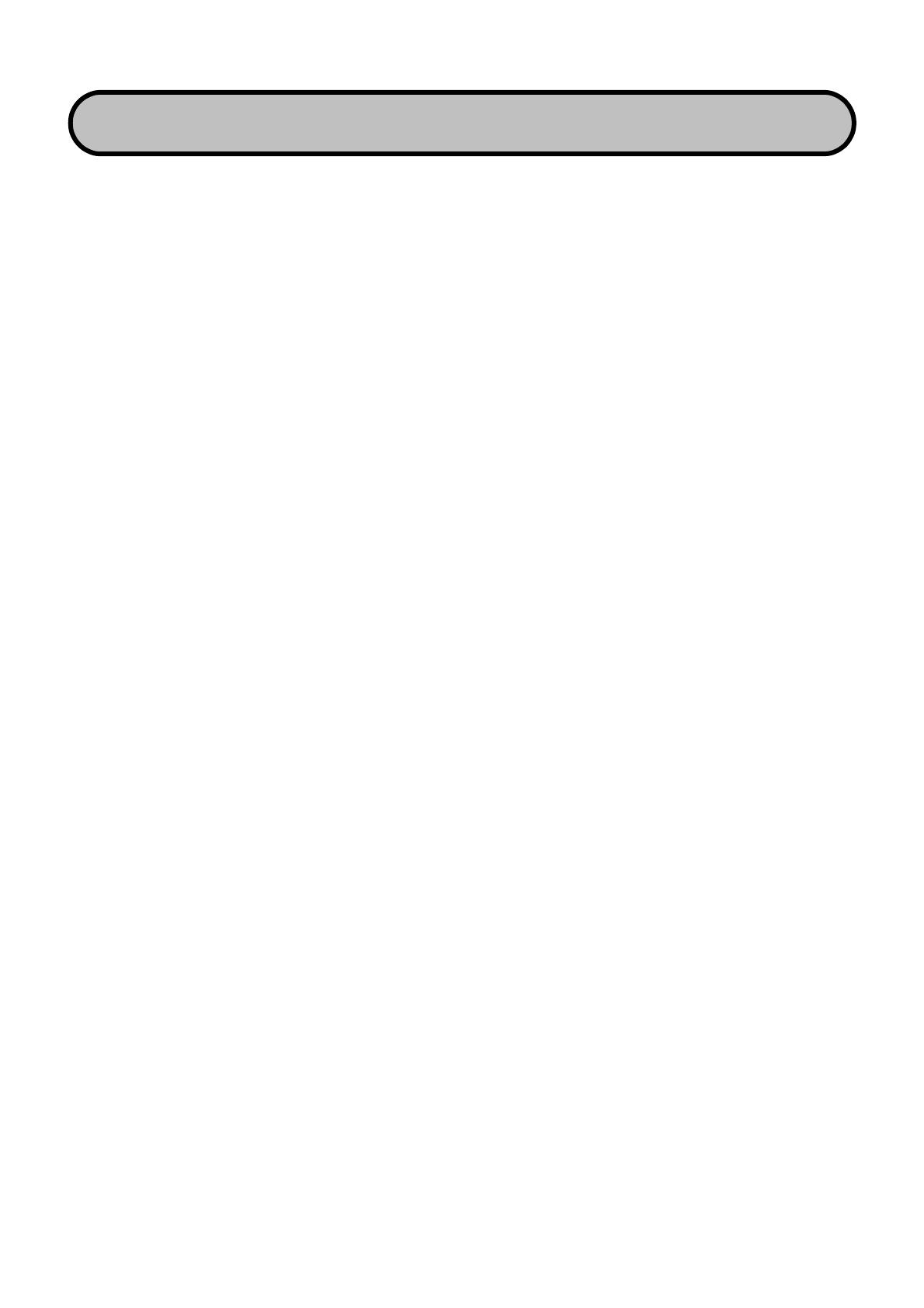
Contents
Strato-charged Engine
1. Outline ............................................................................................................... 1
2. Operating Principle ............................................................................................. 2
Construction
1. Engine Short Block Parts ................................................................................... 3
2. Recoil and Clutch Parts ...................................................................................... 4
3. Right Handle and Carburetor Parts .................................................................... 5
4. Chain Brake Parts .............................................................................................. 6
Specifications and Technical Data
.................................................................... 7
Service Guide
1. Teardown
1-1 Carburetor Removal .................................................................................... 8
1-2 Recoil Assy. Removal .................................................................................. 9
1-3 Handle Comp. Removal .............................................................................. 9
1-4 Spark Plug Removal .................................................................................. 10
1-5 Rotor Removal .......................................................................................... 10
1-6 Module Removal ....................................................................................... 10
1-7 Clutch Removal ......................................................................................... 11
1-8 Oil Pump Removal .................................................................................... 11
1-9 Inlet Pipe Removal .................................................................................... 12
1-10 Muffler Removal ...................................................................................... 12
1-11 Engine Short Block Removal ................................................................... 13
1-12 Crank Shaft Removal .............................................................................. 14
2 Reassembly
2-1 Engine Short Block Assembly .................................................................... 15
2-2 Heat-resistant Gasket Assembly ............................................................... 16
2-3 Inlet Pipe Assembly ................................................................................... 16
2-4 Worm Gear Assembly ............................................................................... 17
2-5 Clutch Assembly ........................................................................................ 17
2-6 Rotor Assembly ......................................................................................... 17
2-7 Module Assembly ...................................................................................... 18
2-8 Handle Comp. Assembly ........................................................................... 18
2-9 Switch Cord and Earth Cord Wiring ........................................................... 19
2-10 Carburetor Assembly ............................................................................... 20
2-11 Fan Cover Assembly ............................................................................... 20
Carburetor
1. Specifications
1-1 Carburetor Specifications .......................................................................... 21
1-2 Recommended Tools ................................................................................. 21
1-3 Construction .............................................................................................. 22
1-4 Carburetor Conforms to Exhaust Emissions Regulations .......................... 23
2. Carburetor Adjustment
2-1 Required Tools and Parts .......................................................................... 24
2-2 Pre Adjustment Check List ........................................................................ 24
2-3 Adjustment ................................................................................................ 24