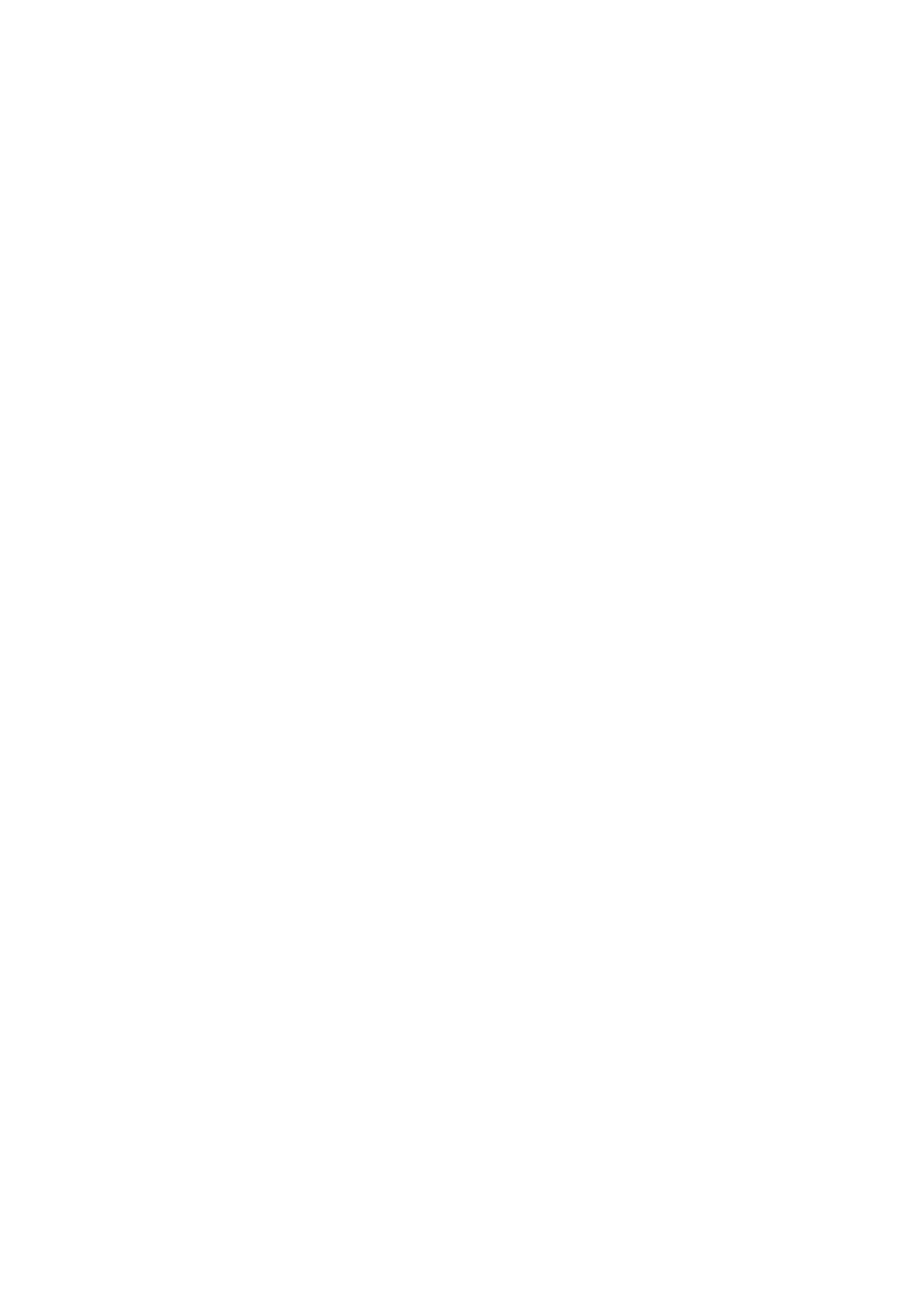
6 SDI-12 Commands and Answers
6.1 Standard commands
The following SDI-12 standard commands are implemented in the SE 200:
Command Answer Description
a! a<CR><LF> Acknowledgment active
aI! allccccccccmmmmmm… Send identification
…vvvxxxx<CR><LF> SE 200 Answer = …OTTHYDRO0000820.03
aAb! b<CR><LF> Change address
?! a<CR><LF> Query address
aM! atttn<CR><LF> Start measurement
aD0! a<values><CR><LF> Send data
aC! atttnn<CR><LF> Start simultaneous measurement
More information on the SDI-12 standard commands can be found in the document
SDI-12; A Serial-Digital Interface Stan-
dard for Microprocessor-Based Sensors; Version 1.2
(see Internet page
www.sdi-12.org
).
6.2 Extended SDI-12 Commands
All extended SDI-12 commands begin with an
O
for
OTT
. With these commands, it is possible to configure the SE 200
through the transparent mode of a datalogger.
Command Answer Description
– Adjust/read units
aOU<value>! aOU<value><cr> Adjust units
aOU! aOU<value><cr> Read out unit
a– Sensor address
<value> – Unit
0= m
1= cm
2= ft
– Set measured value to 0
aOZ! aOZOK<cr> Set measured value to 0 at the current float pulley
position
a– Sensor address
– Adjust/read rotational direction
aOR<value>! aR<value><cr> Adjust rotational direction
aOR! aR<value><cr> Read out rotational direction
a– Sensor address
<value> – Rotational direction
0= to the right
1= to the left
– Adjust/read float pulley circumference
aOC<value>! aC<value><cr> Adjust float pulley circumference
aOC! aC<value><cr> Read out float pulley circumference
a– Sensor address
<value> – b.a
b– Digit prior to the decimal point
b– Digit after the decimal point
Number of spaces: 5 (4 digits + decimal point)
Note the following settings for the units
m →bbb.a Input in mm (001.0 … 999.9)
cm →bbb.a Input in mm (001.0 … 999.9)
ft →b.aaa Input in feet (0.001 … 9.999)