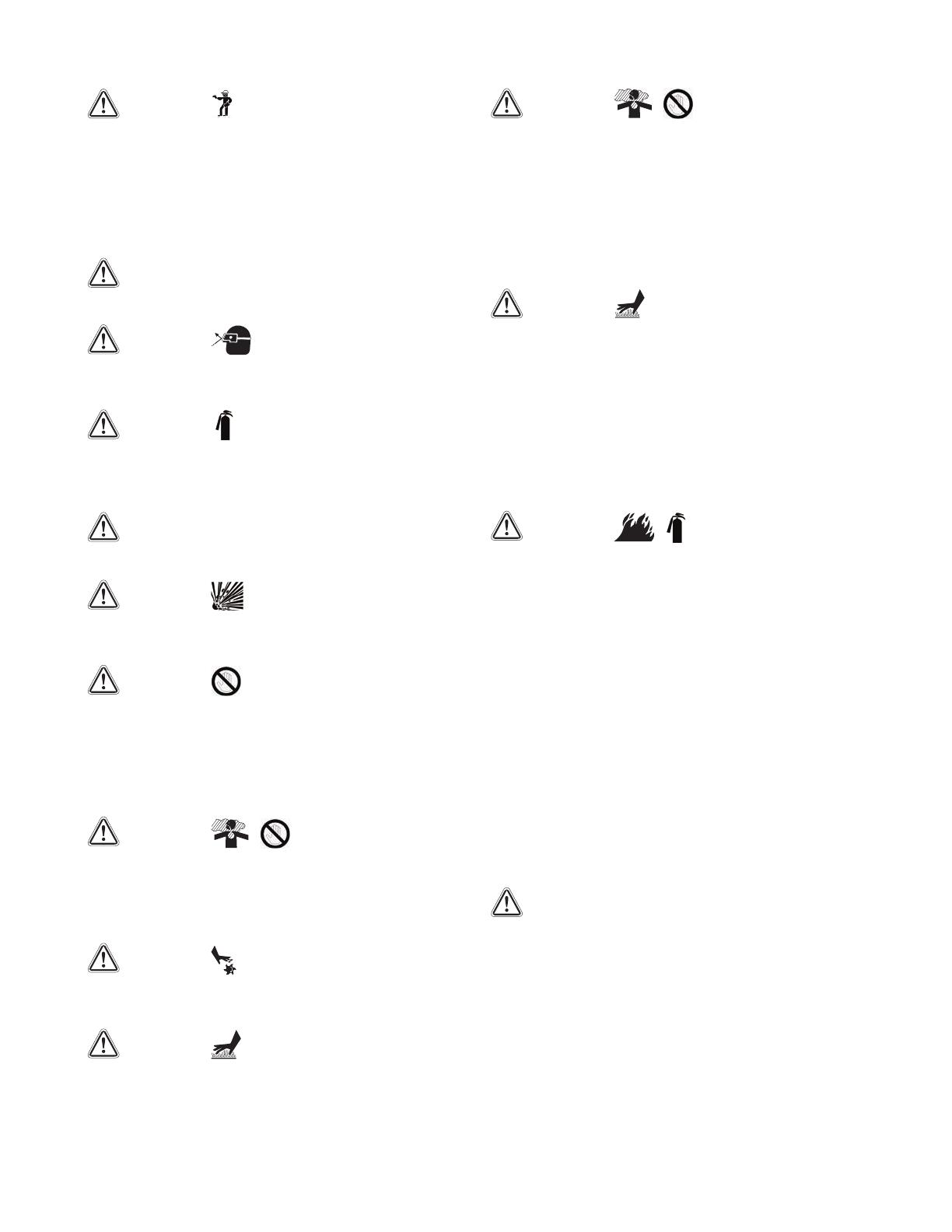
5
WARNING When operating machine, do
not wear:
• Loose clothes
• Clothes with unbuttoned sleeves
• Hanging tie or scarf
• Accessories such as dangling jewelry
• Such items could be caught in rotating parts of
machine, and could result in death or serious injury.
WARNING Do not operate machine when
tired or under influence of drugs or alcohol. Careless
operation could result in death or serious injury.
WARNING Wear appropriate personal
protective equipment (PPE), such as a helmet, safety
glasses, earplugs, safety shoes, gloves, and a dust
mask.
WARNING Have first-aid boxes and fire
extinguishers near machine in case of emergency
such as injury and fires. It is also advisable to have a
list of phone numbers of doctors, ambulance and fire
department available in case of emergency.
WARNING To prevent injury, tools, cables,
hoods, covers and other unnecessary items should be
cleaned and removed from machine before operation.
WARNING Do not open oil filler cap of
separator receiver tank during or immediately after
operation. Explosive pressure could cause death or
serious injury.
WARNING Do not open fluid drain valves
or plugs during operation. this includes:
• Separator receiver tank drain valve
• Coolant drain valve and plug
• Engine oil drain valve
• Oil cooler drain valve
• Fuel tank drain valve and plug
WARNING Never direct
compressed air at people, pets or foods:
• Never blow compressed air directly at people. Dirt,
dust, oil or foreign objects in compressed air could
cause serious injury to eyes and skin.
• Do not blow compressed air on food.
WARNING Contact with rotating parts
or belts could cause death or serious injury. Keep
hands from rotating parts and belts while machine is in
operation.
WARNING Do not open radiator cap
during or immediately after operation. Explosive
pressure of hot liquid could cause severe burns,
resulting in death or serious injury.
WARNING Operation with
compressed air supply port opened is prohibited:
• Do not operate machine with service valves and/
or relief valve open, unless piping and/or hose is
connected. Uncontrolled pressurized air could cause
death or serious injury.
• If machine must be temporarily operated with port
open, be sure to mount a silencer to reduce noise,
and wear personal protective equipment such as
earplugs to protect hearing.
WARNING Do not touch hot parts.
• Never work nearby hot portions of the machine while
it is running.
• Parts such as engine, exhaust manifold, exhaust
pipe, muffler, radiator, oil cooler, air-end, pipe,
separator receiver tank, and discharging pipe are
especially hot. Never touch these parts, as it could
result in serious burns.
• Compressor oil, coolant water, and engine oil are also
very hot and dangerous to touch. Do not check or
add while machine is running.
WARNING Fire prevention.
• Fuel and oils are extremely flammable. Do not
bring lit cigarettes or matches near machine when
checking or adding fuel and oils.
• Adding fuel and oils should be done outdoors or in a
well-ventilated location.
• Refuel after stopping engine, and never leave
fuel near machine. Do not spill. If spilled, wipe up
completely.
• Do not fill fuel oil up to cap level. Fuel oil will overflow
due to volume expansion caused by rise of ambient
temperature. Fuel can also spill during machine
movement or transporting.
• Parts such as muffler and exhaust pipe can be
extremely hot. Remove twigs, dried leaves, dried
grass, waste paper, etc. from around muffler and
exhaust pipe.
• Keep a fire extinguisher available by machine in case
of fire.
WARNING Hang a “Now Checking and under
Maintenance” tag:
• Remove starter key from starter switch before
starting inspection, and hang up a “Now Checking
and under Maintenance” tag where it can be easily
seen. Inspector must keep key during checking and
maintenance.
• Remove black negative (–) cable from battery.
• Neglecting above procedure could result in death or
serious injury.