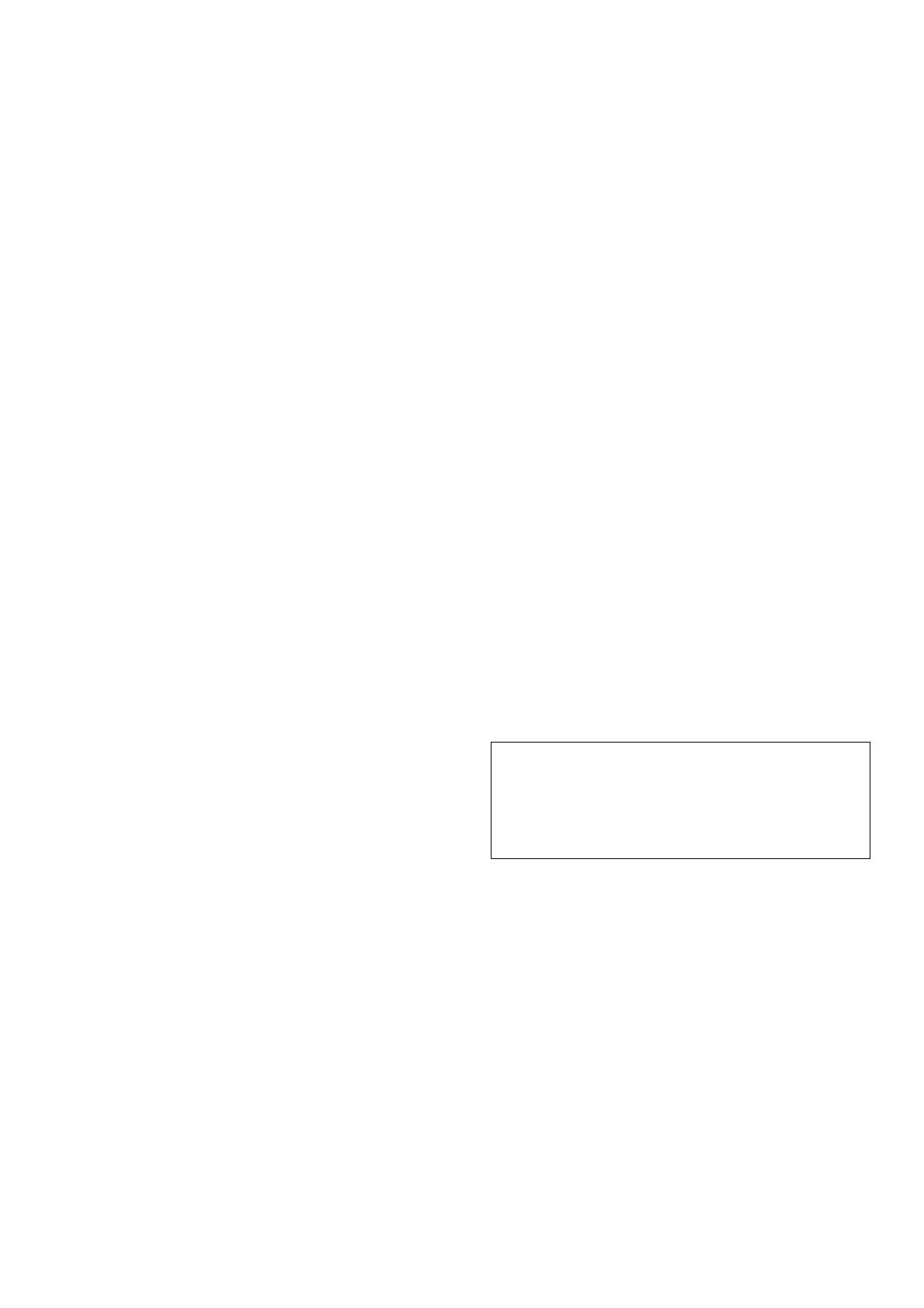
10
High-Level Balanced Flue Kit (2357)
Before commencing assembly, please make sure that you have correctly identified the placement of each pipe section and
that all ‘O’ ring seals are in position and well-lubricated. Any white pipe exposed to the elements should be protected with a
suitable material. Place all weld seams to the rear.
ASSEMBLY METHOD
Before assembly, determine the length of flue required and if
necessary discard the mid-section. See "alternative vertical
lengths" (adjacent) for details of different flue lengths.
1. Having decided the position of the boiler, cut a hole
130mm diameter in the wall. Refer to fig 6 and "alternative
flue heights" for high level flue positions.
2. Remove the boiler top casing and the conventional-flue
socket. Ensure the flue gasket remains in position.
3. Refer to fig 5; place items 8, 7, 6 & 5 in order onto the top
of the boiler. Secure with the nuts provided. Ensure all 'O'-
ring seals (item 9) are in position on all sections of pipe.
Apply a bead of lubricant around each 'O'-ring.
4. Fit the lower flue section (item 4) to the spigot (item 6),
now situated on top of the boiler, ensuring the 'O'-ring
creates a good seal. Ensure the hose connection on the
white outer pipe is directed to the front of the boiler.
5. Fit the flue mid-section (item 3) to the lower flue section in
the same manner, pushing firmly down until the outer
sections meet. Use the clamping strap (item 2) to fasten
these items securely together.
6. Ensuring that all 'O'-ring seals are in position and well-
lubricated, fit the elbow (item 1, fig 4) from the horizontal
balanced flue kit to the top of the flue mid-section, pushing
firmly together until the outer sections meet. Use the
clamping strap to fasten these items securely together.
7. Decide the length of horizontal run required and slide the
terminal (item 4, fig 4) into the horizontal mid-section
(item 2, fig 4). Once in the required position (and ensuring
that at least 140mm will project from the outside wall), seal
these items together using a suitable material.
8. Ensuring that all 'O'-rings are in position, slide the
completed terminal assembly through the wall and fit to
the flue elbow, pushing firmly together until the outer
sections meet. Use the remaining clamping strap to fasten
these items securely together.
9. Use the clip provided to secure the air hose from the
burner to the connection on the lower flue section.
10. Cut the tabs from the hole in the boiler top casing and fit
the casing into position. Perform a final check of the flue.
Ensure all clamping straps are located over all relevant
flue joints.
11. Seal any remaining gaps in the wall around the horizontal
flue section with a suitable material.
ALTERNATIVE FLUE HEIGHTS
Should the height of the flue (see fig 6) not meet your
requirements, alternative arrangements can be made. The
vertical mid-section (item 3, fig 5) can be discarded to
subtract 760mm from the total height. The horizontal section
should instead be fitted to the short vertical section, using
the clamping strap provided.
Alternatively, purchase additional sections of flue pipe to
extend the vertical distance. See page 14 for details.
ALTERNATIVE HORIZONTAL LENGTHS
Should the horizontal length of the standard flues not meet
your requirements, an additional section of flue pipe can be
purchased to extend the maximum wall thickness limit. See
page 14 for details.
ADDITIONAL ELBOWS
When used in conjunction with additional horizontal lengths
of flue, 45º and 90º elbows can be purchased in order to
offset the flue on the horizontal plane. See page 14 for
details.
Additional 45º elbows can be purchased to offset the vertical
sections of flue. 90º elbows cannot be used on the vertical
sections. See page 14 for details.
IMPORTANT: When used on boilers of outputs 90,000
Btu/h or less, the total flue distance, vertical and horizontal,
must not exceed 6000mm. Flues used on boilers of outputs
above 90,000 Btu/h must not exceed 4240mm. Any 45º
elbows used in the assembly contribute 500mm to the
calculation. 90º elbows contribute 1000mm to the
calculation.
To ensure that any condensate produced in the flue drains
away correctly, incline the flue slightly upwards from the
boiler.
TERMINAL GUARD
Where the terminal is positioned in a place where there is
the possibility of contact being made by persons, of damage
to the terminal, or if it is lower than 2 metres from ground
level, an approved terminal guard is necessary.
Generally, exhaust 2 metres above ground level will
alleviate the requirement for a terminal guard.
A suitable stainless steel terminal guard is available from
Trianco (part code 223920).