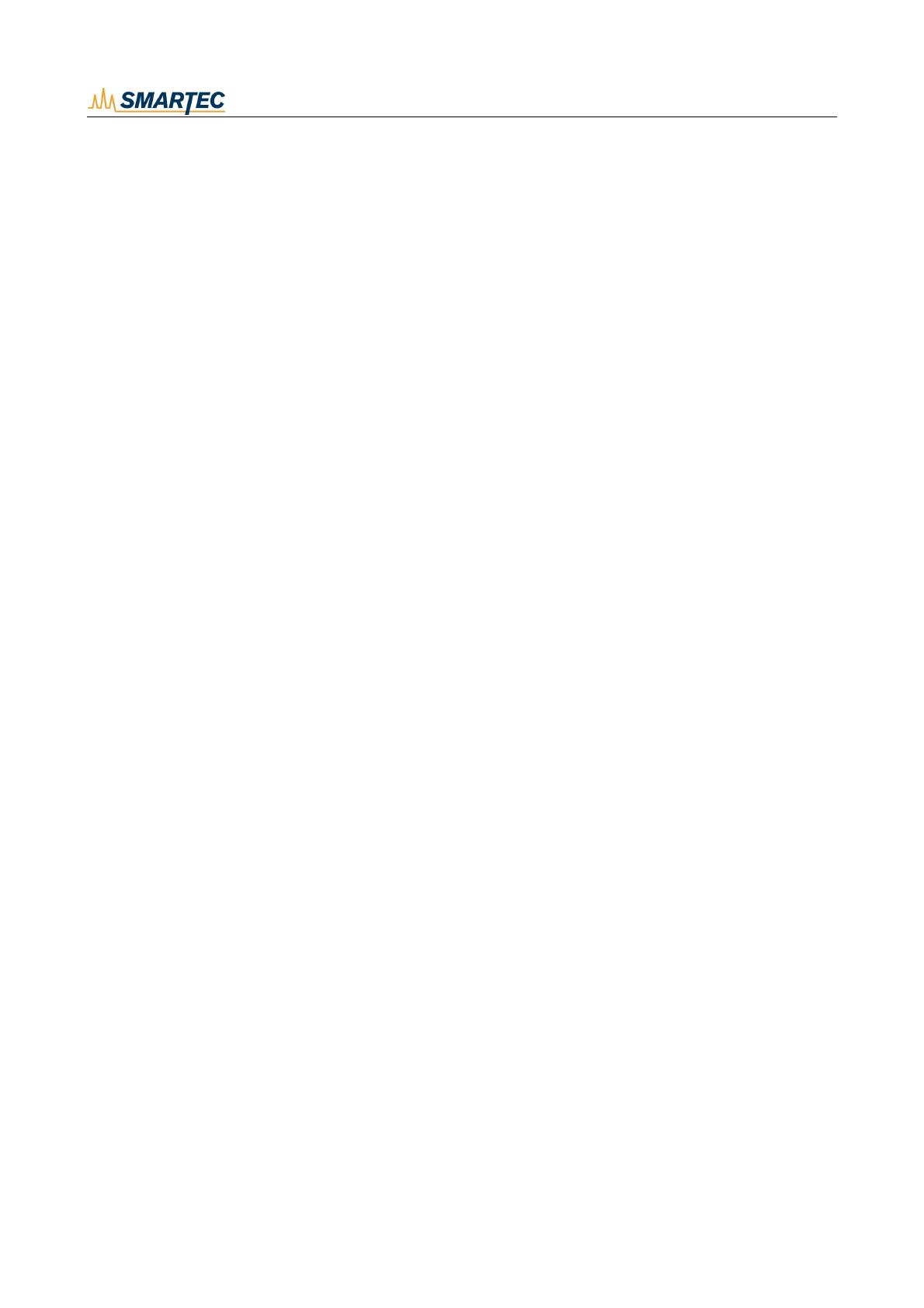
1 Technical details .......................................................................................... 5
1.1 General Information........................................................................................ 5
1.2 System Components ...................................................................................... 5
1.3 MuST VII Dynamic Technical Data .................................................................. 6
1.3.1 Performance .................................................................................................. 6
1.3.2 Technical Characteristics ................................................................................ 6
2 Regulatory and Certification Considerations ............................................... 7
2.1 Environment Considerations ........................................................................... 7
2.1.1 Disposal of your Old Appliance........................................................................ 7
2.2 Laser Safety .................................................................................................. 7
2.2.1 Symbols ........................................................................................................ 8
2.2.2 Class 1 Laser ................................................................................................. 8
2.2.3 General Precautions ....................................................................................... 9
3 Operation ................................................................................................... 10
3.1 Connectors .................................................................................................. 10
3.1.1 Type of connectors ....................................................................................... 11
3.2 Setting Up.................................................................................................... 11
3.2.1 Power supply ............................................................................................... 11
3.2.2 Optical connectors ....................................................................................... 12
3.2.3 Bottom plate ................................................................................................ 13
3.3 Switching On ............................................................................................... 13
3.3.1 Internal PC .................................................................................................. 13
3.3.2 Acquisition Module ....................................................................................... 13
3.4 Switching OFF ............................................................................................. 14
3.4.1 Internal PC .................................................................................................. 14
3.4.2 Acquisition Module ....................................................................................... 14
3.5 Power and Status LEDs ................................................................................ 14
3.5.1 Power LED .................................................................................................. 14
3.5.2 Status LED .................................................................................................. 14
3.6 Interface ...................................................................................................... 15
3.7 Control ........................................................................................................ 15
3.8 Cleaning Procedure...................................................................................... 15
3.8.1 Dry cleaning technique ................................................................................. 18
3.8.2 Wet cleaning technique ................................................................................ 20
3.9 Fuse Replacement ....................................................................................... 22
4 DynamicMONITOR Software ...................................................................... 24